Kunliwelding Grind‑Free Welding Solutions With ER4943 Precision Wire
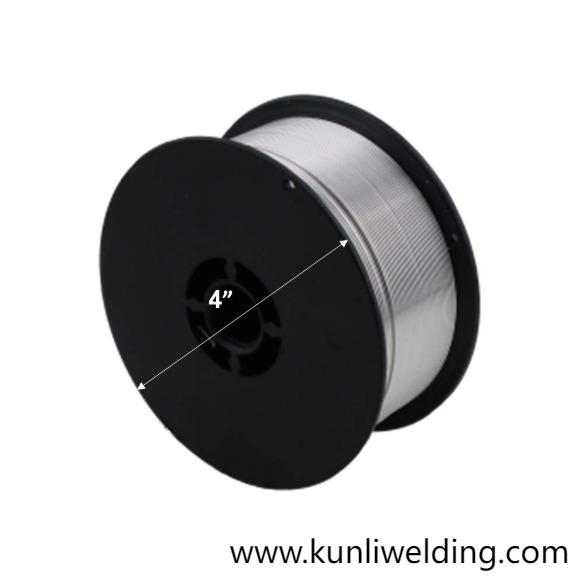
As global industries pursue lighter, more efficient structures, Aluminum Welding Wire ER4943 stands out for its exceptional surface finish and grind‑free seam forming on high‑strength extrusions. Recent shifts toward electric vehicle production and sustainable rail systems have placed a premium on filler metals that combine easy feed stability with smooth bead profiles. This guide explores the unique characteristics of this alloy and shows how fabricators can harness its benefits to streamline assembly and finishing workflows.
This wire's hallmark is its compatibility with specialized "no‑grind" forming techniques. When applied to high‑tensile aluminum profiles, it creates weld beads so uniform that manual dressing becomes unnecessary. As renewable energy infrastructure expands, components like mounting rails and battery housings demand consistent surface quality for both aesthetic and functional reasons. By eliminating post‑weld grinding, teams reduce labor hours and mitigate particulate emissions in finishing zones, aligning with clean manufacturing initiatives.
The alloy's chemistry balances strength and formability. Fabricators working in automotive pilot lines report that joints made with this wire exhibit fine grain structures in the heat affected zone, boosting fatigue resistance under cyclic loading. In transport applications-from high‑speed rail couplers to lightweight chassis brackets-such resilience translates into longer service life and reduced maintenance costs. Engineers appreciate the ability to achieve precise penetration without risking burn‑through on thin‑wall sections.
Robotic welding cells benefit greatly from stable wire feeding. In smart factories where sensors monitor arc voltage and deposition rate in real time, fluctuations in wire diameter or surface finish can trigger false alarms and halt production. Precision drawing processes and oxide removal treatments ensure that each spool maintains uniform dimensions, allowing automated systems to run without interruption. This reliability supports just‑in‑time assembly lines and helps manufacturers meet aggressive delivery schedules.
Detail‑focused applications such as architectural façade panels also gain from this wire's properties. Seam visibility and paint adhesion depend on bead smoothness and minimal undercut. When architects specify clean joint lines for exterior cladding, using ER4943 filler metal ensures that the welded seams blend seamlessly with surrounding surfaces. This capability has attracted attention in urban renewal projects, where modern designs call for both structural integrity and visual cohesion.
Surface oxidation control further distinguishes this filler metal. Advanced cleaning baths and controlled storage conditions minimize residual film on the wire surface, reducing spatters and improving arc stability. In environments undergoing heightened scrutiny for workplace air quality, lowering spatter generation not only enhances operator comfort but also eases the burden on ventilation and extraction systems. This dual benefit reinforces commitments to both productivity and employee welfare.
Integration with real‑time monitoring tools amplifies process visibility. Fabricators can link data from seam cameras and thermal scanners to wire lot identifiers, creating digital records of joint formation from start to finish. Such traceability aids quality auditors and supports rapid troubleshooting when deviations occur. By mapping detailed performance metrics to specific spools, teams drive continuous improvement and refine parameter sets for future production runs.
Training and knowledge sharing accelerate the adoption of these advanced welding methods. Virtual reality simulations allow operators to practice torch oscillation patterns and wire feed adjustments in a risk‑free environment. Live workshops led by experienced welding engineers delve into best practices for extrusion joint design, optimizing travel speed and arc length to achieve consistent bead geometry. This hands‑on guidance helps bridge the gap between theoretical advantages and shop floor realities.
Supply chain agility rounds out the value proposition. Fabricators benefit from suppliers that maintain regional stock of this speciality wire, ensuring prompt delivery even when demand surges. Flexible packaging options-ranging from small test coils to bulk spools-enable workshops to scale orders according to project needs. By partnering with a responsive wire provider, manufacturing teams mitigate lead time risks and preserve production continuity.For a detailed look at how this high‑performance filler metal is transforming industrial joining, visit www.kunliwelding.com .
- Art
- Causes
- Crafts
- Dance
- Drinks
- Film
- Fitness
- Food
- Games
- Gardening
- Health
- Home
- Literature
- Music
- Networking
- Other
- Party
- Religion
- Shopping
- Sports
- Theater
- Wellness