Advanced Materials Driving Performance Improvements in Wind Turbine Components
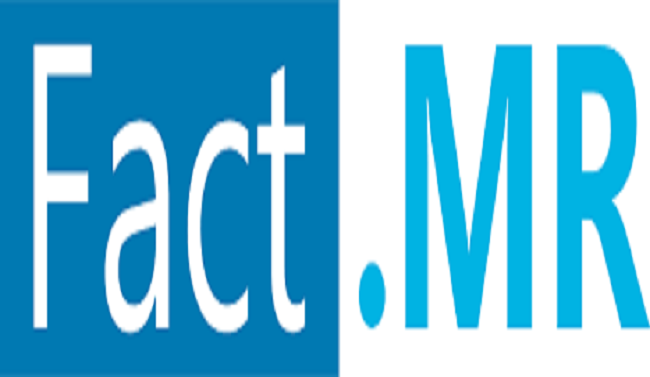
The global wind turbine material market is valued at US$ 7.01 billion in 2024 and is expected to reach US$ 13.8 billion by 2034. The demand for wind turbine materials is anticipated to grow at a compound annual growth rate (CAGR) of 7% from 2024 to 2034.
The wind turbine material market plays a crucial role in the global renewable energy landscape. As the world increasingly turns to wind power to reduce carbon emissions and achieve sustainability goals, the demand for high-performance materials that enhance turbine efficiency has surged. Wind turbines are complex machines composed of various materials, each selected for its ability to withstand environmental stressors such as high winds, saltwater corrosion, and extreme temperatures. The primary materials used in wind turbines include metals, composites, resins, and adhesives. Steel, copper, fiberglass, and carbon fiber are among the most common materials utilized, with each component serving a specific function, whether it be in the tower, blades, or electrical systems. The ongoing advancements in material technology have paved the way for stronger, lighter, and more durable wind turbines, reducing maintenance costs and increasing energy output, making the market for these materials a critical focus for manufacturers and energy companies alike.
Market Insights
The wind turbine material market has evolved significantly over the past decade, driven by the rapid expansion of wind energy projects worldwide. Government policies supporting renewable energy initiatives, coupled with technological innovations, have spurred demand for materials that improve the efficiency and lifespan of turbines. One of the key insights from the market is the increasing preference for composite materials, particularly carbon fiber-reinforced plastics, which offer superior strength-to-weight ratios. This shift is helping manufacturers create lighter and more durable blades, enabling turbines to capture more energy at lower wind speeds. Additionally, the integration of advanced coatings and adhesives to protect turbine components from harsh environmental conditions is on the rise. Another critical insight is the regional dynamics, with countries like China, the U.S., and Germany leading the wind energy industry, driving material demand due to their massive turbine installations. The growing offshore wind projects further add to the complexity of material requirements, emphasizing corrosion resistance and structural durability.
Market Demand
The demand for wind turbine materials is closely tied to the increasing global investment in wind energy as a key component of the renewable energy mix. Several factors are driving this demand. First, the global shift towards renewable energy sources, driven by climate change concerns and energy security, is prompting governments and companies to expand their wind energy capacity. Second, the trend of building larger and more efficient turbines has escalated the need for materials that offer both durability and reduced weight. Lightweight composites, particularly carbon fiber, are in high demand for manufacturing blades, which must be both flexible and strong to operate efficiently in a variety of wind conditions. The need for robust metals for turbine towers and advanced adhesives and resins for secure component bonding also contribute to the growing demand. Furthermore, as offshore wind farms continue to proliferate, the need for materials with high corrosion resistance is increasingly important.
List of Key Companies Profiled in The Report
- Siemens AG
- Teijin Limited
- Toray Industries Inc.
- Reliance Industries Limited
- Lianyungang Zhongfu Lianzhong Composites Group Co. Ltd.
- Molded Fiber Glass Companies
- Gurit Holding AG
- Others
Recent Industry News
In recent industry news, several key players in the wind turbine material market have announced advancements and partnerships aimed at improving material efficiency and sustainability. Notably, companies such as Siemens Gamesa and Vestas have been exploring recyclable blade technologies to address the issue of end-of-life turbine waste. Meanwhile, the expansion of offshore wind farms in Europe and the U.S. has led to new material innovations, particularly in coatings that protect turbines from the corrosive effects of seawater. The market has also seen an increase in mergers and acquisitions, with larger material suppliers acquiring specialized companies to enhance their portfolios and production capabilities in the wind energy sector.
Notable Developments
Several notable developments have emerged in the wind turbine material market. One of the most significant is the growing use of thermoplastic materials for turbine blades. Unlike traditional thermoset composites, thermoplastics offer the advantage of recyclability, aligning with the industry’s growing focus on sustainability. Another development is the integration of digital technologies, such as smart sensors and coatings that monitor material degradation and performance in real-time. This shift towards smart materials is expected to improve the operational efficiency and longevity of wind turbines. Additionally, the continued evolution of lightweight materials is enabling the construction of larger, more efficient turbines, with blades exceeding 100 meters in length now becoming more common.
Competitive Landscape
The competitive landscape of the wind turbine material market is shaped by key players employing strategies such as innovation, diversification, strategic collaborations, sustainability, and cost-efficiency to boost their revenue and strengthen their market position. Ongoing investments in research and development are enabling these companies to create advanced materials and technologies that enhance the efficiency, durability, and sustainability of wind turbine components.
Many leading companies are also expanding their global footprint, aiming to access new customer bases and diversify their revenue streams. For example, in May 2021, Hexcel launched a new line of HexPly products designed for surface finishing applications in the wind energy sector, as well as the automotive and marine industries.
- Art
- Causes
- Crafts
- Dance
- Drinks
- Film
- Fitness
- Food
- Games
- Gardening
- Health
- Home
- Literature
- Music
- Networking
- Other
- Party
- Religion
- Shopping
- Sports
- Theater
- Wellness