Blood Collection Tube Manufacturing Plant Project Report 2025: Key Insights and Plant Setup
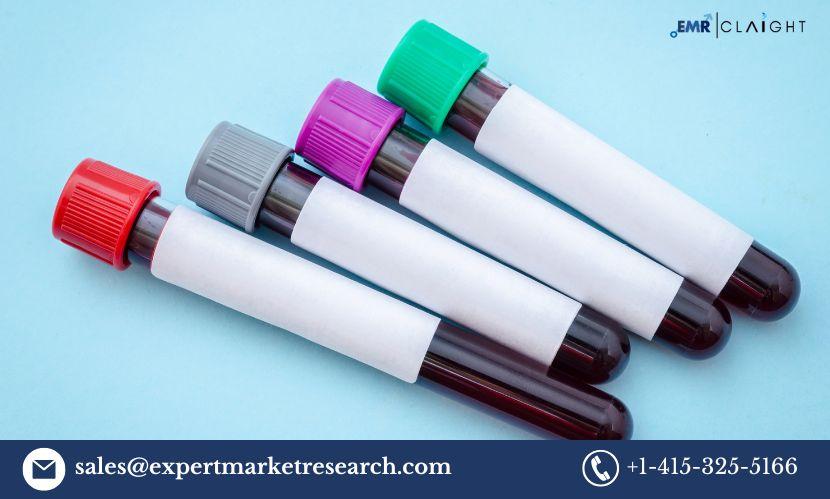
Introduction
Blood collection tubes, commonly referred to as vacutainers, are essential medical devices used for collecting, storing, and transporting blood samples. These tubes are integral to various medical and laboratory procedures, such as diagnostic tests, blood typing, and research. The Blood Collection Tube Manufacturing Plant is a facility dedicated to producing these crucial medical instruments in large volumes, ensuring that healthcare systems and diagnostic laboratories have a consistent supply. In this Blood Collection Tube Manufacturing Plant Project Report, we will explore the key components of setting up a blood collection tube manufacturing plant, including market demand, production processes, required equipment, regulatory compliance, and financial considerations. Understanding the nuances of blood collection tube production can help manufacturers navigate the complexities of this sector and capitalise on the growing demand for diagnostic services and medical testing.
Market Overview
1. Demand for Blood Collection Tubes
The global healthcare sector has seen significant growth, particularly in the field of diagnostics, driving an increase in the demand for blood collection tubes. These tubes are used for various applications, such as:
- Clinical Laboratories: Blood collection tubes are vital for conducting routine blood tests, such as complete blood counts (CBC), blood glucose levels, and cholesterol tests.
- Hospitals and Clinics: Hospitals rely heavily on blood collection tubes for diagnostic testing and transfusions.
- Research and Development: Blood collection tubes are used in clinical trials and research studies for the collection of blood samples.
- Forensic and Blood Bank Operations: Blood collection tubes are used in forensic laboratories for analysis and in blood banks for storage.
The global market for blood collection tubes is expected to expand due to the increasing emphasis on diagnostic tests, rising healthcare expenditure, and advances in medical research. With the increase in chronic diseases, ageing populations, and the demand for healthcare services, the production of blood collection tubes is projected to grow at a steady pace.
Get a Free Sample Report with Table of Contents@
2. Market Trends
- Technological Advancements: Innovations in blood collection tube designs, such as safety features (e.g., retractable needles) and anti-coagulant additives, are expected to drive market growth.
- Standardisation and Quality Control: Increasing regulatory demands for uniformity in blood collection tube production, focusing on sterility, material quality, and labelling accuracy.
- Emerging Markets: Developing regions, such as Asia-Pacific, Africa, and Latin America, are witnessing a growing demand for blood collection tubes due to expanding healthcare infrastructure and rising disease prevalence.
- Automation and Smart Manufacturing: The adoption of automated production lines and robotics to improve efficiency, reduce human error, and lower production costs.
3. Regulatory Framework
Blood collection tubes, being medical devices, are subject to strict regulatory standards to ensure they are safe and effective for use. These regulations include:
- Food and Drug Administration (FDA): In the U.S., blood collection tubes are regulated by the FDA under the 21 CFR 880 guidelines, which specify requirements for medical devices.
- European Medicines Agency (EMA): In Europe, blood collection tubes must comply with the Medical Device Regulation (MDR), ensuring that they meet essential safety and performance standards.
- International Organization for Standardization (ISO): Manufacturers must adhere to ISO 13485 certification, which focuses on quality management systems for medical devices.
- Good Manufacturing Practices (GMP): Compliance with GMP is required for ensuring that the production of blood collection tubes meets the necessary quality standards, and they are manufactured in a controlled environment.
Non-compliance with these regulations can lead to serious repercussions, including product recalls, legal issues, and damage to brand reputation. Therefore, regulatory compliance must be a priority throughout the manufacturing process.
Manufacturing Process
1. Raw Materials
The primary raw materials used in the production of blood collection tubes are:
- Glass or Plastic Tubes: These are the base material of the blood collection tubes. Glass tubes are more common in certain segments due to their non-reactive properties, while plastic tubes are increasingly preferred due to their lower cost and durability.
- Additives: Various additives are used in blood collection tubes, including anti-coagulants (such as EDTA, heparin, or sodium citrate), which prevent blood clotting and ensure accurate test results.
- Rubber Stoppers or Caps: These seal the tubes, ensuring that blood samples are securely contained during transportation and storage.
- Labels: Accurate labelling is crucial for identifying patient information and sample details, ensuring traceability and avoiding mix-ups.
