Welding Consumables Market: Regional Insights and Competitive Landscape for Global and Local Players
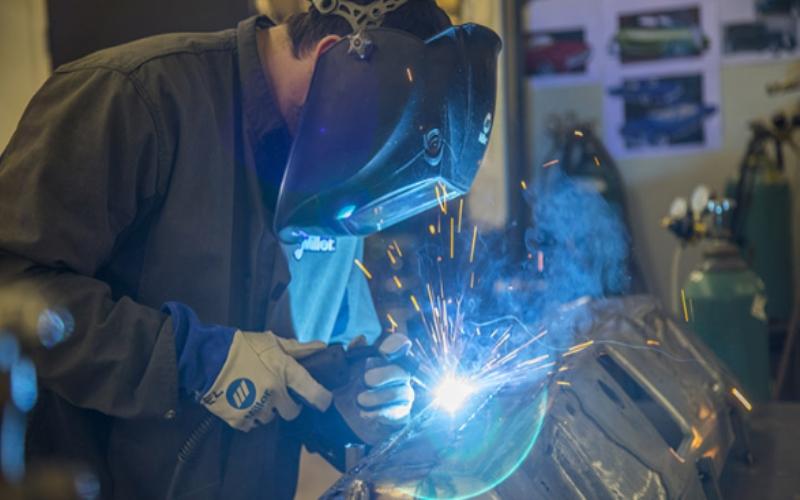
Welding is a crucial process in many industries, from manufacturing and construction to automotive and aerospace. Central to this process is the use of welding consumables, which play an essential role in ensuring strong, durable, and high-quality welds. Welding consumables refer to the materials used in the welding process, such as electrodes, filler rods, flux, and shielding gases. These materials not only help in forming a weld but also protect it from contaminants and oxidation. As the demand for welding grows across various industries, the market for welding consumables has seen significant expansion.
Market Overview
The welding consumables market has experienced steady growth over the past decade. The global market is driven by the increasing demand for welded products, particularly in construction, infrastructure, automotive, shipbuilding, and energy sectors. According to industry reports, the global welding consumables market was valued at over USD 15 billion in 2020 and is projected to grow at a compound annual growth rate (CAGR) of approximately 5% over the next several years.
This growth is attributed to several key factors, including industrial advancements, increased construction activities, and the rising need for durable materials in modern machinery. The demand for high-performance consumables that can withstand extreme conditions such as high temperatures, corrosion, and pressure is also a major driver.
Key Trends Driving Market Growth
-
Technological Advancements: As industries become more demanding in terms of quality and performance, there has been a steady shift towards high-performance welding consumables. Companies are investing in research and development to produce consumables that offer better reliability, longer service life, and enhanced weld quality. Moreover, the rise of automated and robotic welding systems has further emphasized the need for precise and high-quality consumables. This has led to the development of more advanced flux-cored wires, electrodes, and filler materials.
-
Sustainability Focus: With the increasing emphasis on sustainable manufacturing practices, there is a growing demand for eco-friendly and low-emission welding consumables. Many companies are now focusing on creating consumables that produce fewer harmful by-products during the welding process. These consumables not only help in reducing environmental impact but also comply with the tightening regulations regarding industrial emissions.
-
Rise in Construction and Infrastructure Projects: One of the most significant drivers of the welding consumables market is the growth in construction and infrastructure projects. Emerging economies, particularly in Asia-Pacific, are witnessing a boom in construction activities, which is leading to an increase in demand for welding consumables. The rise in infrastructure projects such as roads, bridges, and airports, as well as the increasing demand for residential and commercial buildings, is driving the consumption of welding materials.
-
Industrialization and Manufacturing Expansion: Another key trend contributing to market growth is the expansion of the manufacturing sector. As global industrial production increases, especially in automotive, heavy machinery, and oil and gas industries, the demand for welding consumables rises. The automotive sector, in particular, is seeing the adoption of more advanced welding techniques, requiring specialized consumables to handle new materials and meet stricter quality standards.
Market Segmentation
The welding consumables market can be segmented into several categories, each catering to specific industry needs:
-
Product Type:
-
Welding Electrodes: These are among the most widely used consumables, particularly in manual welding processes. Electrodes are available in various types, including coated, bare, and flux-cored electrodes. The choice of electrode depends on factors such as welding position, material to be welded, and the environmental conditions.
-
Filler Materials: These include filler rods, wires, and powder that are added to the joint during welding to form a strong bond. These materials are commonly used in processes like MIG (Metal Inert Gas) welding and TIG (Tungsten Inert Gas) welding.
-
Shielding Gases: Gases like argon, carbon dioxide, and helium are essential in protecting the weld pool from contamination during the welding process. The use of the right shielding gas ensures a clean, high-quality weld.
-
-
Application:
-
Construction & Infrastructure: The construction sector remains the largest consumer of welding consumables, driven by the ongoing demand for welding in building structures, bridges, and roads.
-
Automotive & Transportation: With the increasing adoption of electric vehicles (EVs) and advanced materials, the automotive industry is utilizing specialized welding consumables to address new challenges.
-
Oil & Gas: The oil and gas sector requires highly durable welding consumables to withstand harsh offshore and onshore environments, making it a key end-user segment.
-
Shipbuilding & Aerospace: These industries demand precision welding and high-performance consumables that can meet stringent standards.
-
Regional Insights
The welding consumables market is experiencing rapid growth across various regions. Asia-Pacific, led by countries like China, India, and Japan, dominates the market due to rapid industrialization, increasing construction activities, and a booming automotive sector. The region is also home to some of the largest manufacturers of welding consumables, making it a hub for both production and consumption.
North America and Europe also contribute significantly to the market, driven by advancements in manufacturing, aerospace, and automotive industries. Additionally, the adoption of green welding technologies in these regions is expected to further enhance market growth.
Challenges
Despite the overall growth, the welding consumables market faces a few challenges. One of the primary concerns is the fluctuating prices of raw materials, such as steel and copper, which directly affect the production cost of consumables. Additionally, stringent regulations regarding the environmental impact of welding processes are prompting manufacturers to innovate but also increasing operational costs. Another challenge is the need for skilled labor to effectively use advanced welding technologies, which limits the potential for automation in some markets.
Conclusion
The welding consumables market is set to continue its growth trajectory, driven by technological advancements, increasing demand from key industries, and a focus on sustainability. As welding technologies evolve and industries push for more precise, durable, and eco-friendly solutions, the market for welding consumables is likely to see even more innovation in the coming years. Companies that can adapt to these changes and provide high-quality, cost-effective consumables will find themselves in a favorable position in this competitive landscape.
- Art
- Causes
- Crafts
- Dance
- Drinks
- Film
- Fitness
- Food
- Games
- Gardening
- Health
- Home
- Literature
- Music
- Networking
- Other
- Party
- Religion
- Shopping
- Sports
- Theater
- Wellness