Industrial Valve Market to Benefit from Rising Automation in Industrial and Processing Facilities Globally
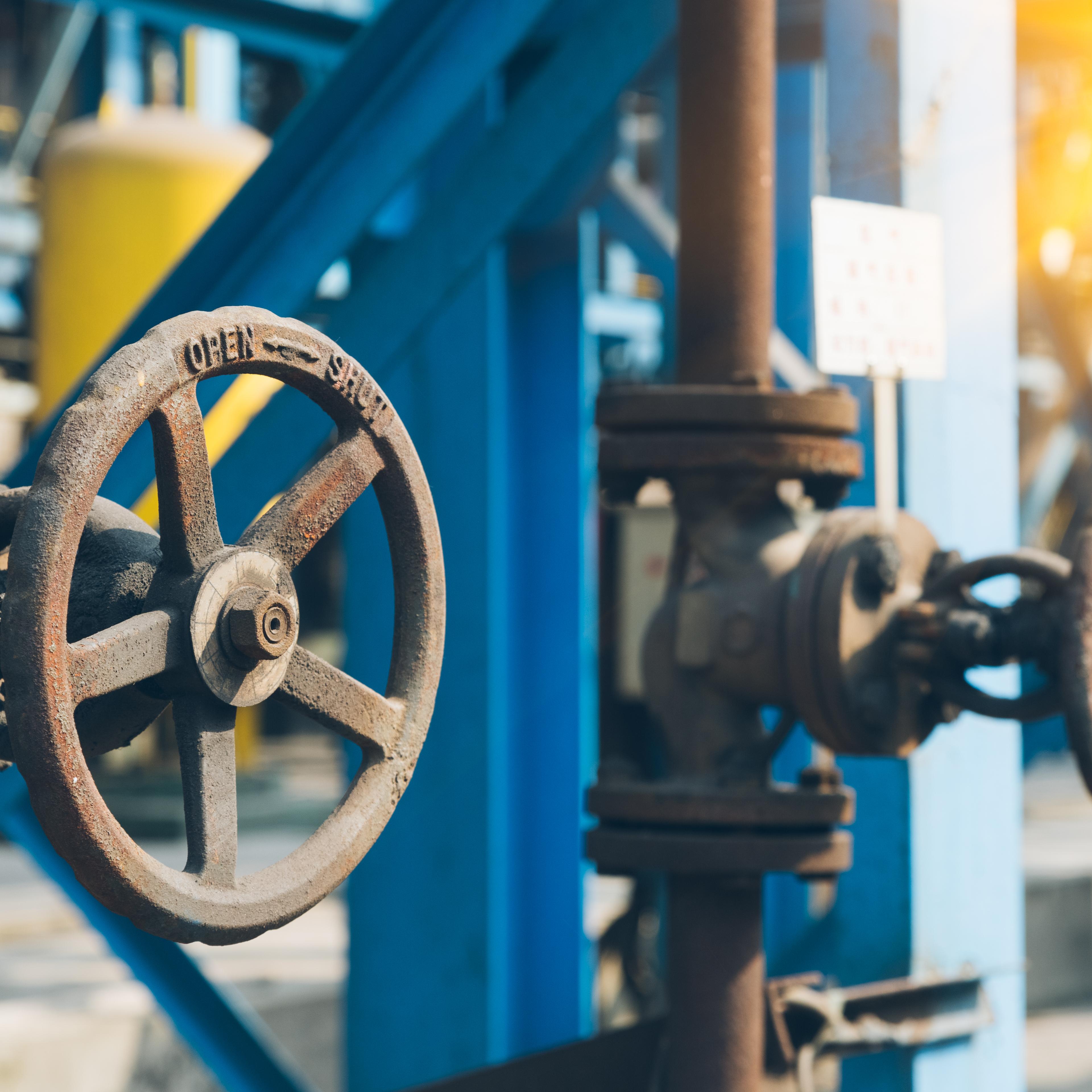
The Restraints in the Industrial Valve Market: An In-Depth Look
The industrial valve market plays a crucial role in various sectors such as oil and gas, water treatment, power generation, and manufacturing. Valves control the flow of liquids, gases, and slurries, ensuring the safe and efficient operation of systems. However, despite the market's significant growth potential, several factors hinder its expansion and development. These restraints, ranging from technological challenges to environmental regulations, impact the industry's growth trajectory. In this blog, we will explore the primary restraints affecting the industrial valve market.
