Understanding Aluminum Coil Manufacturing: A Step-by-Step Guide
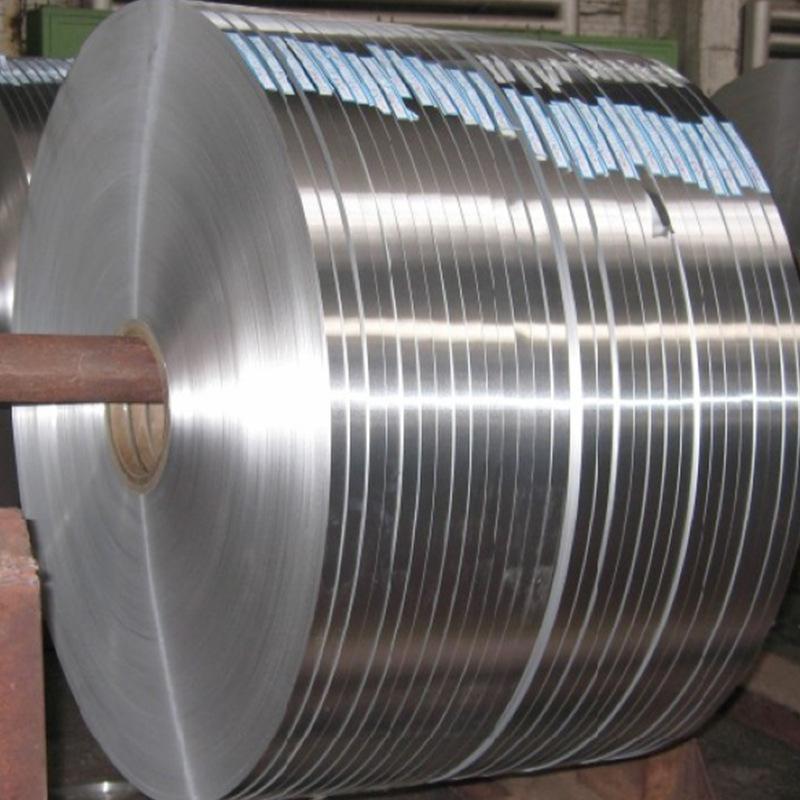
Aluminum coils are an integral part of many industries, from construction to automotive and electronics. The manufacturing process for aluminum coils involves a series of steps that transform raw aluminum into a versatile and durable product. In this blog, we will explore the aluminum coil manufacturing process step by step, highlighting the key techniques and technologies involved.
Step 1: Raw Material Selection
The manufacturing of aluminum coils begins with the selection of raw materials. Primary aluminum is typically sourced from bauxite ore, which is processed through the Bayer process to produce alumina. This alumina is then reduced to aluminum metal using the Hall-Héroult process. In some cases, recycled aluminum can also be used, which is a more sustainable option and significantly reduces the energy required for production.
Step 2: Melting and Casting
Once the raw aluminum is obtained, it undergoes melting and casting. The aluminum is heated in a furnace to its melting point, which is around 660°C (1220°F). After it melts, the liquid aluminum is poured into molds to form large blocks known as ingots. These ingots can weigh up to several tons and serve as the primary feedstock for the next phase of production.
Key Considerations:
Alloying Elements: During the melting process, various alloying elements (like magnesium, silicon, or copper) may be added to achieve desired mechanical properties.
Quality Control: It’s essential to monitor the melting process closely to ensure that no impurities are introduced.
Step 3: Hot Rolling
After casting, the aluminum ingots are cooled and then reheated before undergoing hot rolling. This process involves passing the ingots through a series of rollers that gradually reduce their thickness. Hot rolling typically occurs at temperatures above 400°C (752°F) to maintain the malleability of the aluminum.
Benefits of Hot Rolling:
Thickness Reduction: This step can reduce the thickness of the ingots from several inches to a few millimeters.
Grain Structure Modification: The rolling process also refines the grain structure of the aluminum, improving its strength and flexibility.
Step 4: Cold Rolling
Following hot rolling, the aluminum coils may undergo cold rolling, which further reduces their thickness while improving surface finish and dimensional accuracy. Cold rolling is done at room temperature, allowing for tighter tolerances and enhanced mechanical properties.
Important Factors in Cold Rolling:
Surface Quality: Cold rolled aluminum typically has a smoother surface, making it ideal for applications where aesthetics are important.
Work Hardening: This process increases the hardness of the aluminum, making it suitable for a wider range of applications.
Step 5: Annealing
To relieve the stresses introduced during the rolling processes, aluminum coils undergo annealing. This heat treatment process involves heating the aluminum to a specific temperature and then slowly cooling it. Annealing helps to soften the material, restoring its ductility and making it easier to work with in subsequent processing steps.
Process Control:
Temperature and Time: The annealing process requires precise control of temperature and time to ensure uniformity and prevent defects.
Step 6: Surface Treatment
The surface treatment of aluminum coils is crucial for enhancing their properties, particularly in terms of corrosion resistance and aesthetics. Common surface treatments include:
Anodizing: This electrochemical process forms a protective oxide layer on the aluminum surface, improving its corrosion resistance and wear properties.
Coating: Applying paint or powder coating can enhance appearance and protect against environmental factors.
Step 7: Slitting and Shearing
Once the aluminum coils have been processed and treated, they are slit into narrower widths to meet specific customer requirements. Slitting involves cutting the coils into strips of varying widths, while shearing can cut the coils into specific lengths.
Equipment Used:
Slitter Machines: These machines are designed to cut aluminum coils with precision.
Shear Blades: High-quality blades ensure clean cuts without damaging the material.
Step 8: Quality Assurance and Packaging
Before the finished aluminum coils are shipped to customers, they undergo rigorous quality assurance checks. This includes visual inspections, dimensional checks, and testing for mechanical properties. Any defects identified during this process are addressed to ensure that only high-quality products reach the market.
Packaging:
Proper packaging is essential to protect the aluminum coils during transport. They are typically wrapped in protective materials and securely strapped to pallets to prevent damage.
Conclusion
Understanding the manufacturing process of aluminum coils provides valuable insight into the complexities involved in producing this essential material. From raw material selection to the final quality checks, each step plays a crucial role in determining the properties and performance of aluminum coils. As industries continue to innovate and demand higher quality materials, advancements in aluminum coil manufacturing will remain a focal point in achieving sustainability and efficiency in production. Whether in construction, transportation, or electronics, the significance of aluminum coils cannot be overstated, making this knowledge essential for anyone involved in the aluminum supply chain.
- Art
- Causes
- Crafts
- Dance
- Drinks
- Film
- Fitness
- Food
- Games
- Gardening
- Health
- Home
- Literature
- Music
- Networking
- Other
- Party
- Religion
- Shopping
- Sports
- Theater
- Wellness