Setting up a Moisture Meters Manufacturing Unit: Detailed Report, Cost and Requirements
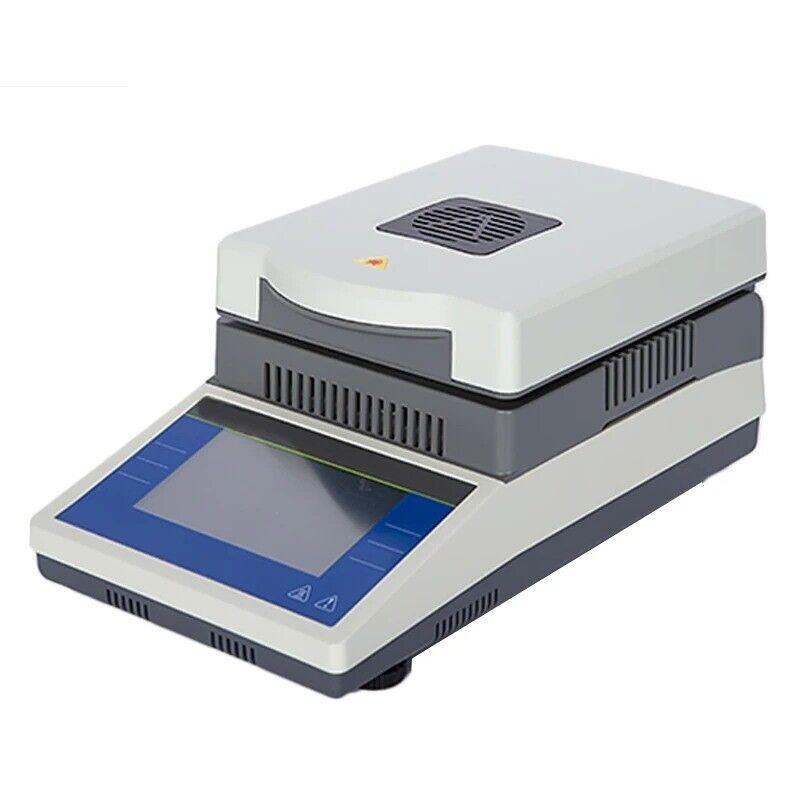
Moisture meters are precision instruments used to measure the moisture content in various materials, such as wood, concrete, soil, and textiles. They play a critical role in industries like construction, agriculture, and manufacturing by ensuring materials meet required standards before use. They can be operated using different technologies, including pin-type sensors that penetrate the material and pinless sensors that use electromagnetic waves for non-destructive testing. They are available in several types, including wood moisture meters, concrete moisture meters, and soil moisture meters, each designed for specific applications. Their importance lies in preventing material degradation, mold growth, and structural damage caused by excessive moisture. They also contribute to quality control in industries like paper production and textile manufacturing. Additionally, they offer cost savings by preventing material waste and minimizing repairs.
Several factors drive the demand for moisture meters. One of the primary factors contributing to this requirement is the growing construction and building materials sector for assessing material quality and ensuring structural integrity. In confluence with this, the increasing adoption of precision agriculture practices acts as another key driver, as farmers rely on moisture meters for efficient soil management, optimal irrigation, and enhanced crop yields. Additionally, the food and beverage (F&B) industry leverages these devices to maintain product quality during storage and transportation, reducing the risk of spoilage. Another notable trend supporting the market growth is the continuous advancement in technologies, including the integration of digital sensors, real-time data analysis, and wireless connectivity.
IMARC Group’s comprehensive report serves as a vital guide for anyone interested in setting up a moisture meters manufacturing plant by detailing all crucial steps involved, including location analysis, plant layout, machinery selection, and resource management. The report also thoroughly examines the moisture meters manufacturing business cost, offering a detailed breakdown of both capital investment and recurring operational expenses. This enables entrepreneurs and investors to make informed decisions regarding budgeting and financial planning. By covering these essential aspects, the report ensures that readers have a clear understanding of the financial and logistical requirements needed to launch and sustain a successful manufacturing business.
Key factors for setting up a moisture meters manufacturing plant:
1. Market Research
These innovations improve measurement accuracy and operational efficiency. The emphasis on sustainability and resource management further drives the demand, as moisture meters enable water conservation and prevent material wastage. Moreover, the pharmaceutical industry is emerging as a key trend, utilizing these devices to ensure compliance with quality standards and avoid costly product defects. Expanding e-commerce platforms and the availability of portable, user-friendly devices are also increasing market accessibility and user adoption. As industries continue to prioritize accuracy, efficiency, and sustainability, the market is experiencing steady growth, offering advanced solutions for diverse applications.