1. High Initial Investment Costs
One of the most significant restraints in the industrial valve market is the high initial investment required for valve manufacturing and installation. Industrial valves are complex mechanical devices that require precise engineering, testing, and material selection. As such, their production can be costly, particularly for valves used in high-pressure and high-temperature applications like those found in the oil and gas industry.
The installation of these valves also involves significant costs related to labor, training, and specialized equipment. For smaller companies or those in developing markets, the high upfront costs can be prohibitive. In many cases, businesses may opt for lower-cost alternatives or delay upgrades to their existing valve systems, which can limit market growth.
2. Strict Regulatory and Environmental Standards
The industrial valve market is heavily influenced by strict regulatory and environmental standards. As industries such as oil and gas, chemicals, and water treatment increasingly face scrutiny over their environmental impact, the demand for valves that comply with these regulations has grown. However, the regulatory landscape is complex and varies by region, making it challenging for manufacturers to develop products that meet all the required standards.
The tightening of environmental regulations, such as those aimed at reducing emissions or improving water efficiency, can restrict valve designs and the materials used in manufacturing. This increases the cost of production and can limit the introduction of new valve technologies that may offer improved performance but fail to meet environmental standards. Additionally, industries may struggle to retrofit existing systems to comply with new regulations, which could delay the adoption of advanced valve solutions.
3. Competition from Alternative Technologies
The industrial valve market faces increasing competition from alternative technologies and products that can perform similar functions. For example, automated flow control systems and digital sensors are gaining popularity due to their ability to optimize performance and reduce maintenance costs. These technologies can often replace traditional mechanical valves, especially in applications where precise control and real-time monitoring are essential.
As automation and digitalization become more widespread, industries may shift towards more advanced systems that reduce the need for traditional valves. This trend poses a challenge for the valve market, as manufacturers must continually innovate to ensure that their products remain competitive and relevant in a rapidly evolving technological landscape.
4. Limited Skilled Labor and Technical Expertise
The industrial valve market requires a highly skilled workforce for design, manufacturing, installation, and maintenance. Engineers and technicians must have specialized knowledge to work with complex valve systems, especially those used in critical industries such as aerospace, energy, and pharmaceuticals.
However, there is a global shortage of skilled labor in engineering and technical fields. This shortage creates a bottleneck in the valve manufacturing process, as companies struggle to find qualified workers to meet increasing demand. Additionally, the training required to maintain and repair valves is intensive, which can increase operational costs for businesses that rely on these components. Without a steady supply of qualified personnel, the market may experience delays in valve production and installation, restricting overall growth.
5. Fluctuating Raw Material Prices
The prices of raw materials used in industrial valve manufacturing, such as stainless steel, brass, and other alloys, can fluctuate significantly due to various factors, including geopolitical tensions, supply chain disruptions, and global demand shifts. These price variations can directly impact the cost of producing valves, as manufacturers may face increased costs for sourcing high-quality materials.
Fluctuating raw material prices can also affect the pricing of finished valves, making it difficult for manufacturers to maintain consistent profit margins. In some cases, these cost fluctuations can lead to price instability in the market, which may cause delays in production or discourage customers from making large-scale investments in valve systems.
6. Economic Uncertainty and Market Volatility
Global economic conditions, including recessions, trade wars, and political instability, have a significant impact on the industrial valve market. During periods of economic uncertainty, industries may reduce capital expenditures or delay major projects, directly affecting demand for valves. The oil and gas industry, for example, is highly sensitive to global economic fluctuations, and changes in commodity prices can lead to postponed investments in infrastructure and equipment, including valves.
Additionally, the ongoing volatility in global supply chains, driven by factors such as pandemics and trade disruptions, has created uncertainty in the industrial valve market. Supply chain issues can result in delays, higher costs, and an overall slowdown in market growth.
Conclusion
While the industrial valve market presents significant opportunities, it is not without its challenges. High initial costs, regulatory pressures, competition from alternative technologies, labor shortages, raw material price fluctuations, and economic instability all contribute to the restraints faced by the industry. To remain competitive and foster growth, valve manufacturers must navigate these obstacles by embracing innovation, improving efficiency, and staying adaptable in the face of evolving market demands and technological advancements. Overcoming these challenges will be crucial for unlocking the full potential of the industrial valve market in the years to come.
- Art
- Causes
- Crafts
- Dance
- Drinks
- Film
- Fitness
- Food
- Games
- Gardening
- Health
- Home
- Literature
- Music
- Networking
- Other
- Party
- Religion
- Shopping
- Sports
- Theater
- Wellness