Why Supplier Management Software Is Now a Must-Have for Compliance Teams
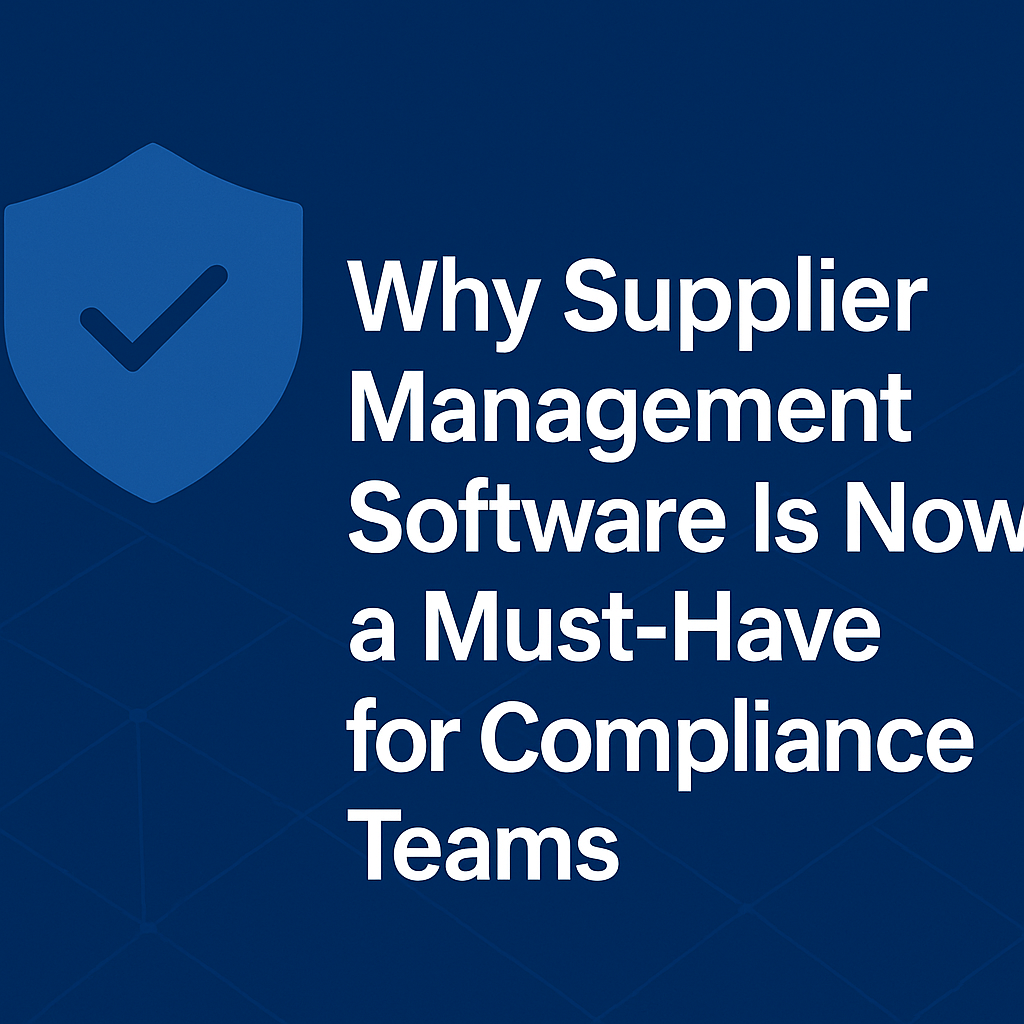
Introduction: A Tectonic Shift in Regulatory Expectations
Compliance teams across life sciences and manufacturing sectors are facing an unprecedented surge in regulatory scrutiny. With increasingly complex supply chains and global sourcing dynamics, managing supplier relationships manually or through fragmented tools is no longer viable. For organizations operating in highly regulated environments—like pharmaceuticals, medical devices, aerospace, and high-tech manufacturing—ensuring supplier quality, traceability, and accountability has become mission-critical. This is where supplier management software plays a transformative role. It is no longer a luxury or a ‘nice-to-have’—it is now an operational necessity.
The Growing Regulatory Burden on Compliance Teams
Tighter Regulations Across Global Markets
From FDA’s CFR 21 Part 820 to EU MDR, and from ISO 13485 to IATF 16949, global regulatory bodies are enforcing rigorous guidelines around supplier qualifications, performance monitoring, and product safety. Compliance teams are expected to maintain detailed records of supplier quality and ensure that every material, component, or service aligns with organizational standards.
Real-Time Auditing and Continuous Quality Assurance
Compliance is no longer periodic; it is perpetual. Quality assurance is expected to be integrated into the supplier lifecycle—right from onboarding to phase-out. Manual systems or siloed solutions lack the agility and visibility required for real-time auditing. Supplier management software enables live data capture, audit readiness, and proactive issue resolution, ensuring quality management system alignment with compliance goals.
