The Evolution and Manufacturing Process of Resin Zippers
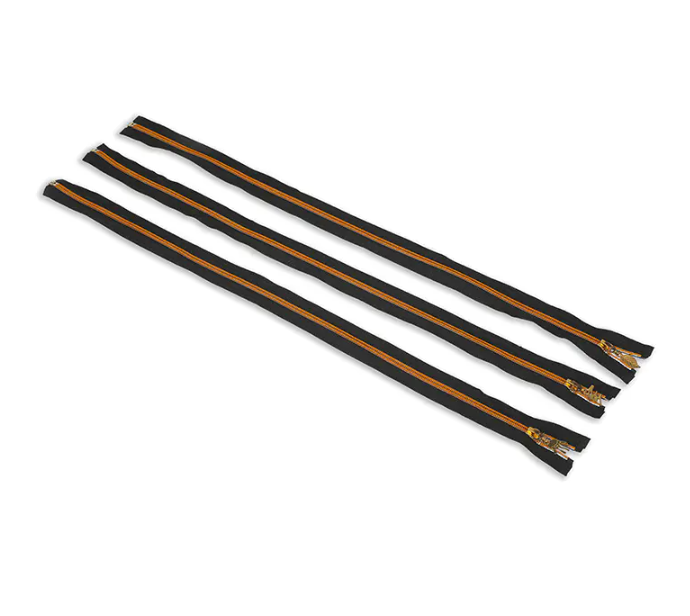
Resin zippers have evolved over the years to become an essential component in various products, ranging from apparel to outdoor equipment. Unlike traditional metal zippers, resin zippers are made from plastic materials, offering a range of benefits that have made them increasingly popular in different industries. Understanding the manufacturing process and the materials used in resin zipper production can provide insight into their widespread adoption.
The primary material used in resin zippers is plastic, typically polyethylene terephthalate (PET) or polyacetal (POM). These materials are selected for their durability, resistance to corrosion, and ability to withstand moisture and environmental stress. The manufacturing process begins with the injection molding of plastic parts, which involves injecting molten plastic into molds to create the zipper's teeth and slider components. This process ensures that the parts are consistent in size and shape, allowing for a smooth operation once assembled.
One of the advantages of using plastic for zippers is its flexibility. Unlike metal zippers, which can be rigid and heavy, resin zippers are lightweight, making them ideal for products that require ease of handling, such as clothing, bags, and tents. Resin zippers can be manufactured in various colors and finishes, providing manufacturers with the ability to create customized zippers that suit the design and functionality of the product. The smooth texture and customizable appearance make resin zippers a preferred choice for industries where aesthetics are important.
The production of resin zippers involves several stages, including the molding of zipper teeth, the attachment of the slider, and the final assembly. In the molding stage, the plastic material is heated to a molten state and injected into molds to form the individual teeth. The teeth are then sewn onto the fabric or tape of the zipper, with the slider inserted later to facilitate the opening and closing of the zipper. The result is a finished zipper that is both functional and aesthetically appealing.
While resin zippers offer numerous advantages, there are some challenges in their production. For instance, the precision required in molding the teeth and aligning them with the fabric can lead to variations in quality. Additionally, the environmental impact of plastic production and the long-term durability of resin zippers under heavy use are considerations that manufacturers must address.
In conclusion, the manufacturing of resin zippers is a sophisticated process that involves molding plastic materials into functional and customizable parts. Their lightweight nature, corrosion resistance, and design flexibility make them a popular choice for a variety of products. As the demand for lighter, more sustainable alternatives to metal zippers grows, resin zippers are likely to continue playing a significant role in the manufacturing of everyday items.
- Art
- Causes
- Crafts
- Dance
- Drinks
- Film
- Fitness
- Food
- Games
- Gardening
- Health
- Home
- Literature
- Music
- Networking
- Other
- Party
- Religion
- Shopping
- Sports
- Theater
- Wellness