Metalworking Fluids Market Segmentation Analysis: Exploring Diverse Types, Applications, and End-User Industries Driving Demand
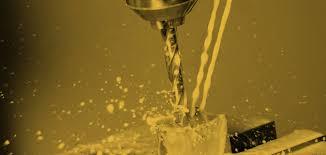
The metalworking fluids market is a critical segment of the manufacturing industry, encompassing various types of fluids that facilitate machining processes. These fluids play essential roles in lubrication, cooling, and protecting both the workpiece and the tools during manufacturing. With the market evolving rapidly, a detailed segmentation analysis reveals the diverse types of metalworking fluids, their applications, and the end-user industries driving demand.
Types of Metalworking Fluids
1. Cutting Fluids
Cutting fluids are among the most commonly used types of metalworking fluids. They are designed to reduce friction and wear during cutting operations, which enhances tool life and improves surface finish. Cutting fluids can be further categorized into:
-
Oil-Based Fluids: These fluids typically consist of mineral oils and are effective in providing lubrication and cooling. They are widely used in various machining processes, such as turning, milling, and drilling.
-
Water-Soluble Fluids: Also known as emulsions, these fluids combine water and oil to provide cooling and lubrication. They are popular due to their cost-effectiveness and ability to dissipate heat efficiently.
-
Synthetic Fluids: Composed of chemical compounds, synthetic fluids offer superior cooling and lubricating properties without the use of oil. They are increasingly favored in precision machining applications where high performance is essential.
2. Forming Fluids
Forming fluids are specialized fluids used in processes like stamping, bending, and forging. Their primary role is to lubricate and cool during the deformation of metal, reducing friction and wear on tools. Key types include:
-
Straight Oils: These are non-emulsifiable fluids that provide excellent lubrication in forming processes.
-
Emulsifiable Fluids: These fluids can be mixed with water to create a milky emulsion, offering both lubrication and cooling properties.
3. Quenching Fluids
Quenching fluids are used to cool hot metal parts during heat treatment processes, such as hardening. These fluids can significantly impact the final properties of the metal. Common types include:
-
Water-Based Solutions: These are often used for their high cooling efficiency but can lead to warping if not managed correctly.
-
Oil-Based Quenchants: These fluids provide slower cooling rates, allowing for controlled hardening and reducing the risk of cracking.
4. Rust Preventive Fluids
Rust preventive fluids are essential for protecting metal parts from corrosion during storage and transportation. They form a protective film over the surface, inhibiting moisture and air from causing rust. These fluids can be classified into:
-
Temporary Protective Coatings: Used for short-term protection, these coatings are often easy to remove before further processing.
-
Permanent Protective Oils: These fluids offer long-term protection and are used for parts that will not be processed further.
Applications of Metalworking Fluids
1. Machining Operations
The machining sector represents the largest application area for metalworking fluids. Cutting, grinding, and milling operations require effective lubrication and cooling to maintain efficiency and product quality. The choice of fluid can significantly impact tool life and surface finish.
2. Forming Processes
In addition to machining, metalworking fluids are crucial in forming processes such as stamping, bending, and extrusion. The right fluid can enhance the quality of the formed part, reduce tool wear, and improve process efficiency.
3. Heat Treatment
Heat treatment processes, including quenching and tempering, heavily rely on metalworking fluids to achieve desired mechanical properties. The cooling rates and fluid characteristics play a vital role in determining the hardness and strength of the finished product.
4. Surface Treatment
Surface treatment processes, including polishing and coating, often use metalworking fluids to ensure smooth finishes and enhance adhesion of coatings. The choice of fluid can affect the final surface quality and performance.
End-User Industries Driving Demand
1. Automotive
The automotive industry is a significant consumer of metalworking fluids, driven by the need for efficient machining and manufacturing of components. With the rising demand for lightweight and high-performance vehicles, there is a growing emphasis on advanced machining processes that require specialized fluids.
2. Aerospace
The aerospace sector demands high precision and quality in manufacturing, leading to the adoption of advanced metalworking fluids. The need for lightweight materials and complex geometries in aerospace components necessitates the use of specialized fluids to enhance performance and reduce wear.
3. General Manufacturing
General manufacturing encompasses a wide range of applications, including machinery, equipment, and tools. The diverse needs of this sector drive demand for various types of metalworking fluids tailored to specific processes.
4. Construction and Heavy Equipment
The construction and heavy equipment industries rely on metalworking fluids for the manufacturing of components such as gears, axles, and frames. The durability and performance of these components are critical, increasing the need for effective lubrication and cooling solutions.
5. Electronics
As technology advances, the electronics industry requires precision machining for components like circuit boards and connectors. The use of specialized metalworking fluids helps achieve the tight tolerances and clean finishes necessary for electronic components.
Conclusion
The metalworking fluids market is characterized by diverse types, applications, and end-user industries, each driving demand in unique ways. Understanding the segmentation of this market is crucial for manufacturers and suppliers looking to develop targeted strategies that address specific needs. As industries evolve and sustainability becomes a priority, the demand for innovative and eco-friendly metalworking fluids is expected to grow. By exploring these diverse segments, stakeholders can better navigate the market landscape and capitalize on emerging opportunities for growth and innovation.
- Art
- Causes
- Crafts
- Dance
- Drinks
- Film
- Fitness
- Food
- Games
- Gardening
- Health
- Home
- Literature
- Music
- Networking
- Other
- Party
- Religion
- Shopping
- Sports
- Theater
- Wellness