Advanced High Strength Steel Market Sees Investment Booms as EV Manufacturing Spurs Lightweight Material Prioritization Globally
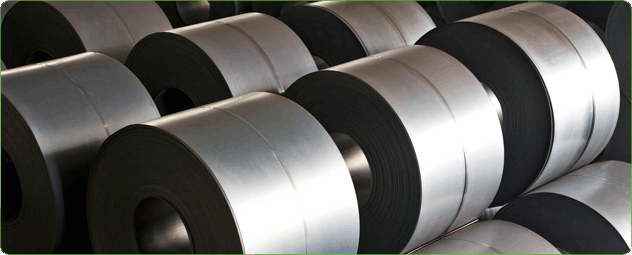
The advanced high strength steel market is currently witnessing a surge in global investments, spurred by the escalating demand for lightweight materials in electric vehicle (EV) manufacturing. As automakers race toward a future dominated by sustainable mobility and zero-emission targets, advanced high strength steel (AHSS) has emerged as a cornerstone material — delivering a rare combination of strength, flexibility, and cost efficiency. This growing emphasis on material innovation is transforming the competitive landscape and driving significant capital inflows into AHSS production and R&D.
Electric vehicles, with their heavy battery systems and complex safety requirements, are fundamentally altering the materials game in automotive design. To achieve optimal performance and efficiency, manufacturers are prioritizing lightweight solutions that can reduce overall vehicle mass without compromising crash protection. AHSS offers the ideal balance: it's significantly lighter than traditional steel, yet strong enough to enhance occupant safety and maintain structural integrity in the event of a collision.
This capability is critical in EV production, where every kilogram matters. Lower vehicle weight translates directly to extended driving range, better energy efficiency, and reduced wear on tires and mechanical systems. As a result, the advanced high strength steel market has become a focal point for automakers and suppliers investing in next-generation EV platforms. Global giants like Tesla, BMW, Toyota, and Hyundai are increasingly incorporating AHSS into chassis, safety cages, and body-in-white components, often in partnership with steel producers who are rapidly scaling up capacity to meet demand.
Investment in the AHSS sector is not limited to OEMs alone. Steel manufacturers are pouring resources into advanced processing facilities, smart metallurgy technologies, and environmentally friendly production methods. Innovations like hot stamping, dual-phase steel, and third-generation AHSS are gaining traction, allowing for more complex geometries and better crash performance while keeping costs manageable. Furthermore, green steel initiatives — including hydrogen-based production and carbon capture integration — are aligning AHSS manufacturing with global sustainability goals, attracting even more investor interest.
From a regional perspective, Asia-Pacific leads the way in AHSS market investment, thanks to its dominant role in both EV production and steel manufacturing. China, Japan, and South Korea are home to some of the most technologically advanced steel plants and EV factories, creating a synergistic ecosystem that supports AHSS innovation. Meanwhile, North America and Europe are experiencing a second wave of investments, driven by government-backed EV incentives, clean energy policies, and a surge in EV startups demanding high-performance materials.
Yet, despite the booming interest, the AHSS market faces some challenges. High development and processing costs, along with the need for specialized forming and welding equipment, can slow adoption — particularly among smaller automakers or in emerging markets. However, as economies of scale improve and training expands across manufacturing sectors, these barriers are expected to diminish.
Looking ahead, the advanced high strength steel market is poised for sustained growth, underpinned by the global shift toward electric mobility and sustainable industrial practices. As EV adoption accelerates, the strategic importance of AHSS will only increase, driving further innovation and investment. In this material revolution, AHSS stands as a critical enabler — reinforcing the future of transportation while meeting the urgent demands of a decarbonized world.
- Art
- Causes
- Crafts
- Dance
- Drinks
- Film
- Fitness
- Food
- Games
- Gardening
- Health
- Home
- Literature
- Music
- Networking
- Other
- Party
- Religion
- Shopping
- Sports
- Theater
- Wellness