Distributed Control Systems Market: The Growing Demand for Energy-Efficient Solutions
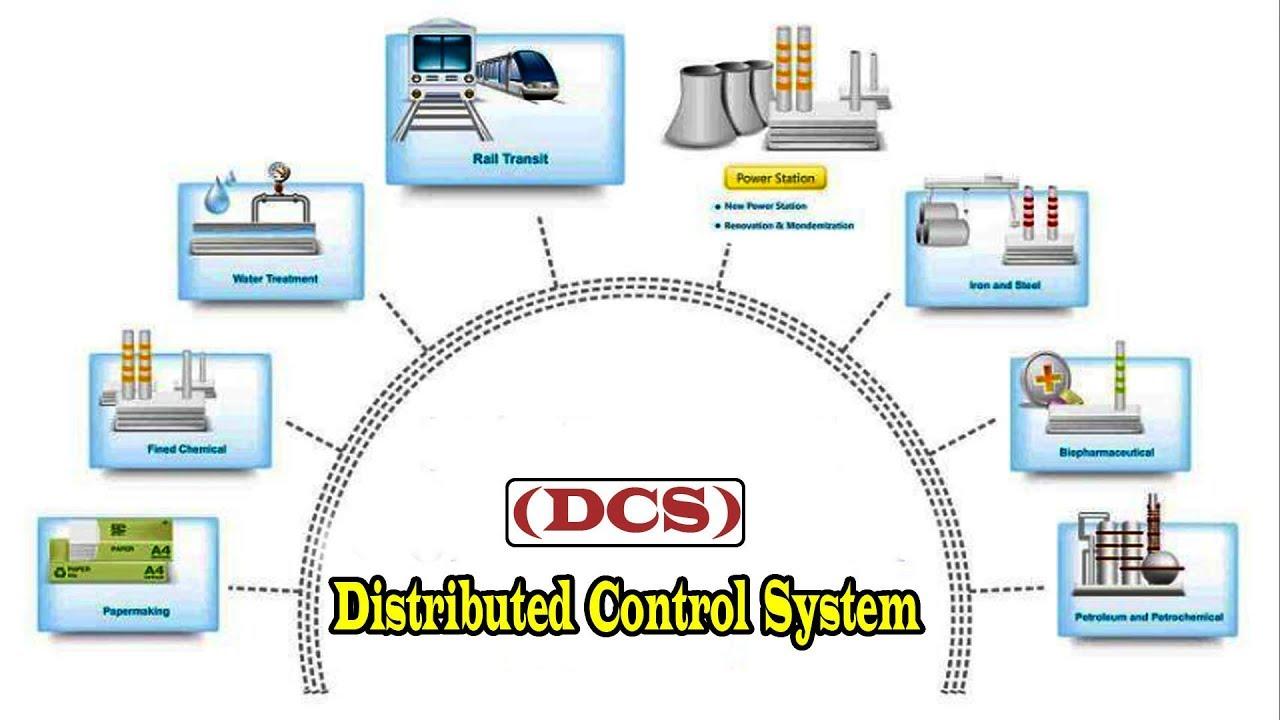
The Distributed Control Systems (DCS) market has experienced substantial growth in recent years, driven by the increasing demand for automation, safety, and operational efficiency across various industrial sectors. One of the key trends fueling the DCS market’s expansion is the growing emphasis on energy efficiency. As industries face rising energy costs, environmental regulations, and the need to reduce their carbon footprint, the demand for energy efficient control systems has become a major driver of innovation in the DCS market. By optimizing energy consumption, improving process control, and enhancing system performance, DCS solutions play a critical role in helping industries meet these challenges.
Market Dynamics
The DCS market is characterized by several key dynamics that influence its growth and development. These include the rising adoption of automation technologies, increasing environmental awareness, advancements in digital technologies, and the need for better integration of renewable energy sources into the grid.
-
Increasing Industrial Automation: The global push for Industry 4.0 and the digital transformation of industries has driven a significant rise in the adoption of automation technologies. DCS provides a flexible, scalable solution for controlling complex industrial processes, making it an essential tool for industries like oil and gas, chemicals, power generation, and manufacturing. Automation systems that integrate DCS help organizations improve their productivity, reduce downtime, and optimize the use of resources, including energy.
-
Environmental Regulations and Sustainability Goals: Governments and regulatory bodies worldwide are setting stricter environmental regulations to reduce industrial carbon emissions and improve energy efficiency. In this context, DCS plays an important role by automating processes that optimize energy consumption and minimize waste. Energy-efficient DCS solutions can help companies reduce their operational costs while meeting stringent environmental standards. As industries work toward sustainability goals, energy efficient DCS systems become an integral part of their operations.
