A Journey Through the Quality Control of Plasticine Toys
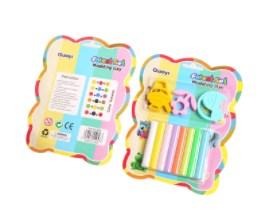
In the realm of children's entertainment, plasticine toys have carved out a niche that is both educational and creative. These malleable, colorful, and versatile toys have become a staple in the playrooms of many, offering endless possibilities for imaginative play. However, the journey from concept to creation is a complex one, with quality assurance playing a pivotal role in ensuring that every batch of plasticine toys meets the highest standards of safety, durability, and playability.
The production process of plasticine toys begins with the selection of raw materials. High-quality, non-toxic polymers are essential to ensure that the toys are safe for children. Manufacturers must adhere to stringent regulations and standards, such as those set by the ASTM (American Society for Testing and Materials) and EN71 (European Standard for Toy Safety), which dictate the acceptable levels of harmful substances in plasticine toys.
Once the raw materials are sourced, the process moves to the mixing and coloring stages. Here, pigments are carefully blended with the base polymer to achieve the vibrant hues that characterize plasticine toys. Consistency in color and texture is crucial, and manufacturers employ advanced mixing technologies to ensure uniformity throughout the batch. This step is also where quality control teams conduct initial tests for colorfastness and material integrity.
Molding is the next critical phase in the production of plasticine toys. Precision machinery is used to shape the plasticine into the desired forms, whether they be simple balls, intricate animal shapes, or complex character models. The molds must be designed to withstand repeated use without compromising the quality of the plasticine toys. Post-molding, each toy undergoes a thorough inspection to check for any defects in shape or size.
Curing is an essential step that follows molding. During this phase, the plasticine toys are allowed to set and harden, ensuring that they maintain their shape and form. The curing process must be carefully controlled in terms of temperature and duration to avoid over-hardening or under-curing, both of which can affect the playability and longevity of the toys.
After the curing process, the plasticine toys are subjected to a series of rigorous quality tests. These tests evaluate the toys' resilience, ensuring they can withstand the wear and tear of play without breaking or losing their shape. Additionally, the toys are tested for their non-toxicity, ensuring that they are safe for children to handle and play with.
Packaging is another area where quality control is paramount. The packaging must be designed to protect the plasticine toys during transportation and storage, preventing damage that could affect the toys' quality. It must also be child-friendly, with easy-open mechanisms and clear labeling that provides information about the toys' contents, age recommendations, and safety warnings.
Continuous improvement is a key aspect of quality assurance in the production of plasticine toys. Manufacturers invest in research and development to refine their processes, materials, and designs. They also stay abreast of the latest advancements in toy safety regulations and consumer preferences, ensuring that their products remain relevant and desirable in the market.
In conclusion, the production of plasticine toys is a meticulous process that involves careful attention to detail at every stage. From the selection of raw materials to the final packaging, quality is the driving force behind the creation of these beloved toys. Manufacturers must maintain a vigilant eye on every aspect of production, employing rigorous quality control measures to ensure that the plasticine toys they produce are safe, durable, and a source of joy for children worldwide.
- Art
- Causes
- Crafts
- Dance
- Drinks
- Film
- Fitness
- Food
- Games
- Gardening
- Health
- Home
- Literature
- Music
- Networking
- Other
- Party
- Religion
- Shopping
- Sports
- Theater
- Wellness