The Sound of Precision: Noise Levels in Hydraulic Angle Steel Cutter Applications
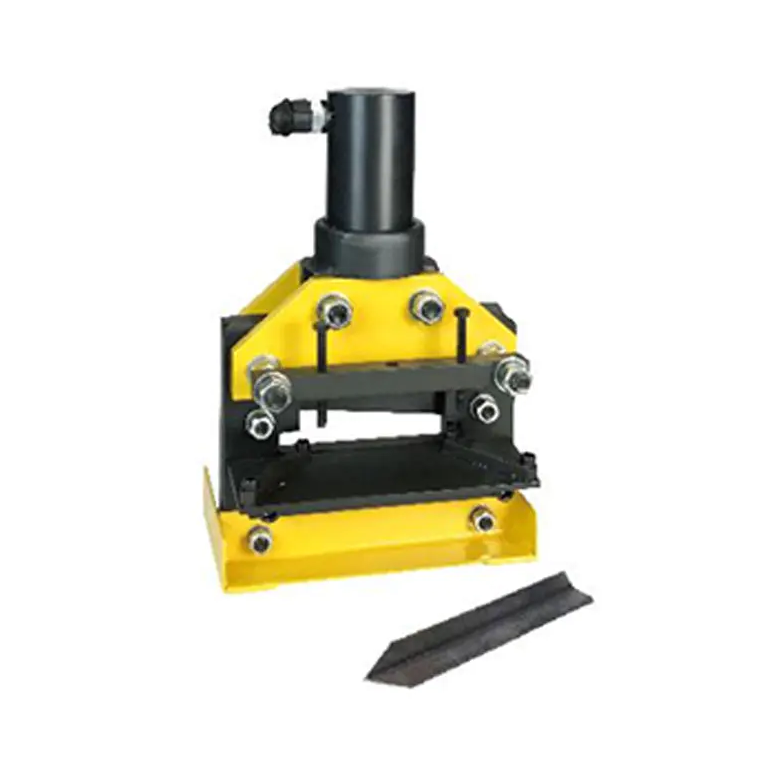
Noise pollution is a significant concern in industrial settings, affecting both worker health and safety as well as the surrounding environment. Hydraulic Angle Steel Cutters, despite their efficiency and precision in cutting operations, are not exempt from this consideration. The noise levels generated by these machines are a critical factor that manufacturers must address to ensure compliance with industrial noise standards and to maintain a safe working environment.
The Hydraulic Angle Steel Cutter, a powerful tool in metal fabrication, is designed to withstand the rigors of heavy-duty cutting tasks. However, these operations are not without their auditory consequences. The noise generated by a Hydraulic Angle Steel Cutter can be attributed to several factors, including the force exerted during the cutting process, the movement of mechanical components, and the interaction between the cutter and the material being cut.
One of the primary contributors to the noise level of a Hydraulic Angle Steel Cutter is the hydraulic system itself. Hydraulic systems involve the rapid movement of fluids under pressure, which can result in high noise levels due to the flow of pressurized fluids through valves and the operation of pumps. The design of the hydraulic system, including the type and size of the pump, the configuration of the hydraulic lines, and the presence of noise-dampening features, can all impact the overall noise level of the Hydraulic Angle Steel Cutter.
Another factor influencing the noise level is the cutting process itself. The speed at which the Hydraulic Angle Steel Cutter operates, the type of material being cut, and the precision required for the cut can all affect the noise generated. High-speed operations can lead to increased noise due to the rapid movement of the cutter and the resulting vibrations. Additionally, harder materials, such as steel, can produce more noise when cut compared to softer materials due to the increased resistance encountered during the cutting process.
The construction and materials of the Hydraulic Angle Steel Cutter also play a role in noise levels. Cutters with sturdy, well-built frames can help dampen vibrations that contribute to noise. Furthermore, the use of high-quality, wear-resistant materials can reduce the noise associated with friction and wear during operation.
To mitigate the noise levels produced by Hydraulic Angle Steel Cutters, manufacturers often employ various noise reduction strategies. These can include the use of sound enclosures or barriers to contain the noise at the source, the implementation of noise-cancelling technologies within the hydraulic system, and the incorporation of vibration-damping materials in the cutter's construction.
Regulatory standards, such as the Occupational Safety and Health Administration (OSHA) guidelines in the United States, set permissible noise exposure levels to protect workers from the harmful effects of noise-induced hearing loss. Compliance with these standards is crucial for operators of Hydraulic Angle Steel Cutters, necessitating the use of personal protective equipment such as earplugs or earmuffs when noise levels exceed the recommended limits.
In conclusion, the noise level of Hydraulic Angle Steel Cutters is a complex issue that involves a multitude of factors, including the hydraulic system, the cutting process, and the cutter's construction. By understanding these factors and implementing noise reduction strategies, manufacturers can ensure that their Hydraulic Angle Steel Cutters operate within acceptable noise levels, protecting both worker safety and the surrounding environment. The ongoing development of quieter Hydraulic Angle Steel Cutters is essential for meeting the evolving demands of industries where noise pollution is a critical concern.
Output(T): 20
Angle Iron(mm): ≤6
Angle Steel Width(mm): 75x75x6
Net Weight(kg): 33
Gross Weight(kg) :36
Wooden Box Size(mm): 270x155x420
- Art
- Causes
- Crafts
- Dance
- Drinks
- Film
- Fitness
- Food
- Games
- Gardening
- Health
- Home
- Literature
- Music
- Networking
- Other
- Party
- Religion
- Shopping
- Sports
- Theater
- Wellness