Exploring the Impact of Speed on Carbide Rotary Burs' Efficiency in Cutting Applications
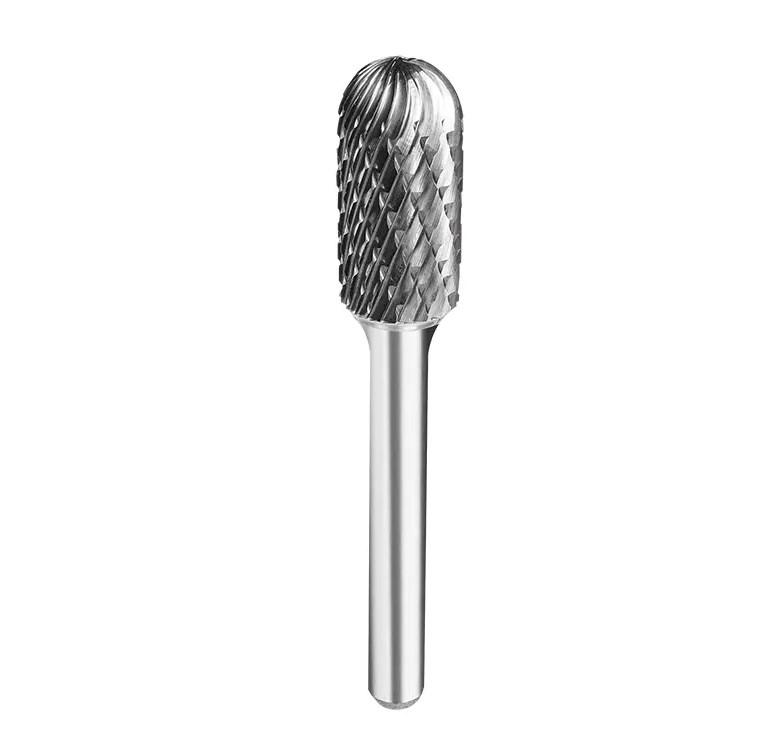
Carbide Rotary Burs are precision tools widely used in various industries for cutting and shaping materials. The performance of these burs is significantly influenced by their rotational speed, a factor that directly impacts the cutting efficiency and the quality of the workpiece. Understanding the relationship between the speed of Carbide Rotary Burs and their cutting effects is essential for optimizing the performance of these tools in different applications.
The rotational speed of the Carbide Rotary Burs is a critical parameter that determines the rate at which material is removed during the cutting process. When the bur rotates at a higher speed, it can cut through materials more quickly, which can increase productivity. However, this increased speed also generates more heat, which can lead to several issues. Excessive heat can cause the material to expand, leading to inaccuracies in the final product. Moreover, high temperatures can also cause the Carbide Rotary Burs to wear out more quickly, reducing their lifespan and increasing the need for replacements.
On the other hand, using Carbide Rotary Burs at a lower rotational speed can reduce the heat generated during the cutting process, thereby minimizing the risk of material deformation. This is particularly important when working with materials that are sensitive to heat, such as certain types of plastics or heat-treated metals. However, lower speeds also mean that the cutting process will take longer, which can decrease productivity and increase the overall time required for a project.
The choice of the appropriate rotational speed for Carbide Rotary Burs is also dependent on the type of material being cut. Harder materials, such as石材 or ceramics, may require a slower speed to ensure a clean and precise cut, while softer materials like wood or some plastics can be cut at higher speeds without the risk of overheating or material degradation.
Another factor to consider is the size and shape of the Carbide Rotary Burs. Larger burs may require a slower speed to prevent breakage, while smaller burs can often handle higher speeds. The shape of the bur also plays a role in determining the optimal speed; for example, a bur with a sharp, pointed tip may be more prone to breaking if used at high speeds.
In addition to the material and the characteristics of the bur itself, the operator's skill level and the specific requirements of the project also influence the selection of the rotational speed. Experienced operators may be able to use higher speeds with greater precision, while beginners might benefit from starting with slower speeds to gain a better understanding of the tool's behavior.
In conclusion, the rotational speed of Carbide Rotary Burs has a significant impact on the cutting effects. Balancing the need for speed with the requirements for precision and material integrity is crucial for achieving the best results. By carefully considering the material being cut, the characteristics of the bur, and the operator's skill level, it is possible to optimize the rotational speed of Carbide Rotary Burs to achieve the desired cutting performance. This optimization not only leads to higher-quality workpieces but also extends the life of the burs and improves overall productivity in various cutting applications.
- Art
- Causes
- Crafts
- Dance
- Drinks
- Film
- Fitness
- Food
- Games
- Gardening
- Health
- Home
- Literature
- Music
- Networking
- Other
- Party
- Religion
- Shopping
- Sports
- Theater
- Wellness