Leveraging Technology for Efficiency: The Path to Automation in Single Wall Paper Cup Factory
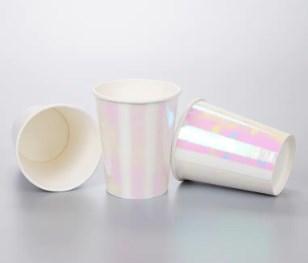
The Single Wall Paper Cup Factory, a cornerstone in the disposable packaging industry, is undergoing a transformative shift towards automation. This transition is not merely a trend but a strategic move to enhance productivity, reduce human error, and meet the growing demands of the market. The implementation of automation in a Single Wall Paper Cup Factory involves the integration of advanced technologies and systems that work in tandem to streamline the production process from start to finish.
The journey towards automation in a single-wall paper Cup Factory begins with the design and engineering of the production line. State-of-the-art machinery that can handle high-speed manufacturing with precision is crucial. These machines are capable of forming, cutting, and shaping the paper into cups with minimal waste and maximum efficiency. The use of robotics in the Single Wall Paper Cup Factory allows for the automation of tasks such as material handling, which was traditionally a manual process. Robots can load and unload materials with speed and accuracy, reducing downtime and the risk of injury to workers.
The next phase of automation in a Single Wall Paper Cup Factory involves the integration of intelligent systems that can monitor and control the production process. These systems, often referred to as the Industrial Internet of Things (IIoT), collect data from various points in the production line, allowing for real-time adjustments and optimizations. By analyzing this data, the Single Wall Paper Cup Factory can identify bottlenecks, predict machine failures, and adjust production schedules accordingly. This level of oversight not only improves efficiency but also ensures the consistency and quality of the final product.
Another critical aspect of automation in a Single Wall Paper Cup Factory is the implementation of quality control systems. Automated inspection systems can check each cup for defects, such as uneven walls or misaligned seams, at a rate far surpassing human capabilities. These systems can also be programmed to learn from the data they collect, improving their accuracy and efficiency over time. By automating quality control, the Single Wall Paper Cup Factory can maintain high standards of product quality while reducing the need for manual inspection.
The automation of a Single Wall Paper Cup Factory also extends to the packaging and shipping processes. Automated packaging lines can wrap, box, and palletize the finished cups with precision, reducing the risk of damage during transportation. Additionally, automated warehousing systems can optimize storage and retrieval, ensuring that the right products are available when needed. This not only speeds up the shipping process but also reduces the likelihood of errors in order fulfillment.
The transition to automation in a Single Wall Paper Cup Factory is not without its challenges. The initial investment in new machinery and technology can be substantial, and there is a learning curve for both the machines and the workforce. However, the long-term benefits of increased efficiency, reduced waste, and improved product quality far outweigh these initial costs. As the technology continues to evolve, the Single Wall Paper Cup Factory that embraces automation will be well-positioned to meet the challenges of the future.
In conclusion, the automation of a Single Wall Paper Cup Factory is a multifaceted endeavor that encompasses the integration of advanced machinery, intelligent systems, and quality control measures. By embracing this transformation, Single Wall Paper Cup Factories can achieve a new level of efficiency and competitiveness in the global market. The path to automation is not without its obstacles, but for those who navigate it successfully, the rewards are significant and sustainable.
- Art
- Causes
- Crafts
- Dance
- Drinks
- Film
- Fitness
- Food
- Games
- Gardening
- Health
- Home
- Literature
- Music
- Networking
- Other
- Party
- Religion
- Shopping
- Sports
- Theater
- Wellness