2. Production Process
The manufacturing process for blood collection tubes involves several key stages:
Tube Formation
The first step involves extrusion or blow-moulding of the tube material. For glass tubes, the process typically involves heating glass tubes and shaping them into the desired size and thickness. For plastic tubes, the process may involve extrusion or blow-moulding of polymer resins such as polyethylene or polypropylene into cylindrical shapes.
Surface Treatment
Once the tubes are formed, they undergo surface treatment to improve their adhesion to additives like anti-coagulants or preservatives. This process may involve chemical treatments or flame polishing for glass tubes to ensure smooth surfaces.
Additive Dispensing
Next, the required additive is added to the tubes. Anti-coagulants or other substances are dispensed in precise amounts, either as a liquid or powder, depending on the type of additive and the tube specifications.
Sealing and Capping
The tubes are sealed with rubber stoppers or plastic caps to prevent contamination and ensure secure storage of the blood sample. The sealing process is critical in ensuring the safety and stability of the sample.
Sterilisation
Once the tubes are sealed, they undergo sterilisation. This is typically done using gamma radiation or ethylene oxide (ETO) to ensure that the tubes are free from any microbial contamination before being used for medical purposes.
Labelling
After sterilisation, the tubes are labelled with the necessary patient or product information. Labels include crucial details such as lot numbers, expiration dates, and safety warnings to comply with medical standards and regulatory requirements.
Packaging
The final step involves the packaging of blood collection tubes into sterile packaging to maintain the sterility and prevent damage during transportation. Tubes may be packaged individually or in bulk, depending on the intended use.
3. Quality Control
Quality control is essential in ensuring that blood collection tubes meet industry standards and are free from defects. Key quality checks include:
- Tube integrity: Ensuring that the tubes are free from cracks, leaks, or other defects.
- Additive consistency: Verifying that the correct quantity of anti-coagulant or other additives is included in each tube.
- Sterility testing: Conducting microbial tests to ensure that the tubes are sterile and safe for medical use.
- Sealing integrity: Verifying that the rubber stoppers or caps are securely attached to prevent leakage.
Plant Design and Layout
1. Raw Material Storage
The raw materials, including glass or plastic tubing, additives, and rubber stoppers, should be stored in climate-controlled environments to ensure their integrity.
2. Production Area
The production area should be divided into different sections for tube formation, surface treatment, additive dispensing, sealing, and sterilisation. This layout ensures that each stage of production is optimised for efficiency and quality control.
3. Sterilisation and Packaging Area
A dedicated area for sterilisation and packaging is essential to maintain sterility and ensure that finished products are sealed and labelled correctly.
4. Quality Control Lab
A quality control lab should be set up for testing and inspecting raw materials and finished products to ensure compliance with medical standards.
5. Waste Management
The facility should have an effective waste management system to handle production waste, including any defective products, packaging materials, or used chemicals.
Cost and Financial Considerations
1. Capital Investment
Setting up a blood collection tube manufacturing plant requires significant capital investment. The major costs include:
- Facility setup (building, equipment, utilities)
- Machinery and equipment (extrusion machines, moulding machines, sterilisation units, packaging lines)
- Raw materials (glass or plastic tubing, rubber stoppers, additives)
2. Operating Costs
The operating costs of the plant include:
- Raw materials: The cost of sourcing and purchasing glass, plastic, and additives.
- Labor costs: Wages for production workers, quality control technicians, and administrative staff.
- Energy consumption: The cost of utilities such as electricity and water for production processes.
- Regulatory compliance costs: Expenses for certifications, inspections, and audits.
3. Revenue Generation
The revenue for the manufacturing plant primarily comes from the sale of blood collection tubes to hospitals, clinics, laboratories, and research institutions. The plant can also explore contract manufacturing agreements with healthcare providers and distributors.
Opportunities and Challenges
1. Opportunities
- Growing demand for diagnostic testing: As healthcare systems and diagnostic procedures grow, the demand for blood collection tubes is expected to rise.
- Product differentiation: Introducing innovative features such as safety-engineered tubes (e.g., retractable needles) can differentiate the product line and capture a niche market.
- Emerging markets: There is an increasing demand for medical supplies in developing countries, offering expansion opportunities.
2. Challenges
- Regulatory hurdles: Meeting stringent regulatory requirements can be time-consuming and costly.
- Raw material costs: The price of raw materials such as glass or high-quality plastic can fluctuate, affecting profitability.
- Competition: The blood collection tube market is highly competitive, with several established players.
FAQ
1. What are the primary uses of blood collection tubes?
Blood collection tubes are used in clinical laboratories, hospitals, and research for drawing, storing, and transporting blood samples for diagnostic tests.
2. What materials are used to make blood collection tubes?
Blood collection tubes are typically made from glass or plastic materials, with additives like anti-coagulants or preservatives to prevent blood clotting.
3. Is there a demand for blood collection tubes in emerging markets?
Yes, developing regions like Asia-Pacific, Africa, and Latin America are witnessing an increasing demand for blood collection tubes due to the expansion of healthcare infrastructure.
Media Contact
Company Name: Claight Corporation
Contact Person: Lewis Fernandas, Corporate Sales Specialist — U.S.A.
Email: sales@expertmarketresearch.com
Toll Free Number: +1–415–325–5166 | +44–702–402–5790
Address: 30 North Gould Street, Sheridan, WY 82801, USA
Website: www.expertmarketresearch.com
Aus Site: https://www.expertmarketresearch.com.au
- Art
- Causes
- Crafts
- Dance
- Drinks
- Film
- Fitness
- Food
- Игры
- Gardening
- Health
- Главная
- Literature
- Music
- Networking
- Другое
- Party
- Religion
- Shopping
- Sports
- Theater
- Wellness