A Deep Dive into the Quality Control Processes of Plastic Cap Mould Manufacturers
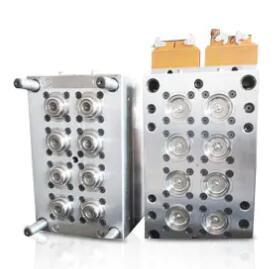
In the realm of manufacturing, precision, and quality are the cornerstones upon which the reputation of any industry is built. This is especially true for plastic cap mould manufacturers, who are tasked with the creation of intricate and essential components that secure and protect a vast array of products. The manufacturing process of these moulds is a complex one, involving numerous stages where quality control is paramount. Here, we will explore the key control points that plastic cap mould manufacturers must adhere to to ensure the highest standards of quality and functionality.
The journey of a plastic cap mould begins with its design. Manufacturers must select the appropriate materials that will withstand the rigors of the injection moulding process and the end-use environment of the caps. The design must also account for the shrinkage and warpage that can occur during the cooling phase. Quality control at this stage involves rigorous testing of material properties and the use of advanced computer-aided design (CAD) software to simulate the moulding process.
Once the design is finalized, the creation of the mould tooling begins. This is a delicate process that requires extreme precision to ensure that the mould cavities are accurate and will produce caps with the desired dimensions and tolerances. Quality control here includes the inspection of the tooling materials, the machining process, and the final assembly of the mould components.
The injection moulding process itself is a critical point for quality control. Plastic cap mould manufacturers must monitor the temperature, pressure, and injection speed to ensure that the plastic material is correctly melted, injected, and cooled within the mould. Any deviation can lead to defects such as flash, short shots, or warping.
After the caps are ejected from the mould, they undergo a series of inspections to check for dimensional accuracy, surface finish, and the presence of any defects. This may involve manual inspection, automated optical inspection systems, or even tactile measurement tools. Plastic cap mould manufacturers must ensure that their inspection processes are thorough and consistent.
Before full-scale production begins, plastic cap mould manufacturers often produce prototypes to test the functionality and performance of the caps. This testing can include torque tests, seal integrity checks, and environmental stress cracking (ESC) tests. The results of these tests feed back into the design and manufacturing process to refine the mould and production techniques.
Maintaining control over each batch of caps produced is essential for quality management. Plastic cap mould manufacturers implement batch control systems that allow for the tracking and tracing of each set of caps back to the specific mould and production run. This is crucial for identifying any issues and implementing corrective actions swiftly.
Finally, plastic cap mould manufacturers must be committed to continuous improvement. This involves regularly reviewing and updating quality control procedures, investing in new technologies, and training staff to maintain a high level of expertise. The pursuit of excellence is an ongoing process that ensures the manufacturer remains at the forefront of the industry.
In conclusion, the manufacturing process of plastic cap moulds is a meticulous and multifaceted operation that demands stringent quality control at every stage. From the initial design and material selection to the final inspection and continuous improvement efforts, plastic cap mould manufacturers play a critical role in ensuring that the caps they produce meet the highest standards of quality and performance. By adhering to these key control points, manufacturers can deliver products that are reliable, safe, and fit for purpose, ultimately contributing to the success of their clients' products in the marketplace.
- Art
- Causes
- Crafts
- Dance
- Drinks
- Film
- Fitness
- Food
- Games
- Gardening
- Health
- Home
- Literature
- Music
- Networking
- Other
- Party
- Religion
- Shopping
- Sports
- Theater
- Wellness