PP Plastic vs PVC: Which Material is More Durable and Cost-Effective?
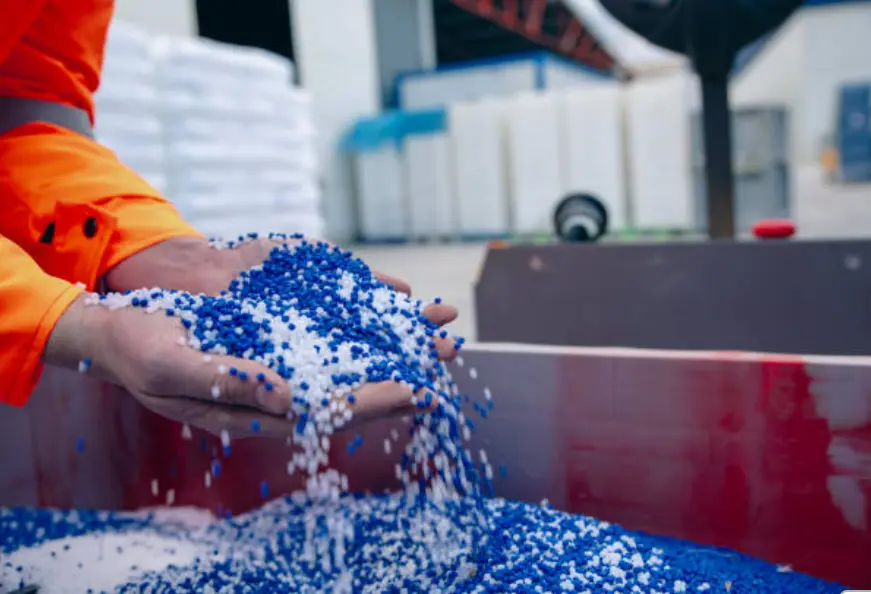
Understanding the Basics of PP Plastic and PVC
Composition and Characteristics of PP Plastic
PP plastic or polypropylene is a polymer created by combining propylene monomers through a process called polymerization process It is recognized for its properties and high melting point which makes it resistant to chemicals and suitable for environments where contact with substancess important Its crystalline structure provides a good mix of strength and flexibility Its lightweight due to its low density making it valuable, in decreasing product weight while ensuring durability.
PP plastic is great for tasks involving water due to its resistance to moisture and wear. Its insulating properties add safety and reliability to applications easily enhanced with additives for UV resistance or flame retardancy, in different industries.
Composition and Characteristics of PVC
PVC or polyvinyl chloride is a thermoplastic polymer that is produced by polymerizing vinyl chloride monomers together. Known for its nature and long lasting qualities PVC is often used in building materials such as pipes and fittings. Unlike PP plastic PVC can be found in both flexible forms thanks, to the inclusion of plasticizers that modify its properties.
In situations where fire safety is paramount PVCs innate ability to resist flames makes it highly appealing.Leveraging its electrical insulation properties PVC is well suited for applications in wires and conduits.While PVC excels in chemical durability it may not possess the encompassness of PP plastic.Its versatility enables it to be molded into shapes and structures for a wide range of purposes. From medical instruments, to everyday consumer goods.
Comparing Durability: PP Plastic vs PVC
Resistance to Environmental Factors
In assessing the durability of materials for uses it is important to consider how they withstand environmental factors such as temperature fluctuations and exposure to UV rays or chemicals. PP plastic shows resistance to numerous acids and bases maintaining its structural integrity even in harsh chemical conditions. Its performance in high temperature situations outperforms that of PVC due, to its melting point.
In weather conditions and when supplemented with substances such as UV inhibitors to shield against the harmful impact of sunlight over time PVC demonstrates strong durability.In the absence of these additives PVCs resistance, to weather elements may weaken and result in material degradation especially when exposed to prolonged sunlight.Compared to PP plastic PVC may become brittle in climates but remains stable in moderate temperature conditions.
Longevity in Various Applications
The durability of substances such as PP plastic and PVC is typically determined by how they're used in various contexts. In piping systems that experience fluid flow or fluctuations in pressure levels both materials function effectively. However PP plastic stands out due to its resistance, to fatigue which enhances its long term dependability especially in dynamic environments.
When choosing materials such as PP plastic and PVC for projects like siding or decking the choice often hinges upon their exposure to elements.The addition of additives can extend the lifespan of both materials.However due to its durability and toughness PP plastic typically surpasses PVC in terms of longevity and performance without experiencing deterioration, over time.
Cost-Effectiveness Analysis
Initial Costs and Installation
When choosing between the two materials at glance costs should be considered including not just the price per unit but also the installation expenses associated with their practical use in real world applications often PP plastic seems to be a more cost effective option initially because of its lower costs, for raw materials and simpler manufacturing processes compared to PVC.
