Exploring the Output Stability and Long-Term Operating Capabilities of Playing Cards Making Machines
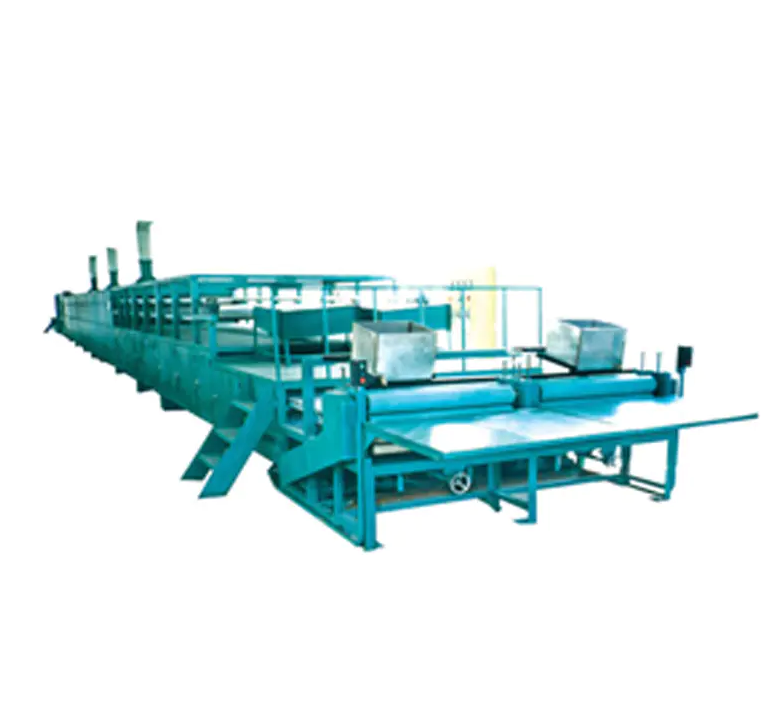
When assessing the reliability and industrial performance of printing and converting equipment, output stability and long-term operation are critical factors. This is especially true for a Playing Cards Making Machine, which is often expected to handle large production volumes for commercial or customized card decks. In today’s competitive manufacturing environment, consistent output without quality drops, system errors, or mechanical slowdowns is essential. A well-designed machine must deliver uniform performance over long shifts, whether it is operating eight hours a day or running continuously in a 24/7 production environment.
One of the key indicators of output stability is the machine’s ability to maintain print quality, cutting precision, and material feeding alignment throughout extended use. Modern systems are engineered with high-precision components such as servo motors, automated tension controls, and real-time correction sensors to ensure each card remains within exacting production standards. These features significantly reduce the chances of printing misalignment, inconsistent coating application, or cutting errors. Additionally, advanced feeders and stackers support smooth material transitions, preventing jams or irregular feeding that could cause interruptions or product defects.
Another critical factor in long-duration performance is thermal and mechanical management. Machines designed for continuous work must be equipped with cooling systems and ventilation to prevent motor overheating or electronic instability. Heat can lead to print distortion, adhesive inconsistencies, or wear on sensitive parts, so high-performance machines typically include internal monitoring systems that track temperature, vibration, and load balance. These systems can automatically slow operations or alert operators before issues affect product output. Built-in lubrication circuits and dust management also help reduce wear and prevent particle buildup that could compromise long-term function.
Automation plays a major role in maintaining steady performance. Digital control systems not only regulate speed and synchronization across multiple functions like printing, cutting, and lamination but also perform error checks during every cycle. These systems reduce the dependence on manual oversight, allowing machines to continue running with minimal human intervention while maintaining output consistency. Software-driven job management allows for automatic transition between batches or card types, which is essential for minimizing downtime and keeping production fluid over longer periods.
Regular maintenance schedules are also built into many high-end card-making machines, including programmable cleaning cycles and component diagnostics that alert operators when parts need attention. These proactive systems help avoid unexpected breakdowns that could halt production mid-cycle. When combined with proper operator training and periodic service, many machines are capable of working continuously over extended periods without significant loss of speed or precision.
In summary, the output stability of a Playing Cards Making Machine is largely dependent on the quality of its design, the integration of automated systems, and its ability to self-monitor during long-term use. Most commercial-grade machines available today are specifically engineered for continuous operation, offering the kind of reliability needed in high-demand production environments. With the right settings, environmental conditions, and maintenance support, these machines can consistently produce thousands of cards per hour across multiple shifts, maintaining both quality and efficiency throughout the production cycle.
- Art
- Causes
- Crafts
- Dance
- Drinks
- Film
- Fitness
- Food
- Games
- Gardening
- Health
- Home
- Literature
- Music
- Networking
- Other
- Party
- Religion
- Shopping
- Sports
- Theater
- Wellness