How CNC Machining Aerospace Parts Is Shaping the Future of Aviation Manufacturing
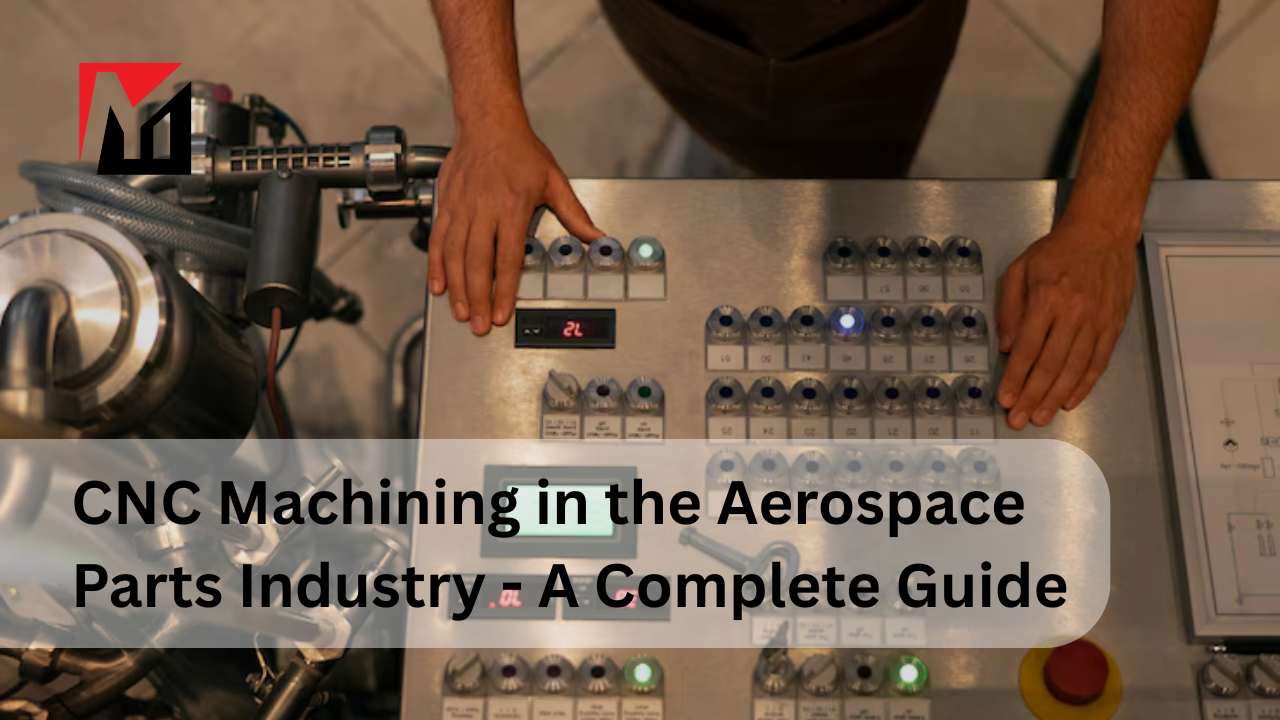
The aerospace industry has always been a symbol of precision, innovation, and complexity. Every bolt, bracket, and blade within an aircraft must perform flawlessly under extreme conditions. To meet these stringent demands, manufacturers increasingly rely on cnc machining aerospace parts for unmatched accuracy, efficiency, and quality. As aircraft designs become more advanced, CNC (Computer Numerical Control) machining remains essential to shaping parts that support performance, safety, and regulatory compliance.
This article explores how CNC machining powers the production of aerospace parts, what components it’s used for, the materials it handles, and why it's the preferred choice for manufacturers across the globe.
What Is CNC Machining?
CNC machining is a subtractive manufacturing process that uses programmed computer software to control the movement of tools and machinery. Unlike manual machining, CNC operations follow precise code that automates every movement of the tool — cutting, milling, drilling, or turning materials with high speed and accuracy.
In aerospace manufacturing, this is crucial. Tolerances often go down to ±0.0001 inches. A deviation even smaller than a human hair could affect aerodynamics, component fitment, or mechanical performance. CNC machines eliminate human error and offer repeatability for both prototype and large-scale production.
Why Aerospace Needs CNC Machining
The aerospace industry places enormous pressure on manufacturing standards. Components must:
-
Withstand extreme temperatures (from sub-zero at cruising altitudes to over 1,000°C in jet engines)
-
Handle high mechanical stress
-
Maintain lightweight structures for fuel efficiency
-
Fit together seamlessly to support safety and performance
Traditional methods like manual machining, casting, or forming often fall short of these demands. CNC machining provides:
-
Superior dimensional accuracy
-
High repeatability across production runs
-
Support for complex geometries
-
Efficient use of high-performance materials
This makes CNC technology the foundation of modern aerospace production lines.
