Revolutionizing Liquid Handling in Manufacturing with the IBC Tote Mixer
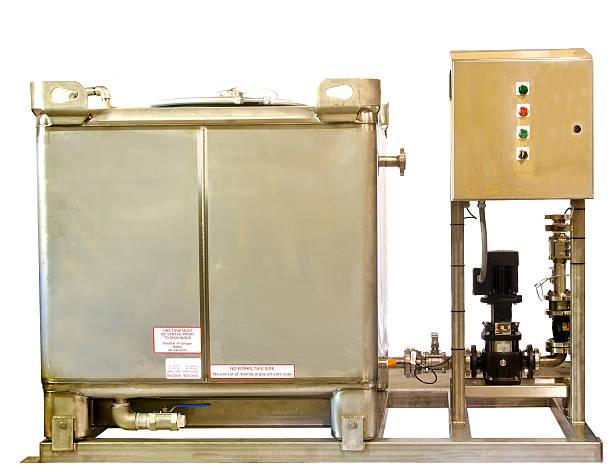
Introduction to Smart Liquid Mixing
In today’s high-speed industrial environment, manufacturers are constantly under pressure to improve efficiency, reduce waste, and maintain product consistency. These challenges are especially pronounced when handling liquids in bulk. The ibc tote mixer has emerged as a vital solution to these challenges, offering a way to mix directly within Intermediate Bulk Containers, minimizing transfer losses and maximizing output efficiency.
Streamlined Process and Reduced Downtime
Traditionally, liquid mixing required multiple containers, transfers, and cleaning cycles. Each of these steps introduced the potential for product loss and contamination. The ibc tote mixer streamlines this entire process. It allows mixing to take place inside the same container used for storage and transport. This not only reduces the number of steps involved but also cuts down on downtime between batches, making operations leaner and more responsive.
Consistency in Every Batch
Manufacturing liquid-based products demands precision. Inconsistencies can affect quality, customer satisfaction, and regulatory compliance. The ibc tote mixer ensures that contents are evenly blended from top to bottom. Its strategically designed mixing blades or paddles are capable of reaching deep into the container, agitating dense materials and light liquids alike. The result is uniform composition, whether mixing simple solutions or complex chemical compounds.
The Role in Regulatory Compliance
Industries such as pharmaceuticals, food and beverage, and personal care are governed by strict regulatory frameworks. Every component used in the production process must meet certain hygiene and safety standards. The ibc tote mixer supports compliance by promoting clean-in-place protocols and reducing opportunities for contamination. Many mixers are constructed from stainless steel and other FDA-compliant materials, ensuring safe use in sensitive production environments.
Cost-Effective for Both Large and Small Operations
One of the most compelling advantages of using an ibc tote mixer is its ability to provide high performance without excessive cost. It makes use of existing IBCs, so there is no need to purchase additional tanks. This cost-saving approach is ideal not only for large-scale manufacturers but also for smaller producers who require efficiency on a budget. Over time, savings accumulate from reduced labor, energy, and maintenance expenses.
Supporting Agile Manufacturing
In a world where consumer demands shift rapidly, manufacturers need to be agile. The ibc tote mixer allows for quick changes between products and formulas. With minimal cleanup and setup required between uses, businesses can pivot more easily to accommodate new production runs. This adaptability gives a competitive edge in fast-moving markets.
Conclusion
The ibc tote mixer has become an indispensable tool in modern manufacturing. By combining efficiency, hygiene, cost-effectiveness, and adaptability, it redefines how industries handle liquid blending. Whether for chemicals, food, or cosmetics, this equipment empowers manufacturers to meet production demands with confidence and precision.
- Art
- Causes
- Crafts
- Dance
- Drinks
- Film
- Fitness
- Food
- Games
- Gardening
- Health
- Home
- Literature
- Music
- Networking
- Other
- Party
- Religion
- Shopping
- Sports
- Theater
- Wellness