Machine Condition Monitoring Market: Driving Efficiency and Reliability in Industrial Operations
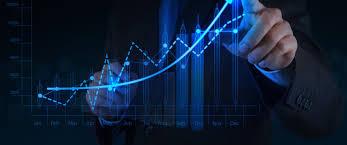
The Global Machine Condition Monitoring Market Demand is gaining significant momentum as industries prioritize operational efficiency, predictive maintenance, and equipment reliability. Condition monitoring technologies are evolving rapidly, fueled by advancements in sensors, data analytics, and Industrial Internet of Things (IIoT).
Market Overview
Machine condition monitoring involves tracking the health and performance of machinery to detect potential failures and optimize maintenance schedules. Technologies such as vibration analysis, thermography, and ultrasound detection are widely used to monitor equipment in real time, reducing downtime and repair costs.
The Machine Condition Monitoring Market size was valued at USD 2.61 Billion in 2023. It is estimated to reach USD 5.27 Billion by 2032, growing at a CAGR of 8.14% during 2024-2032. Key factors driving this growth include the rising adoption of predictive maintenance strategies, increasing industrial automation, and the integration of AI and IoT technologies.
Get a Sample Copy of this Research Report https://www.snsinsider.com/sample-request/1552
Top Key Players
Emerson Electric Co, Rockwell Automation Inc, Analog Devices Inc., Amphenol Inc., National Instruments Corp, Fluke Corporation, General Electric, Parker Hannifin Corp, SKF, Allied Reliability, Meggitt PLC
Current Trends in the Machine Condition Monitoring Market
- Shift Toward Predictive Maintenance
Predictive maintenance is gaining traction as industries move from reactive and preventive approaches. Machine condition monitoring enables early detection of anomalies, helping to prevent unexpected failures and optimize operational efficiency. - Integration with IIoT
The Industrial Internet of Things (IIoT) is revolutionizing condition monitoring by enabling real-time data collection and analysis. Wireless sensors, cloud computing, and edge analytics are streamlining monitoring processes and improving accuracy. - AI and Machine Learning in Analytics
AI-powered analytics are being integrated into condition monitoring systems, offering enhanced diagnostic capabilities and predictive insights. Machine learning algorithms can identify complex patterns in data, enabling more accurate failure predictions. - Increased Adoption in Renewable Energy
The renewable energy sector, including wind and solar power, is adopting condition monitoring systems to ensure the reliability of critical components such as turbines and inverters. - Demand for Portable and Wireless Solutions
Portable and wireless condition monitoring devices are gaining popularity due to their flexibility, ease of deployment, and cost-effectiveness. These solutions are particularly beneficial in remote and hard-to-reach industrial settings.
Segmentation Analysis
- By Technique:
- Vibration Monitoring: Uses sensors to detect abnormal vibrations in machines, helping to identify wear, misalignment, and imbalance.
- Thermography: Involves the use of infrared cameras to monitor temperature variations in machinery, indicating overheating or inefficiency.
- Oil Analysis: Involves testing lubricants for contamination and wear particles to assess the health of machinery.
- Corrosion Monitoring: Detects the presence of corrosion in machinery and structures, helping to prevent failures due to material degradation.
- Ultrasound Emission Monitoring: Uses high-frequency sound waves to detect leaks, air bubbles, and other irregularities in machines.
- Motor Current Analysis: Monitors the motor current to detect issues like imbalance, unbalance, and fault in motors.
- By Deployment:
- On-Cloud: Condition monitoring systems hosted on cloud platforms, enabling remote monitoring, data storage, and analysis with greater scalability.
- On-Premises: Monitoring systems deployed within the organization’s premises, offering direct control and security but limited scalability compared to cloud solutions.
- By Process:
- Online Condition Monitoring: Continuous, real-time monitoring of machinery and equipment using sensors and IoT devices, often with predictive maintenance capabilities.
- Portable Condition Monitoring: Equipment that can be manually carried to different machines or locations for periodic monitoring, providing flexibility in smaller or temporary setups.
- By Industry:
- Manufacturing: Machine condition monitoring to prevent downtime and improve operational efficiency in factories and production lines.
- Oil & Gas: Monitoring of heavy machinery, pumps, and pipelines to ensure smooth operations in upstream, midstream, and downstream activities.
- Energy & Power: Includes monitoring of turbines, generators, and other critical assets in power plants for optimized performance and reduced risk.
- Automotive: Used in automotive production plants and for predictive maintenance in vehicles.
- Aerospace & Defense: Monitoring of machinery in aerospace manufacturing, aircraft, and defense equipment for safety and reliability.
- Food & Beverage: Ensuring machine health in food processing plants to maintain production quality and reduce the
Regional Analysis
- North America
North America leads the market, driven by its advanced industrial infrastructure, early adoption of IIoT technologies, and a strong focus on predictive maintenance. The U.S. is a major contributor to the region's growth. - Europe
Europe is witnessing significant growth due to stringent regulations on industrial safety, energy efficiency initiatives, and the presence of key manufacturing hubs. Germany, the UK, and France are leading markets in the region. - Asia-Pacific
Asia-Pacific is the fastest-growing region, propelled by rapid industrialization, growing adoption of automation, and increasing investments in smart manufacturing. China, India, and Japan are key players in this market. - Latin America and Middle East & Africa (MEA)
These regions are emerging markets for condition monitoring, with expanding oil & gas, mining, and energy sectors driving adoption. Brazil and Saudi Arabia are notable contributors.
Buy Now Link https://www.snsinsider.com/checkout/1552
Conclusion
The machine condition monitoring market is at the forefront of transforming industrial operations by enhancing equipment reliability and operational efficiency. As industries embrace predictive maintenance and IIoT technologies, the adoption of condition monitoring solutions is set to accelerate.
Future growth will be driven by technological innovations, such as AI-driven diagnostics, wireless sensor networks, and edge computing. Stakeholders in the market have a significant opportunity to develop advanced, scalable, and cost-effective solutions to meet the evolving demands of various industries.
About Us:
SNS Insider is a global leader in market research and consulting, committed to driving the industry forward. Our mission is to provide clients with the insights they need to navigate ever-shifting landscapes. By harnessing innovative methodologies such as surveys, video interviews, and focus groups, we offer timely, accurate market intelligence and consumer insights, empowering you to make informed and confident decisions.
Contact Us:
Akash Anand – Head of Business Development & Strategy
Phone: +1-415-230-0044 (US)
- Machine_Condition_Monitoring_Market_Size
- Machine_Condition_Monitoring_Market_Share
- Machine_Condition_Monitoring_Market_Trends
- Machine_Condition_Monitoring_Market_Technology
- Machine_Condition_Monitoring_Market_Forecast
- Machine_Condition_Monitoring_Market_Demand
- Machine_Condition_Monitoring_Market_Growth
- Machine_Condition_Monitoring_Market_Opportunity
- Machine_Condition_Monitoring_Market_Forecast_2032
- Machine_Condition_Monitoring_Market_Research_Report
- Art
- Causes
- Crafts
- Dance
- Drinks
- Film
- Fitness
- Food
- Παιχνίδια
- Gardening
- Health
- Κεντρική Σελίδα
- Literature
- Music
- Networking
- άλλο
- Party
- Religion
- Shopping
- Sports
- Theater
- Wellness