Mastering PCB Layout Design: Essential Techniques for Experts
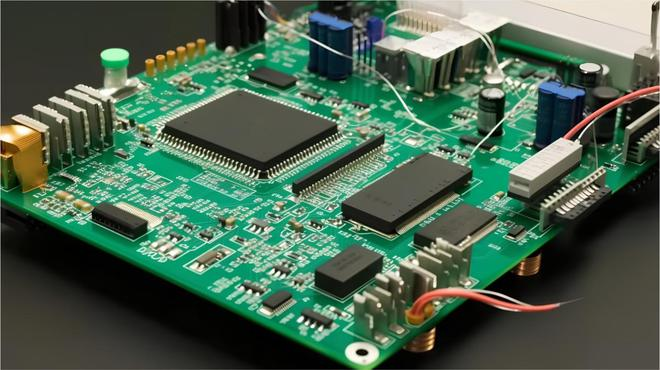
Advanced Strategies in PCB Layout Design
Understanding the Importance of Signal Integrity
Maintaining signal integrity is crucial in PCB Layout Design, for applications involving speeds and frequencies to ensure that the quality of transmitted signals remains intact without any deterioration.
Factors Affecting Signal Integrity
Numerous elements can impact the quality of signals such as impedance disparities leading to reflections due to line discontinuities and crosstalk causing interference, between neighboring traces resulting in performance degradation and noise infiltration.
Techniques to Enhance Signal Integrity
To enhance signal integrity, designers can employ techniques such as impedance matching, proper trace routing, and controlled impedance routing. Impedance matching involves ensuring that the transmission line impedance matches that of the load to minimize reflections. Proper trace routing involves maintaining adequate spacing between traces to reduce crosstalk. Controlled impedance routing ensures consistent impedance across traces.
Thermal Management in PCB Design
Maintaining thermal control is crucial, in the design of PCB layouts to prevent overheating and ensure their reliability.
Heat Dissipation Methods
Methods for managing heat involve the use of vias that move heat from hot components to different parts of the PCB or other layers within it; attaching heat sinks to components to release heat into the surroundings; and using thermal pads that offer a conductive route, for transferring heat from components to heat sinks or other cooling systems.
Thermal Simulation Tools
Designers use simulation tools to forecast how heat spreads on a PCB, in different scenarios and conditions. These tools enable the testing of various thermal management approaches before creating physical prototypes to save both time and resources.
Power Distribution Network Optimization
Optimal management of the power distribution network is essential to ensure voltage levels throughout the printed circuit board.
Designing Efficient Power Planes
Creating a power plane design requires establishing pathways with minimal impedance, for delivering power to reduce voltage drop and preserve signal quality, which can be accomplished by utilizing broader traces or planes and ensuring the correct positioning of decoupling capacitors.
Minimizing Voltage Drop and Noise
To minimize voltage drop it's important to have sized power planes placed near components that need power while reducing noise can be done by placing decoupling capacitors close, to power pins and using ferrite beads or inductors to filter out high-frequency noise.
High-Speed PCB Design Considerations
Designing high-speed PCBs involves the need to carefully address both interference (EMC or EMI) as well, as signal integrity concerns.
Managing Electromagnetic Interference (EMI)
EMC can lead to problems, in fast-paced designs if not handled correctly.
EMI Reduction Techniques
Techniques for reducing EMI include using ground planes, proper trace routing, and filtering components. Ground planes provide a return path for signals, reducing loop areas that contribute to EMI. Proper trace routing minimizes loop areas and reduces radiation.
Shielding and Grounding Practices
To protect circuits, from external interference shielding is used by enclosing them with conductive materials while proper grounding involves establishing a stable ground plane and ensuring all components have a direct path to the ground with minimal impedance.
Implementing Differential Pair Routing
In high-speed designs utilizing differential pair routing helps enhance signal integrity.
Benefits of Differential Pairs
Differential pair configurations provide advantages like decreased vulnerability to interference noise and enhanced signal reliability over extended distances, with superior rejection of common mode noise.
