3D Printing Stainless Steel Market in Aerospace: Lightweight Design and Strength
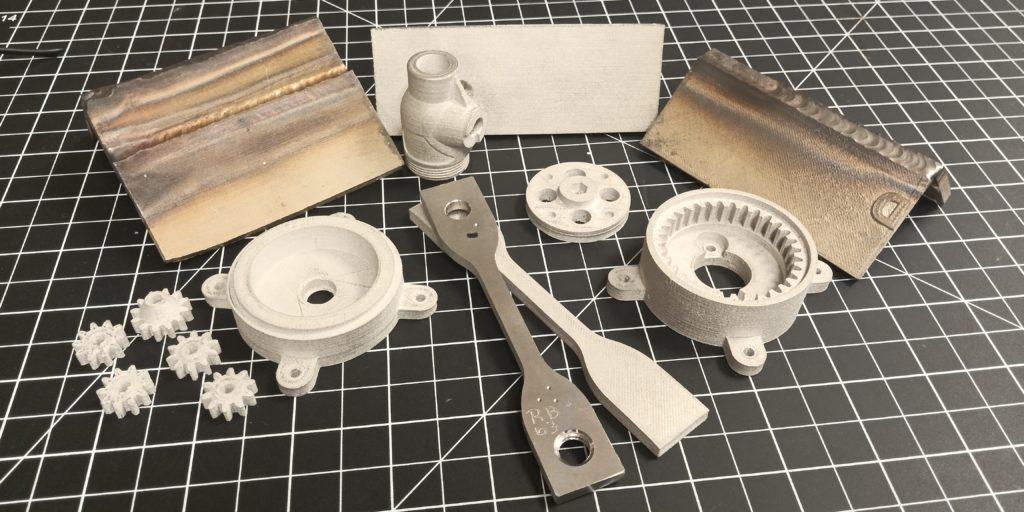
The 3D Printing Stainless Steel Market has become a pivotal enabler of innovation within the aerospace industry. With an increasing demand for lightweight yet durable materials, aerospace manufacturers are turning to stainless steel 3D printing to achieve improved performance, cost-efficiency, and design flexibility. This article delves into how the aerospace sector is leveraging 3D printing with stainless steel to advance aircraft design, streamline production, and redefine what's possible in modern aviation.
Why Stainless Steel Matters in Aerospace
Stainless steel is renowned for its corrosion resistance, mechanical strength, and temperature tolerance, making it ideal for aerospace components that operate in extreme conditions. Traditional manufacturing methods like casting and machining often face limitations in producing the complex geometries required for aerospace parts. 3D printing overcomes these limitations while maximizing material efficiency.
Key grades commonly used include:
-
316L – Excellent corrosion resistance and toughness.
-
17-4 PH – High strength and hardness with moderate corrosion resistance.
-
15-5 PH – Balanced properties for structural and engine parts.
Lightweight Design with Complex Geometries
Weight reduction is a critical goal in aerospace, as every kilogram saved translates into fuel efficiency and lower emissions. Stainless steel 3D printing enables:
-
Topology optimization: Designers can remove unnecessary material and retain only the structure that bears loads.
-
Lattice structures: These allow for lightweight yet strong internal geometries, reducing mass without compromising strength.
-
Part consolidation: Multiple components can be combined into a single printed part, reducing assembly time and potential failure points.
These capabilities are particularly useful in producing parts like:
-
Fuel nozzles
-
Brackets and mounts
-
Turbine components
-
Heat exchangers
Applications in Aerospace
-
Engine Components
The complex internal cooling channels and high-strength requirements of engine parts are well-suited to stainless steel 3D printing. It allows manufacturers to produce parts with internal features that were previously unachievable. -
Structural Supports
Lightweight, high-strength supports and brackets printed in stainless steel reduce aircraft weight and assembly complexity. -
Cabin and Interior Parts
Metal parts inside the cabin, such as seat supports or fasteners, benefit from stainless steel's strength and longevity. -
Satellite and Spacecraft Components
In satellite manufacturing, every gram counts. Stainless steel's durability and resistance to thermal expansion make it ideal for components exposed to the vacuum of space.
Advantages for the Aerospace Industry
-
Shorter Lead Times: Critical components can be produced on-demand, bypassing the long tooling times associated with traditional methods.
-
Inventory Reduction: Aerospace companies can maintain a digital inventory and produce spare parts as needed, reducing storage costs.
-
Sustainability: 3D printing generates minimal waste, which aligns with aerospace's push toward greener operations.
-
Improved Performance: Optimized designs can enhance aerodynamic properties and thermal performance.
Notable Industry Developments
-
GE Aviation has pioneered stainless steel 3D printing for its LEAP fuel nozzles, which are 25% lighter and five times more durable than traditionally manufactured versions.
-
NASA and other space agencies are exploring 3D printed stainless steel parts for space-bound missions, aiming for higher reliability and modularity.
-
Airbus and Boeing are investing heavily in additive manufacturing to streamline production and integrate smart components into future aircraft.
Challenges and Considerations
Despite the advantages, the adoption of 3D printing stainless steel in aerospace is not without hurdles:
-
Regulatory Compliance: Aerospace components must meet rigorous safety and reliability standards. Certification for 3D printed parts remains complex and time-consuming.
-
Material Consistency: Ensuring batch-to-batch consistency in stainless steel powders is essential for reliable mechanical performance.
-
Post-Processing Requirements: Printed parts often require heat treatment, machining, or surface polishing to meet aerospace-grade specifications.
-
High Equipment Costs: The initial investment in industrial-grade printers and controlled environments is substantial.
Market Outlook and Future Potential
The aerospace segment is expected to be a major contributor to the growth of the 3D Printing Stainless Steel Market over the next decade. With a projected CAGR of over 20% in aerospace applications, the market is likely to witness:
-
Greater integration of AI and simulation tools in part design and stress testing.
-
Adoption of hybrid manufacturing methods that blend additive and subtractive techniques for better finishing and precision.
-
Expansion into commercial and defense aviation for both new aircraft models and maintenance, repair, and overhaul (MRO) services.
Conclusion
The integration of stainless steel 3D printing into aerospace manufacturing is no longer a future possibility—it's a current reality reshaping how aircraft are designed, built, and maintained. With capabilities that enable lightweight construction, greater design freedom, and enhanced performance, the 3D Printing Stainless Steel Market is poised to become a foundational technology for the next generation of aerospace innovation. As adoption scales and technology matures, the skies are truly the limit for additive manufacturing in this high-stakes industry.
- Art
- Causes
- Crafts
- Dance
- Drinks
- Film
- Fitness
- Food
- Games
- Gardening
- Health
- Home
- Literature
- Music
- Networking
- Other
- Party
- Religion
- Shopping
- Sports
- Theater
- Wellness