The Importance of Quality Assurance in PCB Header Connector Production
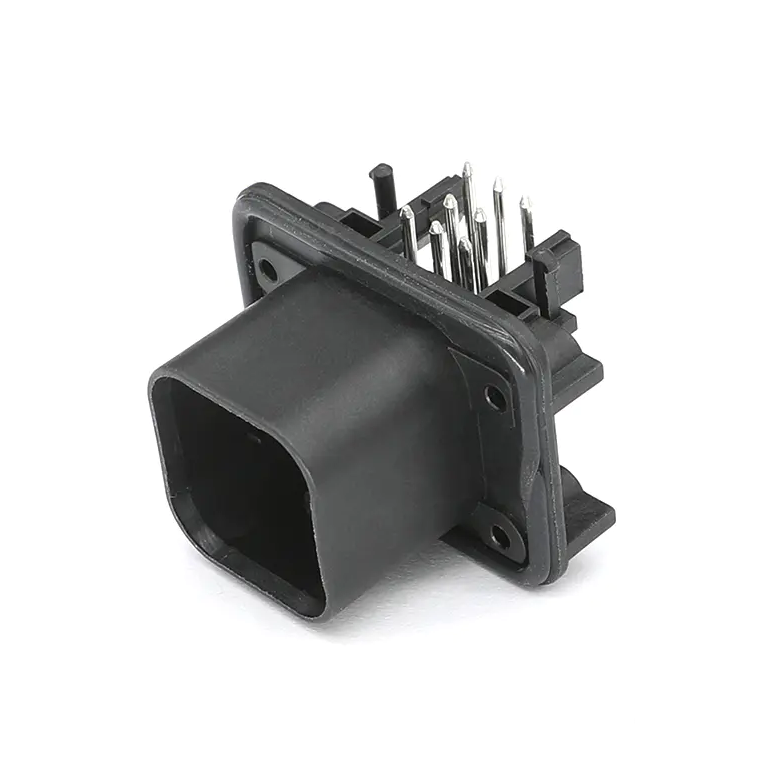
Quality control is a priority for PCB header connector factories. Rigorous testing and inspection processes ensure each product meets performance and reliability standards.
The quality control process begins with raw materials. Factories source high-grade metals and plastics to ensure mechanical strength and electrical conductivity. Incoming materials are inspected for consistency and purity.
During manufacturing, in-process inspections monitor critical parameters. Automated systems check pin alignment, housing integrity, and dimensional accuracy. This real-time monitoring reduces defects and enhances product consistency.
Electrical testing is another essential step. Factories conduct continuity and insulation resistance tests to confirm the connectors perform as intended. High-voltage testing may also be applied for connectors used in demanding environments.
Mechanical stress tests evaluate the durability of connectors under vibration, heat, and repeated mating cycles. These tests ensure the connectors withstand the physical demands of real-world applications.
Final inspections involve visual checks for surface defects, pin misalignment, and plating quality. This comprehensive quality assurance approach minimizes errors and upholds customer trust.
Through stringent quality control, PCB header connector factories deliver reliable components that meet technical specifications and regulatory standards.
- Art
- Causes
- Crafts
- Dance
- Drinks
- Film
- Fitness
- Food
- Games
- Gardening
- Health
- Home
- Literature
- Music
- Networking
- Other
- Party
- Religion
- Shopping
- Sports
- Theater
- Wellness