-
Integration of Renewable Energy: The growing shift toward renewable energy sources such as wind, solar, and biomass is another driver for the DCS market. Renewable energy systems require advanced control systems to manage the fluctuating nature of power generation and ensure grid stability. DCS solutions are essential for integrating renewable energy into the grid by providing real-time control, monitoring, and optimization. By managing both conventional and renewable energy sources, DCS can help ensure a more efficient and sustainable energy mix.
-
Cost Reduction Pressures: Rising energy costs are pushing industries to adopt energy-efficient solutions that reduce operational expenses. For many industries, energy consumption represents a significant portion of overall operating costs. DCS systems help optimize energy use by controlling and monitoring various processes such as heating, cooling, and manufacturing, reducing waste, and improving energy efficiency. The ability to reduce energy consumption directly correlates with lower operational costs, which makes DCS an attractive solution for businesses aiming to improve their bottom line.
-
Technological Advancements and Integration with IoT: The development of smart grids, Internet of Things (IoT), and artificial intelligence (AI) is enhancing the capabilities of DCS systems. By integrating DCS with IoT devices, sensors, and cloud-based data analytics, companies can gain deeper insights into their operations and identify areas for energy optimization. Real time data analysis and predictive maintenance powered by AI can help identify inefficiencies in energy use and make adjustments in real time, further boosting the energy efficiency of operations.
The Role of Energy-Efficient DCS Solutions
Energy efficiency has become a focal point in the development of modern DCS systems. By implementing energy efficient DCS solutions, industries can optimize their processes, reduce energy consumption, and meet both cost and environmental goals. Here are some key ways in which DCS contributes to energy efficiency:
-
Process Optimization: DCS systems allow for real-time monitoring and control of industrial processes. By continuously assessing parameters like pressure, temperature, flow rate, and energy use, DCS can adjust processes to operate at optimal efficiency. For instance, in a manufacturing plant, DCS can regulate machinery speeds, energy-intensive processes, and temperature settings to minimize energy consumption without sacrificing output or product quality.
-
Load Shedding and Demand Response: Energy-efficient DCS solutions are increasingly being integrated with demand-response programs, which help industrial facilities reduce their energy consumption during peak hours. DCS can automatically adjust energy use or shut down non-essential processes during high-demand periods, thereby contributing to grid stability and reducing energy costs. This feature is especially relevant in industries that operate in energy-intensive sectors like petrochemicals and heavy manufacturing.
-
Integration of Energy Management Systems (EMS): Energy management systems are often integrated with DCS to enhance energy efficiency. By combining DCS with EMS, companies can track energy consumption across different processes, identify energy losses, and implement strategies for improvement. An EMS can provide detailed energy audits, predictive analytics, and energy-saving suggestions, while DCS can execute control actions based on the recommendations. This integration enables industries to create energy-efficient workflows and meet sustainability targets.
-
Advanced Process Control (APC): Advanced Process Control (APC) techniques, such as model predictive control (MPC), are increasingly being implemented within DCS systems to further optimize energy use. MPC allows DCS to predict the future state of a system and adjust controls to minimize energy waste and improve efficiency. For example, in a power plant, MPC can predict the energy requirements of various components and adjust the output of turbines and generators to match demand, reducing energy loss and enhancing operational performance.
-
Real-time Data Analytics for Energy Efficiency: Real-time data analytics is a critical feature of modern DCS solutions, enabling companies to monitor energy consumption patterns across their operations. DCS systems can collect and analyze vast amounts of data from various sensors and devices to identify inefficiencies, predict equipment failures, and optimize energy usage. By using data-driven insights, companies can make informed decisions about when to adjust processes, replace equipment, or invest in energy-saving technologies.
Industry-Specific Applications of Energy-Efficient DCS
-
Oil and Gas: In the oil and gas industry, DCS solutions are used to control and monitor complex processes such as drilling, refining, and transportation. Energy-efficient DCS helps minimize energy use in these energy-intensive operations by optimizing pump and compressor speeds, regulating heating systems, and reducing energy waste in offshore platforms and refineries.
-
Power Generation: Power generation plants, particularly those transitioning to renewable energy, benefit from energy-efficient DCS systems that help balance supply and demand. DCS solutions manage grid integration, regulate power generation from both conventional and renewable sources, and ensure that energy consumption is optimized to meet demand efficiently.
-
Manufacturing: In manufacturing, energy efficiency is key to reducing production costs. DCS systems optimize various stages of production, from raw material processing to packaging, by minimizing energy use without affecting the quality or throughput of goods. This is particularly important in industries such as cement, steel, and automotive manufacturing.
- Art
- Causes
- Crafts
- Dance
- Drinks
- Film
- Fitness
- Food
- Games
- Gardening
- Health
- Home
- Literature
- Music
- Networking
- Other
- Party
- Religion
- Shopping
- Sports
- Theater
- Wellness