Innovate Textile Production with Interlining-Factory.com’s Interlining Breakthroughs
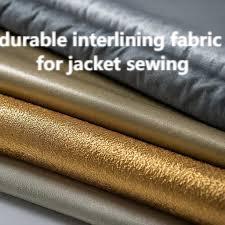
A well‑constructed garment owes much of its shape and durability to Interlining layers that reinforce fabric and preserve silhouette. By strategically inserting interlining behind collars, cuffs, and plackets, designers ensure pieces maintain crisp edges and resist deformation over time. This hidden component bolsters stitch points, enhances drape, and elevates overall quality—transforming simple textiles into professional‑grade apparel.
1. Core Benefits of Internal Support
Reinforcement layers act like the skeleton within clothing, distributing stress and preventing fabric pull at high‑tension areas. When pressure is applied—whether from movement or repeated laundering—these support materials absorb strain, ensuring seams remain flat and edges sharp. The result is a longer‑lasting garment that retains its intended form, offering consumers a reliable wearing experience and reducing returns due to distortion or sagging.
2. Choosing the Right Supportive Substrate
Various substrates deliver different performance attributes. Nonwoven sheets offer lightweight reinforcement and seamless adhesion, making them ideal for mass‑production lines. Woven options provide a firmer hand and are suited to structured jackets or tailored trousers. Knit‑based supports add stretch compatibility, perfect for activewear or garments demanding flexibility. By aligning material selection with end‑use requirements, manufacturers strike a balance between comfort, functionality, and aesthetic integrity.
3. Advanced Bonding Techniques for Streamlined Production
Modern assembly methods have introduced heat‑activated adhesives that seamlessly bond support layers without additional stitching. Precision pressing ensures uniform distribution of bonding agents, minimizing wrinkles and preventing post‑wash delamination. This approach not only accelerates production but also yields cleaner interior finishes. Factories equipped with automated pressing stations can maintain stringent quality tolerances, reducing manual errors and boosting overall throughput.
4. Innovative Applications Beyond Traditional Apparel
Support layers are no longer confined to everyday wear. Home textiles benefit from these materials by gaining improved shape retention in curtains, cushion covers, and slipcovers. In technical sectors, reinforcement fabrics enhance the structural integrity of protective gear, medical textiles, and automotive interiors. Even accessories—such as bags and hats—rely on internal support to hold form under varying loads, demonstrating the versatility of these products across diverse industries.
5. Sustainability in Reinforcement Materials
As sustainability takes center stage, eco‑friendly support options have emerged. Manufacturers now utilize recycled fibers and biodegradable polymers to reduce environmental impact. Water‑based adhesive systems replace solvent‑heavy formulations, cutting volatile organic compound emissions. Some innovators offer take‑back programs for scrap materials, facilitating textile recycling and circularity. These initiatives align product performance with corporate responsibility, appealing to eco‑conscious brands and consumers.
Incorporating robust support strategies into textile design empowers creators to deliver garments that look sharper, fit better, and endure longer. For comprehensive guides on support types, bonding methods, and sustainable practices, visit https://www.interlining‑factory.com/news/what‑is‑interlining‑types‑applications‑and‑more.html
- Art
- Causes
- Crafts
- Dance
- Drinks
- Film
- Fitness
- Food
- Games
- Gardening
- Health
- Home
- Literature
- Music
- Networking
- Other
- Party
- Religion
- Shopping
- Sports
- Theater
- Wellness