The Resilience of the MIG TIG ARC Plasma Cutter in Industrial Applications
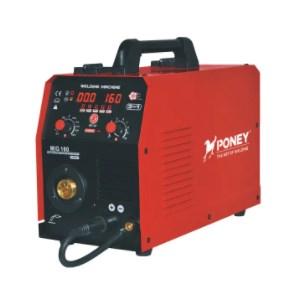
The durability of the MIG TIG ARC plasma cutter is a critical consideration for manufacturers and end-users alike. These versatile tools are the backbone of many industrial processes, from automotive repair to heavy machinery fabrication. The longevity of these devices directly impacts operational efficiency, cost-effectiveness, and overall user satisfaction.
MIG (Metal Inert Gas) welding is known for its ease of use and adaptability to various metal thicknesses. The durability of MIG welding equipment hinges on the quality of its components, such as the wire feeder, torch, and control system. High-quality MIG machines are designed to withstand the rigors of continuous use, with robust construction and reliable electrical systems that ensure consistent performance over time.
TIG (Tungsten Inert Gas) welding, celebrated for its precision and ability to produce high-quality welds, demands equipment that can maintain accuracy and stability. TIG welding machines are often subjected to high temperatures and the need for intricate control. Therefore, the durability of TIG equipment is gauged by the longevity of its tungsten electrodes, the sturdiness of its torch, and the precision of its control mechanisms.
ARC (Atomic Resonance Control) plasma cutters are renowned for their ability to cut through a wide range of materials with exceptional precision. The durability of an ARC plasma cutter is influenced by its power source, torch design, and cooling system. A durable ARC plasma cutter will feature a reliable power supply that maintains a consistent arc, a torch that resists wear from the intense heat of plasma, and an effective cooling system to prevent overheating.
To enhance the durability of the MIG TIG ARC plasma cutter, manufacturers invest in rigorous quality control processes. This includes stress-testing components to ensure they can handle the thermal and mechanical demands of the welding environment. Additionally, the use of high-grade materials in the construction of these machines contributes to their resilience and longevity.
Maintenance is another key factor in the durability of these cutting tools. Regular servicing, which includes cleaning, lubricating, and replacing worn parts, can significantly extend the life of the MIG TIG ARC plasma cutter. Users who follow the manufacturer's maintenance guidelines can expect a longer service life from their equipment.
Innovations in technology also play a role in improving the durability of the MIG TIG ARC plasma cutter. For instance, advancements in power supply technology have led to more efficient and reliable energy delivery, reducing the strain on the machine and contributing to its longevity. Similarly, improvements in torch design have made them more resistant to the corrosive effects of the plasma and the materials being cut.
The user's operating environment can also impact the durability of these machines. Exposure to extreme temperatures, humidity, and dust can accelerate wear and tear. Therefore, it is crucial to use the MIG TIG ARC plasma cutter in appropriate conditions and to take steps to protect them from environmental factors that could shorten their lifespan.
In conclusion, the durability of the MIG TIG ARC plasma cutter is a multifaceted issue that involves the quality of the machine's components, the manufacturer's commitment to quality control, the user's adherence to maintenance protocols, and the operating environment. By focusing on these areas, both manufacturers and users can ensure that these essential tools remain reliable and efficient for as long as possible.
- Art
- Causes
- Crafts
- Dance
- Drinks
- Film
- Fitness
- Food
- Juegos
- Gardening
- Health
- Home
- Literature
- Music
- Networking
- Other
- Party
- Religion
- Shopping
- Sports
- Theater
- Wellness