Can a laser cleaner replace traditional methods of industrial cleaning effectively?
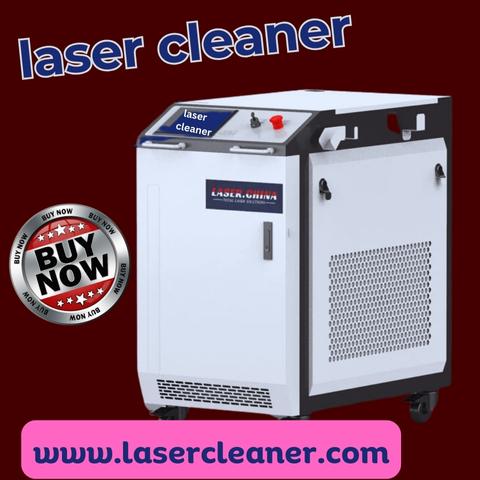
In recent years, industries have seen a significant shift towards cleaner, more efficient technologies. One such innovation is the laser cleaner, a modern solution that is steadily gaining ground over traditional cleaning methods. But, the question arises: can a laser cleaner truly replace conventional cleaning techniques like abrasive blasting, chemical cleaning, or even sandblasting? This is a highly relevant query in a time when environmental concerns and workplace safety are more important than ever.
Laser cleaning technology is an advanced method that uses high-intensity laser beams to remove contaminants, rust, and coatings from surfaces. This process works by directing short pulses of laser light at a specific target, which causes the contaminants to vaporize or be ejected from the surface. What makes it truly revolutionary is that it’s not just effective but incredibly precise, capable of cleaning delicate surfaces without causing damage. This allows manufacturers and service providers to focus on cleaner, safer, and more sustainable operations.
But how does this technology stack up against traditional cleaning methods? Let’s delve deeper into the various ways laser cleaner technology is changing the game in industrial cleaning.
The Rise of Laser Cleaning Technology
Laser cleaning is a relatively new innovation in the industrial cleaning space, but it has already started to make waves. The core technology is based on directing a focused laser beam onto a target surface. The energy from the laser is absorbed by contaminants on the surface, causing them to either vaporize or be blown away. This high level of precision allows it to be used on a variety of surfaces, including delicate materials and complex geometries, which makes it an attractive alternative to traditional methods.
The laser cleaning process works by emitting a concentrated laser beam onto the surface. When the beam hits the surface, it interacts with the contaminants, whether it's rust, old paint, or dirt. The intense energy causes the contaminants to absorb the laser’s heat, which can cause the dirt or rust to either evaporate or be blasted off the surface. Unlike traditional methods that often involve abrasive tools or chemicals, laser cleaning offers a precise, non-invasive alternative.
Laser Cleaners: A Cleaner Future for Industries
One of the primary challenges of traditional cleaning techniques is their reliance on abrasives or chemicals. These cleaning methods, though effective in many cases, often result in considerable wear on the equipment or the treated surface. They can also introduce hazardous materials into the environment, contributing to pollution and making disposal more difficult.
Laser cleaners are different. The technology is inherently more sustainable, as it doesn’t require the use of chemicals or abrasive materials. This makes it a more environmentally friendly option, especially when considering industries that regularly use hazardous substances for cleaning purposes. Furthermore, the laser cleaning process itself doesn’t produce waste, unlike sandblasting or chemical treatments, which generate harmful by-products.
The versatility of the laser cleaner is also a key point of interest. It can be used to clean various types of surfaces, from metals to delicate electronic components, without causing any harm to the underlying material. Traditional methods, on the other hand, may cause abrasions, scratches, or other irreversible damage, especially when dealing with sensitive or delicate surfaces.
Laser Cleaning vs. Traditional Methods
Let’s take a closer look at how laser cleaner technology stacks up against some of the traditional cleaning methods:
-
Abrasive Blasting: Traditional abrasive blasting uses sand, grit, or other materials to scrub contaminants from surfaces. While effective, this method can cause wear and tear on the material being cleaned, leading to surface degradation over time. In contrast, laser cleaning uses a precise beam that doesn’t physically touch the surface, eliminating the risk of abrasions and damage.
