The Resilience of Energy Pumps: A Study in Durability and Longevity
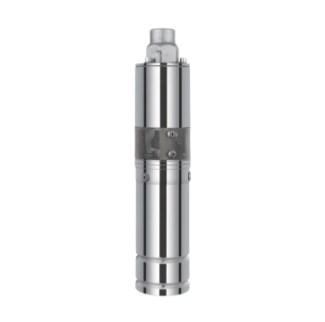
Durability is a cornerstone attribute in the engineering and manufacturing of industrial equipment, and Energy Pump is no exception. These indispensable components of various systems are designed to withstand the rigors of continuous operation, ensuring a reliable and efficient energy transfer process. The durability of Energy Pumps is a testament to the ingenuity of their design, the quality of materials used, and the precision of their manufacturing processes.
The concept of durability in Energy Pumps encompasses several aspects, including resistance to wear and tear, the ability to operate under extreme conditions, and a long service life with minimal maintenance. The materials used in the construction of Energy Pumps are carefully selected to provide the necessary strength and resilience. Metals such as stainless steel, cast iron, and various alloys are common choices due to their robustness and resistance to corrosion, which are critical for the longevity of the pump.
Moreover, the design of Energy Pumps incorporates elements that enhance their durability. For instance, the use of dynamic seals and bearings that are resistant to the specific conditions they will encounter, such as high temperatures, pressures, or corrosive environments, is essential. These components must be able to maintain their integrity and performance over time, which is why they are often made from advanced materials and engineered to minimize friction and wear.
The manufacturing process also plays a crucial role in the durability of Energy Pumps. Precision engineering ensures that each part fits perfectly with the others, reducing the likelihood of mechanical failure. Additionally, rigorous quality control measures are implemented to detect and rectify any defects before the pump is put into service.
One of the most significant factors contributing to the durability of Energy Pumps is their maintenance. Regular inspections, timely replacement of worn parts, and adherence to the manufacturer's guidelines for operation and maintenance can significantly extend the life of an Energy Pump. Proper maintenance not only prevents unexpected breakdowns but also ensures that the pump operates at peak efficiency, reducing energy consumption and environmental impact.
In the context of industrial applications, the durability of Energy Pumps is particularly important. These pumps are often used in demanding environments, such as chemical processing plants, oil refineries, and power generation facilities, where they are subjected to harsh conditions. The ability of an Energy Pump to operate reliably under these conditions is crucial for the smooth operation of the entire facility.
Furthermore, the durability of Energy Pumps has environmental implications. By reducing the frequency of replacements and minimizing maintenance, Energy Pumps contribute to a reduction in waste and resource consumption. This aligns with the growing emphasis on sustainability and the need to develop equipment that is not only efficient but also environmentally friendly.
In conclusion, the durability of Energy Pumps is a multifaceted attribute that is achieved through careful material selection, innovative design, precise manufacturing, and diligent maintenance. It is a critical factor in ensuring the reliability and efficiency of these pumps, which in turn contributes to the overall performance of the systems they support. As the demand for durable and sustainable industrial equipment continues to grow, the role of Energy Pumps as a reliable and long-lasting solution becomes increasingly important.
- Art
- Causes
- Crafts
- Dance
- Drinks
- Film
- Fitness
- Food
- Games
- Gardening
- Health
- Home
- Literature
- Music
- Networking
- Other
- Party
- Religion
- Shopping
- Sports
- Theater
- Wellness