Allen Key Market Dynamics: Understanding Supply Chain Challenges
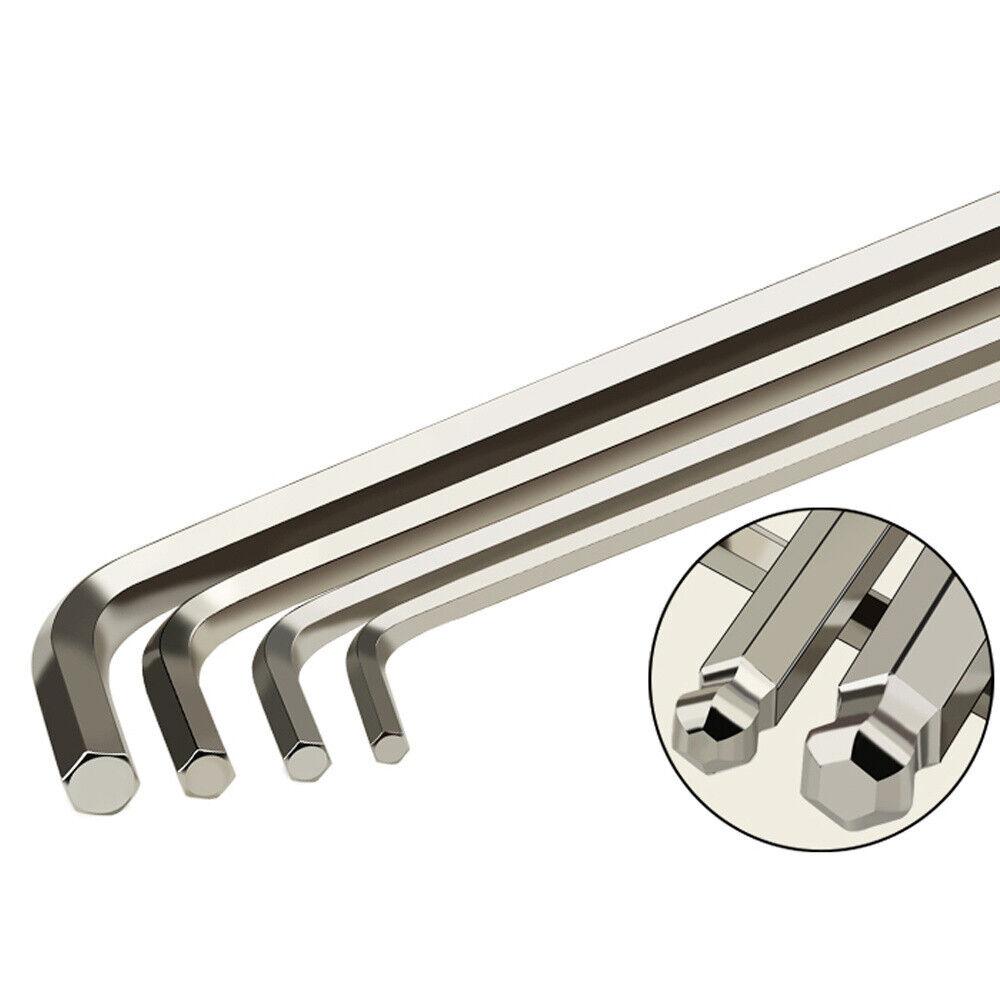
The Allen key market, crucial for a variety of applications from DIY projects to industrial uses, faces a complex landscape shaped by numerous supply chain challenges. Understanding these dynamics is essential for manufacturers, retailers, and consumers to navigate the current environment effectively. This article delves into the key supply chain challenges affecting the Allen key market and their implications for the industry.
Overview of the Allen Key Market
Allen keys, also known as hex keys, are simple yet indispensable tools utilized in various settings, including home assembly, automotive repair, and manufacturing. While demand for these tools remains steady, the market is increasingly influenced by external factors that complicate production and distribution.
Key Supply Chain Challenges
1. Global Disruptions
The COVID-19 pandemic highlighted vulnerabilities within global supply chains, causing widespread disruptions. Factory closures, transportation delays, and labor shortages severely impacted production capabilities and inventory management. These disruptions led to increased lead times and costs, affecting both manufacturers and consumers.
2. Material Shortages
The availability of raw materials, particularly steel and other alloys used in Allen key production, has become increasingly volatile. Demand surges in various sectors, trade restrictions, and geopolitical tensions have contributed to material shortages. This scarcity not only drives up costs but also complicates the manufacturing process, forcing companies to adjust their production schedules and pricing strategies.
3. Transportation Challenges
Transportation issues have emerged as a critical concern, with rising shipping costs and delays in delivery becoming commonplace. Global shipping bottlenecks, port congestion, and fluctuating fuel prices have strained logistics networks, making timely delivery of products more challenging. For manufacturers relying on just-in-time inventory systems, these transportation hurdles can disrupt operations and lead to stockouts.
4. Labor Shortages
Labor shortages in manufacturing hubs have exacerbated supply chain challenges. As companies struggle to attract and retain skilled workers, production capacities may be limited. This issue is particularly acute in industries heavily reliant on manual labor, including tool manufacturing. Without sufficient labor, manufacturers may find it difficult to meet rising demand.
5. Fluctuating Demand
The Allen key market also experiences fluctuations in consumer demand influenced by seasonal trends and economic conditions. For instance, spikes in DIY projects during lockdown periods have led to sudden increases in demand for Allen keys, putting further pressure on supply chains. Manufacturers must remain agile to adjust to these demand shifts while managing their production and inventory levels.
Implications for the Market
1. Increased Costs
Supply chain disruptions typically lead to increased costs, which manufacturers may pass on to consumers. Rising raw material prices, transportation costs, and labor expenses can all contribute to higher retail prices for Allen keys. This situation may affect consumer purchasing decisions, particularly in price-sensitive markets.
2. Product Availability
Challenges in the supply chain can lead to reduced product availability in retail and online marketplaces. Delays in production and distribution may result in stockouts, making it difficult for consumers to find the tools they need. This can lead to frustration and a potential shift in consumer loyalty toward brands that can maintain consistent supply.
3. Emphasis on Resilience
To navigate these challenges, companies are increasingly focused on building resilience within their supply chains. This includes diversifying suppliers, investing in technology for better inventory management, and exploring local sourcing options. By enhancing their supply chain resilience, manufacturers can better withstand disruptions and respond effectively to changes in demand.
Strategies for Overcoming Supply Chain Challenges
1. Diversification of Suppliers
Manufacturers can mitigate risks associated with material shortages and disruptions by diversifying their supplier base. Establishing relationships with multiple suppliers can provide greater flexibility and ensure a more stable flow of materials.
2. Investing in Technology
Adopting advanced supply chain management technologies can improve forecasting, inventory tracking, and logistics planning. Data analytics can help manufacturers anticipate demand fluctuations and optimize production schedules accordingly.
3. Strengthening Partnerships
Building strong relationships with logistics partners and suppliers can enhance communication and collaboration. This teamwork allows companies to respond more effectively to supply chain disruptions and maintain a steady flow of products.
4. Adapting Production Strategies
Manufacturers may need to reevaluate their production strategies to better align with current market conditions. This could involve increasing production capacity during peak demand periods or adjusting product offerings based on material availability.
- Art
- Causes
- Crafts
- Dance
- Drinks
- Film
- Fitness
- Food
- Games
- Gardening
- Health
- Home
- Literature
- Music
- Networking
- Other
- Party
- Religion
- Shopping
- Sports
- Theater
- Wellness