Best Practices for Differential Pair Layout
Some common guidelines involve keeping the lengths of traces for every pair of them and avoiding sharp bends to reduce skewness while ensuring that differential pairs stay closely aligned along their path.
Component Placement and Routing Techniques
The arrangement of components strategically plays a role, in the efficiency of intricate PCB designs.
Strategic Component Placement for Performance
Strategically positioning components focuses on elements while considering both usability and ease of manufacturing.
Prioritizing Critical Components
When designing the board layout it's important to prioritize placing components first as they have specific requirements for their proximity, to other parts or board edges based on performance needs or thermal considerations.
Balancing Functionality and Manufacturability
Ensuring both functionality and manufacturability requires taking into account assembly limitations like component accessibility during soldering processes while also maintaining electrical performance by strategically positioning them about other components, on the board layout blueprint.
Advanced Routing Techniques for Complex Designs
The latest PCB designs face challenges, than ever before with the need to navigate intricate layouts and dense component configurations within restricted spaces.
Via Usage and Optimization
When optimizing connections factors such, as choosing the size for vias based on their ability to carry current are taken into account while also aiming to reduce unwanted inductance effects caused by unnecessary usage on multi-layer circuit boards whenever feasible.
Layer Management Strategies
Strategies, for organizing layers require planning of layer configurations tailored to specific uses taking into account both RF/microwave factors and the need to separate digital and analog components. The goal is to enhance system performance by implementing multilayer designs effectively.
Design Verification and Testing Protocols
Conducting Design Rule Checks (DRC)
Checking the design rules (known as DRCs) is crucial to making sure that a PCB layout meets the design limits and can be manufactured as intended. This process helps spot problems at an early stage, in the design process and lowers the chance of expensive mistakes during production.
Common DRC Errors and Solutions
Common DRC errors include violations such as trace width constraints, spacing between traces, and component clearance issues. Solutions involve adjusting trace widths to meet minimum requirements, ensuring adequate spacing between conductive elements, and repositioning components to avoid interference. Implementing automated DRC tools can streamline this process by quickly identifying violations and suggesting corrective actions.
Simulation and Prototyping for Validation
Testing and creating models are crucial to confirm the effectiveness and quality of PCB designs, for large-scaleable manufacturing.
Types of Simulations Used in PCB Design
Different types of simulations are involved in PCB design such as analyzing signal integrity and power integrity along with evaluating characteristics and conducting electromagnetic compatibility (EMC) simulations. Signal integrity analysis examines the propagation on the board whereas power integrity analysis ensures stable power supply . Thermal analysis predicts heat distribution, on the PCB helping to devise thermal management strategies. The EMC simulations investigate electromagnetic interference concerns.
Benefits of Prototyping in Design Verification
Prototyping allows designers to create physical models of their PCBs for testing under real-world conditions. This hands-on approach enables the identification of unforeseen issues that may not be apparent during simulation. Prototyping provides opportunities for iterative improvements, ensuring that the final product meets design specifications and performs reliably in its intended application.
Innovations in PCB Layout Tools and Technologies
Emerging Software Tools for Enhanced Productivity
The latest enhancements, in PCB design, have boosted efficiency with their tools making the design process smoother and more efficient.
Features of Modern PCB Design Software
Today PCB design software comes equipped with features like tools for collaboration that enable designers to work together effectively from different locations in real time.. Advanced algorithms for routing optimize trace paths with minimal manual input required... Integrated simulation capabilities make it possible to conduct testing simultaneously during the design process. Extensive component libraries are also available to provide access to a diverse range of parts essential, for different applications.
Trends in Automated PCB Layout Design
The use of automation is revolutionizing tCB design procedures by boosting productivity and precision with the help of smart algorithms.
- Art
- Causes
- Crafts
- Dance
- Drinks
- Film
- Fitness
- Food
- Oyunlar
- Gardening
- Health
- Home
- Literature
- Music
- Networking
- Other
- Party
- Religion
- Shopping
- Sports
- Theater
- Wellness