The report offers an exhaustive overview of the global moisture meters manufacturing industry, including a detailed breakdown by segments and regions within the sector. It also includes in-depth analyses of prices involved, market trends and historical data and forecast.
- Market Trends
- Market Breakup by Segment
- Market Breakup by Region
- Price Analysis
- Market Forecast
2. Planning and Designing
A detailed and up-to-date business plan is indispensable for mapping out the steps to establish and operate a moisture meters manufacturing facility. This report offers in-depth details about the process flow and the various unit operations involved in a moisture meters manufacturing production plant.
- Product Overview
- Unit Operations Involved
- Mass Balance and Raw Material Requirements
- Quality Assurance Criteria
- Technical Tests
Request for a Sample Report: https://www.imarcgroup.com/moisture-meters-manufacturing-plant-project-report/requestsample
3. Legal and Regulatory Compliance
Understanding and complying with the intricate framework of business laws and regulations is a vital aspect of establishing a moisture meters manufacturing facility. This requires a detailed knowledge of legal obligations, such as labour laws, environmental standards, tax policies, and industry-specific regulations.
4. Plant Requirements and Costs
The report offers a detailed location analysis, including insights into land selection, key criteria, location importance, environmental considerations, and associated costs for establishing a moisture meters manufacturing facility. It also provides information on plant layout and the factors that impact its design.
- Land, Location and Site Development
- Plant Layout
- Machinery Requirements and Costs
- Raw Material Requirements and Costs
- Packaging Requirements and Costs
- Transportation Requirements and Costs
- Utility Requirements and Costs
- Human Resource Requirements and Costs
Browse the Full Report with the Table of Contents: https://www.imarcgroup.com/moisture-meters-manufacturing-plant-project-report
5. Hiring and Training
Effective workforce planning and recruitment strategies are critical for assembling a skilled and efficient team to manage a moisture meters manufacturing plant. This process includes identifying the specific skills and qualifications needed for different roles and anticipating future staffing requirements based on production goals and business expansion.
- Complying with Labor Laws and Regulations
- Implementing Training Programs for Employees
- Developing Health and Safety Protocols
6. Supply Chain Management
Building strong partnerships with suppliers and vendors is crucial to maintaining a dependable and cost-efficient supply chain. This requires choosing partners who can reliably deliver high-quality raw materials and components at competitive rates.
- Implementing Efficient Inventory Management Systems
- Planning Logistics and Transportation Networks
7. Project Economics
This entails a thorough analysis of the costs associated with a moisture meters manufacturing plant, covering capital expenditure (CapEx), operating expenditure (OpEx), income forecasts, taxation, depreciation, liquidity, profitability, payback period, net present value (NPV), uncertainty, sensitivity assessments, etc. In addition to this, it includes an in-depth review of financial assistance options and a comprehensive list of certifications necessary for establishing the plant.
- Capital Investments
- Operating Costs
- Expenditure Projections
- Revenue Projections
- Taxation and Depreciation
- Profit Projections
- Financial Analysis
8. Marketing and Distribution Strategies:
Creating a robust marketing strategy and establishing strong brand positioning are vital for building a manufacturing plant’s market presence. This process includes conducting thorough market research to identify customer needs, preferences, and competitive trends.
- Identifying Distribution Channels and Sales Networks
- Leveraging Digital Marketing and E-Commerce Platforms
- Participating in Trade Shows and Industry Events
About Us: IMARC Group is a global management consulting firm that helps the world’s most ambitious changemakers to create a lasting impact. The company excel in understanding its client’s business priorities and delivering tailored solutions that drive meaningful outcomes. We provide a comprehensive suite of market entry and expansion services. Our offerings include thorough market assessment, feasibility studies, company incorporation assistance, factory setup support, regulatory approvals and licensing navigation, branding, marketing and sales strategies, competitive landscape, and benchmarking analyses, pricing and cost research, and procurement research.
Contact Us:
IMARC Group
134 N 4th St. Brooklyn, NY 11249, USA
Email: sales@imarcgroup.com
Tel No:(D) +91 120 433 0800
United States: +1–631–791–1145
- Art
- Causes
- Crafts
- Dance
- Drinks
- Film
- Fitness
- Food
- Games
- Gardening
- Health
- Home
- Literature
- Music
- Networking
- Other
- Party
- Religion
- Shopping
- Sports
- Theater
- Wellness