Rising Complexity in Supply Chains Demands Smarter Systems
A Global Supplier Ecosystem
Organizations are no longer working with a handful of local suppliers. The average enterprise today manages dozens or even hundreds of suppliers across continents. The logistical, linguistic, regulatory, and operational challenges this creates are monumental. Supplier management software helps centralize supplier profiles, track global compliance, and manage risk across jurisdictions.
Multiple Tiers, Multiple Risks
With second- and third-tier suppliers now having a direct impact on product quality, companies need more than basic supplier records. A robust software solution can map tiered supplier relationships and trace critical quality assurance metrics to ensure that even upstream suppliers are held accountable.
Bridging the Gap Between Compliance and Quality
Integrated Quality Management System with Supplier Oversight
Supplier management software becomes exponentially more valuable when tightly integrated with an enterprise’s quality management system. This integration ensures that supplier performance is not viewed in isolation but is directly tied to product nonconformances, CAPAs, change controls, and audits.
Proactive vs Reactive Compliance
Legacy approaches focus on identifying problems post-production or during audits. A modern approach, enabled by software, uses predictive analytics and supplier scorecards to flag quality assurance issues before they escalate. This shift from reactive to proactive compliance not only reduces risk but also improves time-to-market.
Streamlining Supplier Onboarding and Qualification
Digitized Workflows for Speed and Consistency
Manual onboarding processes are prone to errors, delays, and inconsistent evaluations. Supplier management software enables standardized digital workflows that capture documentation, perform risk assessments, and guide approvals in a seamless manner—accelerating time to qualification without compromising quality.
Integrated Compliance Checklists and Audit Trails
Using pre-configured templates aligned with ISO, FDA, and other regulatory frameworks, compliance teams can ensure that every supplier undergoes a thorough vetting process. Built-in audit trails provide complete traceability, a crucial requirement for every quality management system quality assurance.
Real-Time Risk Assessment and Supplier Scorecards
Dynamic Risk Models for Compliance Oversight
Static spreadsheets fail to capture the dynamic nature of supplier performance and risk. Supplier management software supports real-time risk modeling, allowing compliance teams to visualize and address emerging threats quickly.
Data-Driven Supplier Scorecards
With configurable KPIs such as on-time delivery, defect rate, and responsiveness to CAPAs, scorecards generated through the software give compliance leaders a holistic view of each supplier’s reliability and alignment with quality assurance standards. These insights are vital for supplier reviews, audits, and strategic decision-making.
Ensuring Continuous Supplier Improvement
Closed-Loop Feedback for Quality Improvement
The best systems don’t just flag issues—they help solve them. Supplier management software supports a closed-loop approach where deviations, complaints, and audit findings automatically trigger corrective actions. Integrated with your quality management system, this ensures that improvement efforts are documented, monitored, and validated.
Collaborative Supplier Portals
By enabling suppliers to log in, view scorecards, submit documentation, and participate in CAPA processes, modern platforms foster a culture of transparency and continuous improvement. Compliance teams benefit from enhanced collaboration and faster issue resolution.
Preparing for the Future: AI, Automation, and Compliance
Leveraging AI for Predictive Compliance
Advanced supplier management software platforms are beginning to incorporate artificial intelligence and machine learning capabilities. These tools can analyze historical data and predict potential risks before they materialize. For compliance teams, this means fewer surprises and better preparedness.
Automation of Routine Compliance Tasks
Automation features such as document routing, renewal alerts, and automated escalation for overdue tasks reduce the administrative burden on compliance professionals. This allows teams to focus on strategic initiatives that elevate overall quality assurance.
The Strategic Role of Compliance in Business Growth
From Cost Center to Strategic Enabler
In the past, compliance was often viewed as a necessary cost. Today, it’s a critical enabler of business growth. With the right supplier management software in place, organizations can assure product quality, reduce rework, and build trust with regulatory bodies—all of which contribute to competitive advantage.
Faster Market Access and Fewer Recalls
Improved supplier visibility and quality assurance translate directly to faster regulatory approvals and fewer product recalls. This is particularly vital in sectors like medical devices and pharmaceuticals, where time-to-market and brand reputation can make or break a business.
Conclusion: Why ComplianceQuest Is Essential for Business in 2025
As the regulatory landscape continues to evolve, the demands on compliance teams will only intensify. Manual processes and fragmented systems can no longer keep pace with the speed, complexity, and accountability required in today’s global market. Supplier management software has emerged as an indispensable tool that enables quality assurance, regulatory compliance, and operational efficiency—all from a single digital platform.
ComplianceQuest offers a fully integrated, cloud-based solution built on the Salesforce platform, designed specifically for the life sciences and manufacturing sectors. By harmonizing supplier data, automating compliance workflows, and embedding quality management system best practices, ComplianceQuest empowers organizations to thrive in a high-stakes environment. In 2025 and beyond, investing in a unified supplier management platform like ComplianceQuest is not just a strategic move—it is a business imperative.
- Art
- Causes
- Crafts
- Dance
- Drinks
- Film
- Fitness
- Food
- Games
- Gardening
- Health
- Home
- Literature
- Music
- Networking
- Other
- Party
- Religion
- Shopping
- Sports
- Theater
- Wellness