The Manufacturing Strategies of Helical Gear Rack Factory
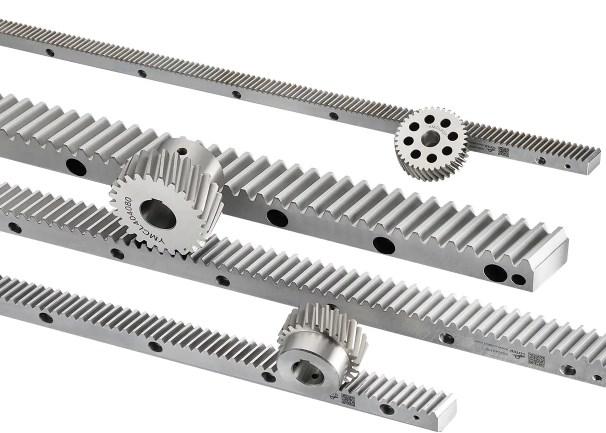
In the intricate world of mechanical engineering, the helical gear rack factory stands as a testament to the marriage of precision and innovation. These specialized facilities are dedicated to the production of helical gear racks, which are critical components in various mechanical systems, including conveyors, elevators, and machinery that requires linear motion conversion from rotational motion.
The manufacturing process within a helical gear rack factory is a symphony of advanced technology and skilled craftsmanship. It begins with the selection of raw materials, which are typically high-quality steel or aluminum alloys. The choice of material is crucial, as it directly impacts the strength, durability, and performance of the final product.
Once the material is selected, it undergoes a series of processes to shape it into the desired form. The first step is cutting the raw material into appropriate sizes and shapes using advanced cutting machines. This is followed by forging or casting, where the material is transformed into a rough form of the helical gear rack factory. The forging process involves the use of heavy machinery to shape the metal under extreme pressure, while casting involves pouring molten metal into a mold and allowing it to solidify.
After the initial shaping, the helical gear rack factory undergoes a series of heat treatments. These treatments, such as annealing, quenching, and tempering, are designed to alter the physical properties of the metal, enhancing its strength, hardness, and resistance to wear. The heat treatment process is carefully controlled to ensure that the metal reaches the desired properties without becoming brittle or losing its ductility.
The next stage in the manufacturing process is machining. This involves the use of computer numerical control (CNC) machines to accurately cut and shape the helical gear rack factory to its final dimensions. The CNC machines are programmed with precise measurements to ensure that each gear rack produced is identical and meets the stringent quality standards of the helical gear rack factory.
Once the machining process is complete, the helical gear rack factory is subjected to a series of quality control checks. These checks include visual inspections, dimensional measurements, and material testing to ensure that the gear rack meets the required specifications. Any defects or inconsistencies are identified and addressed at this stage to maintain the high standards of the helical gear rack factory.
The final stage in the manufacturing process is surface treatment. This may involve processes such as galvanizing, painting, or anodizing to protect the helical gear rack factory from corrosion and wear. The surface treatment also enhances the aesthetic appeal of the gear rack, ensuring that it is not only functional but also visually appealing.
In conclusion, the manufacturing process in a helical gear rack factory is a complex and meticulous affair. It involves a series of carefully controlled steps, from the selection of raw materials to the final surface treatment. Each stage is designed to ensure that the helical gear rack factory produced is of the highest quality, capable of withstanding the rigors of industrial applications. The dedication to precision and quality at every stage of the process is what sets a helical gear rack factory apart and guarantees the reliability and performance of its products.
- Art
- Causes
- Crafts
- Dance
- Drinks
- Film
- Fitness
- Food
- Games
- Gardening
- Health
- Home
- Literature
- Music
- Networking
- Other
- Party
- Religion
- Shopping
- Sports
- Theater
- Wellness