The installation expenses can vary based on the complexity of the application in terms PP plastic is lighter and tends to have more affordable transportation costs and involves less laborious handling during installation when compared to heavier materials, like rigid PVC.
Maintenance and Lifecycle Costs
In examining what is necessary to ensure operation we discover that certain differences can significantly impact the overall cost in the long term. For example the ability of PP plastic to resist chemical damage results in specific maintenance needs over time in environments such, as factories or wastewater treatment facilities where harsh chemicals are prevalent.
Sometimes in PVC installations you may need to do checks or implement measures to avoid UV induced degradation unless the material was adequately stabilized during production. These additional maintenance tasks over time could increase costs despite the expenses being lower, than certain top notch PP plastics.
Understanding these variations can help in making informed decisions that suit the durability requirements and budget constraints of various industries that make use of these versatile polymers.
Applications and Suitability of PP Plastic and PVC
Common Uses of PP Plastic
PP plastic is commonly employed in industries due to its adaptable characteristics and uses that span from the automotive sector to packaging applications. In the field of industry specifically it is used for producing components such, as bumpers and dashboards owing to its quality and resilience to impact. In the realm of packaging PP plastic is favored for crafting containers and bottles because of its resistance to moisture and ability to uphold product quality.
Advantages in Specific Industries
PP plastic is greatly appreciated in industries for its ability to resist chemicals and withstand sterilization methods which makes it a popular choice for syringes and medical trays along with pill bottles usage.. Its low density and robustness are advantageous in the textile field where it is used for making fibers for products like ropes,carpets and upholstery items.. Moreover the electrical insulation properties of PP plastic make it a favored option, in the electronics industry where safety is crucially important.
Limitations in Certain Applications
PP plastic has its advantages in uses but struggles with high temperatures because its not as heat resistant as some engineering plastics are known to be.There is a risk of UV degradation affecting its durability if stabilizers aren't used unless additional treatments are applied.The bonding capabilities of PP plastic are limited which might make it less suitable, for applications requiring properties.
Common Uses of PVC
PVCs versatility allows it to be utilized across a range of industries and sectors for purposes. For example in the construction field rigid PVC is frequently employed in crafting pipes and window frames due to its durability and resistance to weather conditions. On the hand flexible PVC finds common use in flooring and cables thanks, to its pliability.
Advantages in Specific Industries
The construction industry values PVC for its ability to resist fire and its durability in developing materials that adhere to safety regulations. In the medical field PVC is used in blood bags and tubing because of its compatibility, with living tissue. The electrical sector relies on PVC for its insulation properties that provide wiring solutions.
Limitations in Certain Applications
If PVC isn't treated with plasticizers or other additives to enhance its durability under temperatures it may turn brittle.Its improper disposal or incineration can lead to the release of substances into the environment.Concerns about chlorine levels may also restrict its use, in conscious projects.
Environmental Impact Considerations
Recycling and Waste Management for PP Plastic
PP plastic is commonly viewed as a choice due, to its high recyclability and ability to retain quality through multiple recycling cycles into new products.. The recycling rate varies based on the efficiency of recycling facilities Its important to properly sort and clean the plastic to ensure successful recycling processes.
Recycling and Waste Management for PVC
Recycling PVC can be challenging due to the additives it contains that complicate processing tasks.It is essential to have facilities for handling PVC waste effectively and avoiding the release of harmful substances.Technological advancements are now improving recycling methods, for items made of PVC.
Making an Informed Choice: Factors to Consider
Application-Specific Requirements
When choosing between PP plastic and PVC it's crucial to consider the requirements of the intended use case. Factors such as the conditions it will encounter (temperature variations and exposure to chemicals) the level of mechanical strain it will endure (ability to resist impacts and flexibility needs) and compliance, with regulations (meeting fire safety standards and compatibility with living organisms) all contribute to determining the optimal material choice.
Budget Constraints and Long-Term Investment
When deciding which materials to use for a project or product design it's crucial to consider constraints in mind.Experts frequently weigh the cost implications of utilizing PP plastic due, to its raw materials and simpler processing techniques.However when looking at the picture for the long term future planning special attention needs to be given to maintenance needs that can differ basedon the effects of various material choices.
By understanding these components individuals can make informed choices to optimize effectiveness while handling expenses efficiently in scenarios that use either PP plastic or PVC materials effectively in their respective areas of application.
- Art
- Causes
- Crafts
- Dance
- Drinks
- Film
- Fitness
- Food
- Games
- Gardening
- Health
- Home
- Literature
- Music
- Networking
- Other
- Party
- Religion
- Shopping
- Sports
- Theater
- Wellness