-
Chemical Cleaning: Chemical cleaners are widely used for removing rust and coatings, but they often introduce harmful substances into the environment. Disposal of these chemicals can be costly and may require special handling procedures. Laser cleaning does not use any chemicals, making it a more eco-friendly option.
-
Ultrasonic Cleaning: This method involves using high-frequency sound waves to clean materials, often submerged in a bath of cleaning liquid. While effective for some applications, ultrasonic cleaning requires the use of water and chemicals, which introduces the possibility of contaminants. In comparison, laser cleaners don’t need any liquids, making them more efficient and reducing the risk of contamination.
The laser cleaner stands out for its precision, speed, and lack of secondary waste. It’s effective in various industrial applications, from cleaning complex components in the automotive and aerospace industries to delicate electronics and heritage conservation.
The Environmental Impact
One of the major selling points of laser cleaner technology is its minimal environmental footprint. Traditional cleaning methods often involve chemicals, abrasive materials, or even water, all of which require proper disposal. In contrast, laser cleaning uses only light energy, resulting in no waste by-products.
The energy required for laser cleaning is also relatively minimal compared to the energy consumed by abrasive cleaning methods or the production of chemicals used in cleaning solutions. This is particularly appealing for companies looking to reduce their environmental impact or improve their sustainability credentials.
Another environmental benefit is the ability of laser cleaners to precisely target contaminants without affecting the underlying material. For example, when cleaning rust from steel, a laser cleaner can remove the rust without damaging the steel, unlike sandblasting, which may wear down the metal over time.
Cost Efficiency and Operational Considerations
While the initial investment in a laser cleaner can be higher than that of traditional cleaning equipment, the long-term savings often outweigh the initial costs. Traditional methods may require the constant purchase of chemicals, abrasives, or other consumables, which can add up over time. Laser cleaners, on the other hand, are more efficient in the long run, as they don’t require any consumables beyond the energy needed to operate the laser.
Additionally, the labor involved in traditional cleaning methods is often more intensive. Operators need to manage materials, ensure that the cleaning process doesn’t damage the surface, and handle waste disposal. With a laser cleaner, the process is automated to a large extent, reducing the need for manual intervention and making it more efficient in the long run.
Precision and Safety
One of the standout features of laser cleaners is their ability to clean surfaces with a high degree of precision. This precision allows laser cleaners to be used on delicate components, such as electronic devices or fine art, where traditional methods would be too abrasive or risky.
Laser cleaning also offers a safer working environment. Many traditional methods, such as abrasive blasting, require operators to wear protective gear due to the risk of dust or chemical exposure. Laser cleaning, being a non-contact method, poses fewer risks to workers. Additionally, the laser cleaning process generates minimal dust and no chemical fumes, which improves workplace safety and reduces the need for expensive ventilation systems.
Applications in Various Industries
Laser cleaners are already being used across a wide range of industries. In the aerospace sector, for example, laser cleaning can be used to remove contaminants from delicate parts without causing any damage to the components. In the automotive industry, laser cleaning is used to prepare surfaces for coating or welding without damaging the underlying material. Similarly, laser cleaning is being used in the conservation of heritage artifacts, where traditional cleaning methods would be too aggressive or harmful.
The versatility of laser cleaner technology means it has the potential to revolutionize industries beyond manufacturing. From electronics and art conservation to the restoration of historical buildings, laser cleaning can be applied to a variety of surfaces and substrates.
Final Thoughts
The laser cleaner is quickly proving to be an effective alternative to traditional industrial cleaning methods. While it may not be suitable for every application, it offers clear advantages in terms of precision, safety, and environmental impact. For industries looking to streamline their cleaning processes, reduce waste, and improve workplace safety, the laser cleaner offers a solution that is not only efficient but sustainable. As technology continues to evolve, we can expect to see more widespread adoption of laser cleaning, making it an essential tool for the future of industrial cleaning.
- Art
- Causes
- Crafts
- Dance
- Drinks
- Film
- Fitness
- Food
- Games
- Gardening
- Health
- Home
- Literature
- Music
- Networking
- Other
- Party
- Religion
- Shopping
- Sports
- Theater
- Wellness