Viscose Staple Fibre (VSF) Manufacturing Plant Project Report: Comprehensive Guide to Setup and Production
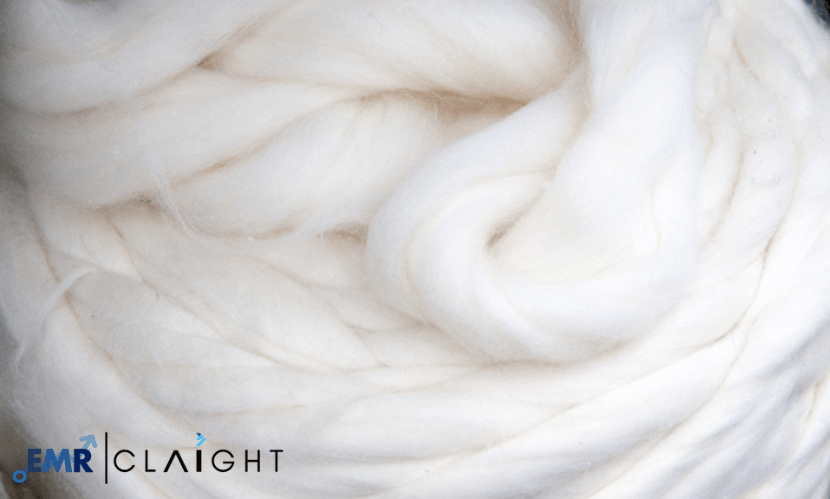
Viscose staple fibre (VSF) is a versatile and eco-friendly textile material derived from natural cellulose, making it a popular choice in the apparel, home furnishing, and hygiene industries. Known for its softness, breathability, and ability to blend with other fibres, VSF has become a key component in producing sustainable fabrics. Establishing a VSF manufacturing plant requires an understanding of its production processes, raw materials, and market opportunities to meet the growing global demand for sustainable and high-quality fibres.
Understanding Viscose Staple Fibre Production
VSF is produced through a chemical process that converts natural cellulose into fine fibres suitable for spinning and weaving. The production involves several intricate stages to ensure the quality and sustainability of the end product.
-
Raw Material Selection
The primary raw material for VSF production is wood pulp, which is sourced from sustainably managed forests. High-purity pulp ensures better fibre quality and minimises environmental impact. -
Cellulose Processing
The wood pulp is treated with chemicals to produce viscose, a liquid solution of cellulose. This step involves precise control of conditions to ensure consistent quality. -
Fibre Formation
The viscose solution is extruded through spinnerets into a coagulating bath, where the liquid is solidified into fine fibres. The fibres are then stretched to enhance their strength and elasticity. -
Cutting and Drying
The fibres are cut into staple lengths, making them suitable for blending with other natural or synthetic fibres. The cut fibres are then dried to remove moisture and prepare them for further processing. -
Finishing
The dried fibres undergo finishing treatments to improve their texture, colour absorption, and performance characteristics. These treatments ensure the fibres meet the specific requirements of various applications. -
Packaging and Storage
The finished VSF is packaged in bales or bundles for easy handling and transportation. Proper labelling and packaging ensure the product’s quality during storage and shipment.
Get a Free Sample Report with Table of Contents@ https://www.expertmarketresearch.com/prefeasibility-reports/viscose-staple-fibre-manufacturing-plant-project-report/requestsample
Key Requirements for Setting Up a VSF Manufacturing Plant
-
Location and Infrastructure
The plant should be situated in a region with access to raw materials, utilities, and transportation networks. Adequate infrastructure is needed for production, storage, and administrative operations. -
Raw Material Procurement
Sourcing high-quality wood pulp from sustainable suppliers is crucial. Establishing reliable supply chains ensures consistent production and supports environmental goals. -
Machinery and Equipment
Essential equipment includes pulping machines, chemical treatment tanks, spinnerets, and drying units. Investing in advanced machinery enhances efficiency and reduces environmental impact. -
Workforce and Training
Skilled personnel are needed to operate machinery, manage production processes, and ensure quality control. Regular training ensures adherence to industry standards and sustainability practices. -
Regulatory Compliance
Adhering to environmental regulations and obtaining certifications such as FSC (Forest Stewardship Council) is critical for legal operations and market acceptance.
Applications of Viscose Staple Fibre
-
Apparel Industry
VSF is widely used in the production of soft, breathable fabrics for clothing, including dresses, shirts, and activewear. Its ability to blend with cotton, polyester, and other fibres enhances fabric versatility. -
Home Textiles
The fibre is used in home furnishings like curtains, bed linens, and upholstery due to its smooth texture and excellent drape. -
Hygiene Products
VSF is a key component in disposable hygiene products like baby wipes, sanitary napkins, and medical textiles due to its absorbency and softness. -
Industrial Applications
VSF is utilised in the production of filters, non-woven fabrics, and specialty papers, showcasing its adaptability across various industries.
Benefits of Establishing a VSF Manufacturing Plant
-
Rising Demand for Sustainable Textiles
The growing consumer preference for eco-friendly products drives the demand for VSF, creating a lucrative market opportunity. -
Versatile Applications
VSF’s wide range of uses in apparel, home furnishings, and hygiene products ensures a broad and stable consumer base. -
Blending Potential
The fibre’s compatibility with other materials allows manufacturers to create innovative fabric blends, catering to diverse market needs. -
Sustainability Advantage
Using renewable resources and adhering to sustainable practices enhances brand reputation and market appeal.
Challenges in Manufacturing
-
Raw Material Availability
Ensuring a consistent supply of high-quality wood pulp can be challenging, particularly during supply chain disruptions. -
Energy and Resource Intensity
The production process requires significant energy and water inputs. Adopting energy-efficient technologies is crucial to minimise costs and environmental impact. -
Regulatory Hurdles
Compliance with environmental and labour regulations requires careful planning and investment in sustainable practices. -
Competition
The textile fibre market is competitive, requiring innovation and effective marketing strategies to differentiate products.
Future Trends in Viscose Staple Fibre Manufacturing
The VSF industry is evolving with advancements in production technology and increasing emphasis on sustainability. Key trends include the adoption of closed-loop production systems to recycle chemicals and water, reducing environmental impact. Innovations in fibre modification, such as antimicrobial treatments and enhanced durability, are expanding the scope of applications. The growing focus on circular fashion and textile recycling presents opportunities for integrating VSF into sustainable supply chains. Additionally, the rise of eco-conscious consumers is expected to drive demand for certified and responsibly sourced fibres.
- Art
- Causes
- Crafts
- Dance
- Drinks
- Film
- Fitness
- Food
- Games
- Gardening
- Health
- Home
- Literature
- Music
- Networking
- Other
- Party
- Religion
- Shopping
- Sports
- Theater
- Wellness