Industrial Coating Market Analysis Indicates Expansion in Marine and Heavy Equipment Segments
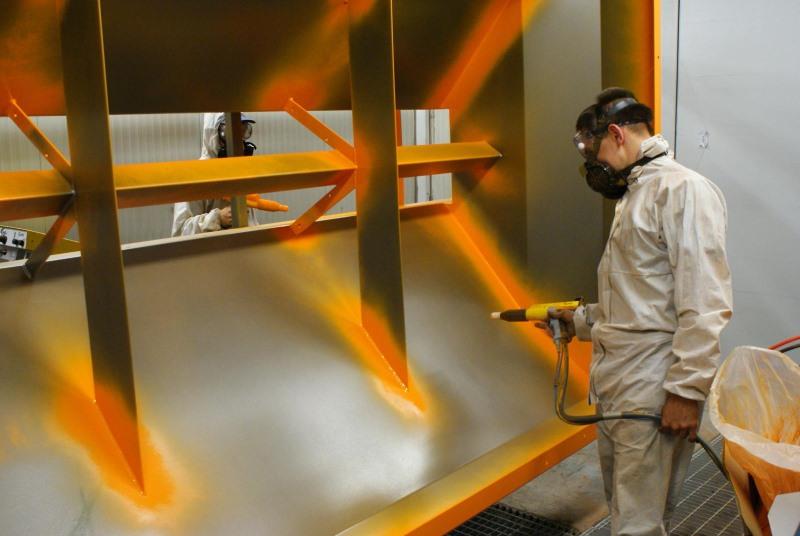
The Industrial Coating Market is experiencing notable growth driven by increased demand in the marine and heavy equipment sectors. These industries present some of the harshest operating environments, requiring specialized coatings that offer corrosion resistance, impact protection, UV stability, and extended service life. As fleets and equipment scale globally, the need for advanced, high-performance coatings in these segments is more critical than ever.
Marine Industry: Battling Corrosion on All Fronts
Marine vessels, whether cargo ships, offshore rigs, or naval ships, face relentless exposure to saltwater, humidity, and extreme weather. This harsh environment accelerates corrosion, impacting structural integrity, fuel efficiency, and long-term performance.
Coatings in marine applications must address:
-
Salt Spray Resistance: To withstand chloride-laden water.
-
Anti-Fouling Properties: To prevent barnacle and algae buildup that increases drag.
-
Flexibility: For coating surfaces subject to mechanical stress and flexing.
-
Durability: Capable of enduring cycles of wetting, drying, and UV exposure.
Technologies like epoxy primers, polyurethane topcoats, and silicone-based foul-release coatings are increasingly used for hulls, decks, and ballast tanks. Innovations in copper-free anti-fouling coatings also align with environmental regulations banning toxic biocides.
Offshore Infrastructure: High Stakes, Zero Compromise
Offshore oil platforms and wind turbines demand ultra-durable coatings to prevent catastrophic corrosion. These structures are not only exposed to salt spray but also mechanical stress from waves, wind, and equipment movement. Here, multi-layered protective coating systems with zinc-rich primers, barrier epoxies, and elastomeric topcoats ensure longevity and safety.
Many offshore companies also adopt thermal spray aluminum (TSA) coatings, which offer sacrificial protection and excellent adhesion. The added benefit of low maintenance makes TSA a preferred solution in remote, high-risk environments.
Heavy Equipment: Facing Impact, Abrasion, and Harsh Chemicals
In mining, construction, and agriculture, heavy equipment faces abrasive particles, high temperatures, hydraulic fluids, and fuel splashes daily. Paint systems for this sector must perform under constant abuse without chipping, fading, or degrading.
Key requirements include:
-
Abrasion Resistance: Particularly for loader buckets, bulldozer blades, and excavator arms.
-
Chemical Resistance: To withstand fuels, lubricants, and soil contaminants.
-
Color Retention: For brand visibility and safety identification in rugged environments.
-
Fast-Dry Properties: For efficient OEM production line throughput.
Powder coatings and high-solid polyurethane systems are gaining traction for their superior toughness and environmental compliance, particularly as OEMs seek sustainable yet robust options.
Regional Trends Supporting Segment Expansion
-
Asia-Pacific: Booming shipbuilding industries in South Korea, China, and Japan drive marine coatings demand.
-
North America: Growth in mining and energy exploration is creating coating opportunities for oil rigs, trucks, and extractive machinery.
-
Europe: Offshore wind expansion, especially in the North Sea, boosts investment in corrosion-resistant systems.
These regional trends highlight tailored product needs, creating opportunities for localized formulations and service models.
Innovation and Custom Formulation
Given the diversity of environments and equipment types, manufacturers are focusing on customized coating systems. Smart modeling tools now allow precise prediction of coating degradation over time, enabling more accurate maintenance planning and formulation optimization.
R&D efforts are also targeting:
-
Low-temperature application coatings: For Arctic offshore structures.
-
Self-cleaning coatings: To reduce downtime on machinery.
-
Multi-functional coatings: That combine abrasion resistance, corrosion control, and antimicrobial features.
By tailoring coatings to exact operational parameters, companies reduce maintenance frequency and ensure peak equipment uptime.
Certification and Compliance Standards
Both marine and heavy equipment sectors operate under rigorous quality control standards. Certifications such as:
-
IMO PSPC (International Maritime Organization Performance Standards for Protective Coatings)
-
NORSOK standards for offshore coatings
-
ISO 12944 for corrosion protection
are mandatory for product approvals. Coating manufacturers must align with these global benchmarks to enter high-stakes procurement channels.
Competitive Dynamics and Market Positioning
Major industry players are forming strategic alliances with marine OEMs, shipyards, and heavy equipment manufacturers to provide end-to-end coating solutions. Key competitive strategies include:
-
On-site technical support for application troubleshooting
-
Digital coating monitoring tools integrated with equipment analytics
-
Warrantied lifecycle systems with guaranteed performance thresholds
Such value-added services are becoming key differentiators in an increasingly performance-driven market.
Looking Ahead
As marine logistics expand and heavy equipment usage intensifies worldwide, demand for high-durability, purpose-built coatings will continue to grow. These coatings not only enhance aesthetics but play a central role in operational efficiency and asset preservation.
The next article will examine how powder and water-based coatings are gaining popularity, offering environmentally friendly yet high-performance solutions across multiple industrial verticals.
- Art
- Causes
- Crafts
- Dance
- Drinks
- Film
- Fitness
- Food
- Games
- Gardening
- Health
- Home
- Literature
- Music
- Networking
- Other
- Party
- Religion
- Shopping
- Sports
- Theater
- Wellness