Aerospace Components Produced with CNC Machining
CNC machining is responsible for a wide range of components in aircraft and spacecraft. Below are major categories where it plays a critical role:
1. Jet Engine Parts
Engines are among the most complex and thermally stressed areas in aerospace. CNC machines are used to make:
-
Compressor blades
-
Turbine vanes
-
Engine casings
-
Mounting brackets
These parts are typically made from titanium or Inconel, which are heat-resistant and strong but difficult to machine without advanced tools.
2. Airframe Components
The aircraft’s structural integrity depends on components such as:
-
Wing ribs and spars
-
Fuselage beams
-
Brackets and supports
-
Skin panels
These are machined from lightweight metals like aluminum and titanium to reduce overall aircraft weight while maintaining strength.
3. Landing Gear Assemblies
Landing gear must survive extreme loads during takeoff and landing. CNC machining ensures exact dimensions for:
-
Shock absorbers
-
Wheels and struts
-
Axles and arms
-
Gear housing units
High-strength alloys are used here, and precise tolerances are critical for safety and long-term durability.
4. Fuel and Hydraulic System Parts
CNC is also used to produce the intricate internal parts that manage fluid movement in aircraft:
-
Pumps and valves
-
Fluid manifolds
-
Tubing connectors
-
Reservoir housings
These components require internal channels, threading, and sealing surfaces machined to perfection to avoid leaks or system failure.
5. Cockpit and Avionics Enclosures
Modern aircraft rely on sophisticated electronics. These systems are housed in CNC-machined parts including:
-
Display enclosures
-
Instrument mounts
-
Control panels
-
Circuit board frames
These housings need to be lightweight, durable, and resistant to vibration or electromagnetic interference.
Materials Used in Aerospace CNC Machining
One of the advantages of CNC machining is its compatibility with a wide variety of aerospace-grade materials, including:
-
Aluminum Alloys: Lightweight, corrosion-resistant, and ideal for structural parts.
-
Titanium: Offers excellent strength-to-weight ratio and corrosion resistance.
-
Inconel and Superalloys: Suitable for engine and high-temperature applications.
-
Stainless Steel: Used in structural and high-stress components.
-
High-Performance Plastics: Such as PEEK and PTFE for non-metallic internal parts.
CNC machines can cut, mill, and drill these materials with extremely tight tolerances, ensuring each component meets the industry’s strict standards.
The Rise of 5-Axis CNC Machining in Aerospace
Traditional 3-axis machining is still widely used, but 5-axis CNC technology has become the gold standard in aerospace. This approach allows the tool to move along five directions simultaneously, making it possible to:
-
Create highly complex geometries
-
Reduce part repositioning
-
Improve surface finishes
-
Complete parts in fewer steps
5-axis machining also reduces setup time and minimizes human error, making it ideal for tight-deadline production environments like aerospace.
Quality Assurance and Certification
No component enters an aircraft without rigorous inspection and documentation. CNC machining for aerospace must comply with international certifications and quality assurance processes:
-
AS9100: The aerospace-specific quality management standard.
-
ISO 9001: A general quality certification required across manufacturing.
-
CMM Inspection: Coordinate Measuring Machines verify that each part matches the CAD model with micron precision.
-
First Article Inspection (FAI): Required for initial production runs.
-
Non-Destructive Testing (NDT): To inspect internal integrity without damaging parts.
CNC facilities must also ensure traceability of every part produced — logging material source, machine settings, and inspection records for every item.
Benefits of CNC Machining for Aerospace Companies
CNC machining delivers several long-term benefits for aerospace companies:
-
Reduced Lead Times: Rapid programming and setup reduce project turnaround.
-
Prototyping to Production: The same CNC program can be used to scale up.
-
Lower Scrap Rates: Accurate machining reduces waste, saving money.
-
Better Inventory Control: Precision and repeatability allow for just-in-time production.
These factors directly support the aerospace industry’s focus on efficiency, compliance, and innovation.
The Future of CNC in Aerospace
As aerospace engineering continues to evolve toward more aerodynamic and efficient designs, CNC technology is evolving with it. Future trends include:
-
AI-driven toolpath optimization
-
Digital twins and simulation
-
Automation through robotic loading
-
Integrated quality sensors
-
Hybrid manufacturing (CNC + 3D printing)
With these advancements, CNC machining will continue to lead the way in shaping next-generation aircraft, spacecraft, and unmanned aerial vehicles.
Conclusion
The aerospace industry operates at the cutting edge of human engineering. Every component must perform flawlessly under the most extreme conditions. In this high-stakes environment, cnc machining aerospace parts has become the foundation of success. It enables manufacturers to produce complex, reliable, and safe components that meet exacting standards — from design to takeoff.
Whether creating turbine blades, landing gear, avionics housings, or fuel system parts, CNC machining offers the precision, consistency, and material flexibility that aerospace demands. As technology advances, its role in the aviation sector will only grow more critical.
- Art
- Causes
- Crafts
- Dance
- Drinks
- Film
- Fitness
- Food
- Games
- Gardening
- Health
- Home
- Literature
- Music
- Networking
- Other
- Party
- Religion
- Shopping
- Sports
- Theater
- Wellness