Environmental Conservation in the Gas Demolition Hammer Production
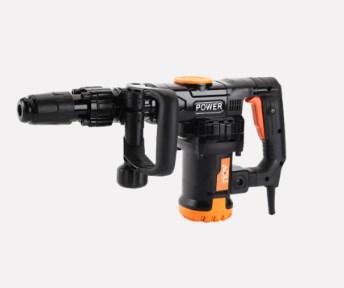
Gas demolition hammer, as a powerful tool in the construction and demolition industry, is often associated with high energy consumption and potential environmental impact. However, with the growing awareness of environmental sustainability, manufacturers are increasingly focusing on incorporating eco-friendly practices in the production process of these tools. This article delves into the various strategies and technologies that can be employed to minimize the environmental footprint of gas demolition hammers.
One of the primary ways to reduce the environmental impact of gas demolition hammers is through innovative design that enhances energy efficiency. This can be achieved by optimizing the combustion process to ensure that the hammers consume less fuel while delivering the same level of performance. Engineers can also focus on reducing the weight of the hammers without compromising their strength, which can lead to less fuel consumption during operation.
The selection of materials used in the construction of gas demolition hammers plays a crucial role in determining their environmental impact. Manufacturers can opt for recycled or biodegradable materials where possible, reducing the demand for new resources and the waste generated at the end of the hammer's life cycle. Additionally, the use of non-toxic materials can help minimize the pollution caused by the disposal of these tools.
Gas demolition hammers, like any combustion engine, emit exhaust gases that can contribute to air pollution. Implementing advanced emission control technologies, such as catalytic converters or particulate filters, can significantly reduce the emission of harmful substances. These technologies can help manufacturers meet stringent environmental regulations and contribute to cleaner air.
During the production process, waste generation is inevitable. However, manufacturers can implement waste reduction strategies, such as lean manufacturing principles, to minimize waste. Any waste that is generated can be managed through recycling programs, ensuring that materials are repurposed rather than ending up in landfills.
Water and energy conservation are also critical aspects of environmentally friendly production. Manufacturers can invest in energy-efficient machinery and lighting, as well as implement water-saving technologies. Additionally, the use of renewable energy sources, such as solar or wind power, can further reduce the carbon footprint of the production process.
Educating employees about the importance of environmental conservation and training them in sustainable practices is essential. This can include training on proper waste disposal, energy conservation, and the use of eco-friendly materials and technologies. A workforce that is aware of and committed to sustainability can significantly contribute to the overall environmental performance of the company.
Conducting a lifecycle assessment of gas demolition hammers can provide valuable insights into the environmental impact of these tools from production to disposal. This information can be used to identify areas for improvement and implement strategies to reduce the environmental footprint. Continuous improvement should be a core part of the company's environmental policy.
Adhering to environmental regulations and obtaining relevant certifications, such as ISO 14001 for environmental management systems, can demonstrate a company's commitment to sustainability. This not only helps in building a positive brand image but also ensures that the company is operating within the legal framework designed to protect the environment.
In conclusion, the production of gas demolition hammers can be made more environmentally friendly through a combination of innovative design, the use of eco-friendly materials, emission control technologies, waste reduction and recycling programs, resource, and energy conservation, employee training, lifecycle assessment, and regulatory compliance. By adopting these practices, manufacturers can ensure that their products contribute to a more sustainable future for the construction and demolition industry.
- Art
- Causes
- Crafts
- Dance
- Drinks
- Film
- Fitness
- Food
- Games
- Gardening
- Health
- Home
- Literature
- Music
- Networking
- Other
- Party
- Religion
- Shopping
- Sports
- Theater
- Wellness