Glass Fiber Reinforced Concrete Panel Manufacturing Plant Project Report 2025: Comprehensive Guide
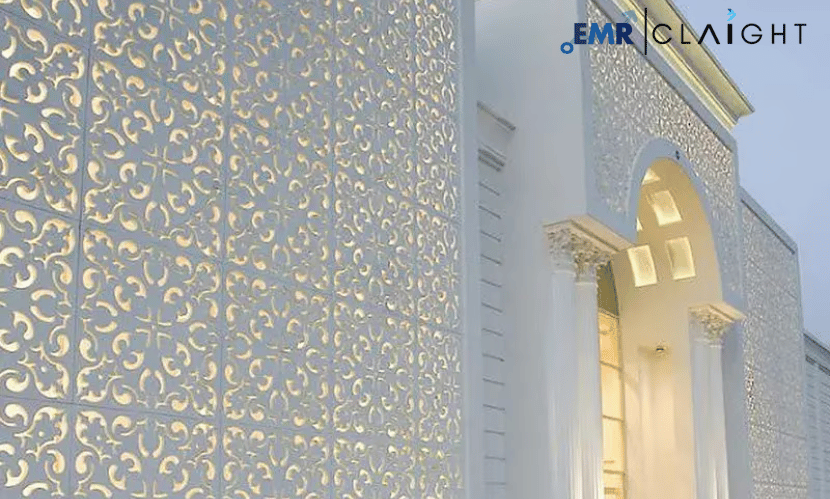
Glass fiber reinforced concrete (GFRC) panels are gaining prominence in the construction industry for their durability, lightweight nature, and versatility. These panels combine the strength of cement and the flexibility of glass fibers, making them an excellent choice for modern architectural designs. Setting up a manufacturing plant for GFRC panels in 2025 requires careful planning and understanding of market trends, raw materials, and production processes. This article provides insights into the critical aspects of establishing a GFRC panel manufacturing plant, helping entrepreneurs and stakeholders make informed decisions.
Market Overview
The demand for GFRC panels is driven by the rising need for sustainable and innovative construction materials. Architects and builders are increasingly opting for GFRC due to its aesthetic appeal and strength. With urbanisation and infrastructural development surging globally, the market for these panels is projected to witness significant growth. Key sectors using GFRC panels include commercial buildings, residential complexes, and public infrastructure projects.
Get a Free Sample Report with Table of Contents@ https://www.expertmarketresearch.com/prefeasibility-reports/glass-fiber-reinforced-concrete-panel-manufacturing-plant-project-report/requestsample
Key Raw Materials
- Cement: Acts as the primary binder, offering compressive strength and durability.
- Sand: Provides bulk and improves the material's workability.
- Glass Fibers: Reinforce the concrete, enhancing tensile strength and resistance to cracking.
- Water: Ensures a uniform mix and proper hydration of cement.
- Additives: Improve performance characteristics like setting time, flexibility, and weather resistance.
Manufacturing Process
The manufacturing process of GFRC panels involves the following steps:
- Material Preparation: Raw materials like cement, sand, and additives are weighed and mixed to form a homogenous mixture.
- Fiber Integration: Glass fibers are added to the mix, ensuring even distribution to achieve the desired strength.
- Moulding: The mixture is poured into moulds of various shapes and sizes, depending on the panel’s intended application.
- Compaction and Curing: Moulded panels are compacted and left to cure, ensuring the material achieves its maximum strength and durability.
- Finishing: Once cured, panels are polished, cut, and prepared for delivery.
Plant Setup Essentials
- Location: Choose a site with proximity to raw material suppliers and key markets to reduce logistics costs.
- Machinery: Invest in advanced mixing, moulding, and curing equipment to ensure quality and efficiency.
- Workforce: Employ skilled technicians and labourers familiar with GFRC production techniques.
- Utilities: Ensure uninterrupted water and power supply, which are critical for production.
- Waste Management: Implement sustainable practices for managing production waste, aligning with environmental regulations.
Applications of GFRC Panels
- Architectural Facades: Ideal for creating intricate designs and cladding for modern buildings.
- Decorative Elements: Used in crafting columns, cornices, and ornamental pieces.
- Wall Panels: Lightweight and strong, suitable for both interior and exterior walls.
- Urban Infrastructure: Applied in the construction of benches, street signs, and other public utilities.
Challenges in Manufacturing
- Material Quality: Ensuring consistent quality of raw materials can be challenging.
- Cost Management: Balancing production costs while maintaining competitive pricing requires careful planning.
- Skilled Labour: The availability of trained personnel is critical for efficient operations.
- Market Competition: Staying ahead of competitors demands continuous innovation and adherence to quality standards.
Future Opportunities
The global focus on green construction and sustainable materials presents vast opportunities for GFRC panel manufacturers. By incorporating eco-friendly practices and exploring innovations like lightweight panels or modular designs, manufacturers can cater to evolving market demands. Additionally, advancements in automation and digitalisation in manufacturing processes can significantly boost efficiency and output.
- Art
- Causes
- Crafts
- Dance
- Drinks
- Film
- Fitness
- Food
- Games
- Gardening
- Health
- Home
- Literature
- Music
- Networking
- Other
- Party
- Religion
- Shopping
- Sports
- Theater
- Wellness