How does a laser machine metal cutting process create precise designs on tough metals without contact?
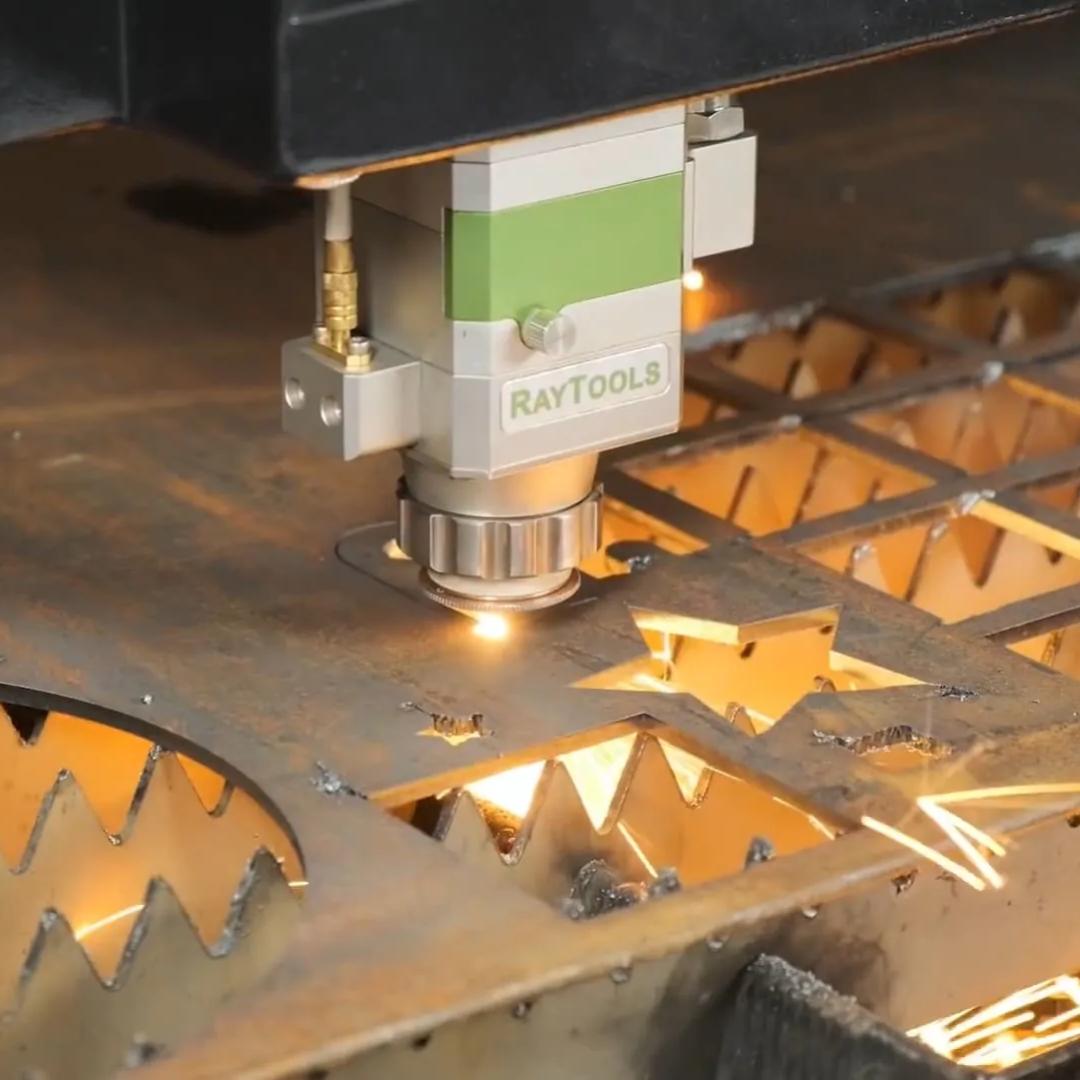
Metal cutting has evolved significantly over the years, with laser machine metal cutting emerging as one of the most advanced and efficient methods in the industry. This technique has transformed how industries approach metal fabrication, offering a non-contact, high-precision cutting solution. Whether in manufacturing, automotive, aerospace, or custom metalwork, this technology has become a game-changer.
Understanding Laser Machine Metal Cutting
At its core, a laser machine metal cutting process uses a high-powered laser beam to melt, burn, or vaporize metal. Unlike traditional cutting methods that require physical contact, this process relies on concentrated light energy to achieve sharp and clean cuts. The beam is controlled through CNC (Computer Numerical Control) systems, ensuring accuracy and intricate detailing.
The process involves directing a laser beam through optics, which then focuses on a specific point on the metal surface. The intense heat from the laser rapidly melts the material, while a stream of gas, such as nitrogen or oxygen, helps remove molten metal, leaving behind a smooth cut.
Why Laser Machine Metal Cutting Stands Out?
The uniqueness of a laser machine metal cutting process lies in its ability to handle various metal types with precision. From stainless steel and aluminum to titanium and copper, the process ensures high-quality results across different materials. The laser's capability to cut complex shapes, fine contours, and micro-sized patterns makes it an ideal choice for industries requiring accuracy.
Traditional cutting techniques often struggle with consistency and speed. In contrast, laser technology eliminates tool wear, minimizes heat-affected zones, and ensures sharp, clean edges without secondary processing. This efficiency makes it the preferred choice for high-production environments.
How Laser Machine Metal Cutting Works on Different Metals?
Each metal has unique properties, affecting how it interacts with laser cutting technology. Some metals conduct heat better, while others require specific gas combinations for optimal cutting performance.
-
Stainless Steel: One of the most commonly used metals, stainless steel responds well to laser cutting due to its heat resistance and ability to produce oxide-free cuts with nitrogen gas.
-
Aluminum: This reflective metal can be challenging to cut, but modern fiber lasers handle it efficiently by preventing excessive reflection.
-
Titanium: Known for its strength and corrosion resistance, titanium is widely used in aerospace and medical applications. Laser cutting ensures precise shaping without material wastage.
-
Copper and Brass: These highly reflective metals require specialized laser systems to avoid beam reflection and ensure effective cutting.
Applications of Laser Machine Metal Cutting
The versatility of laser machine metal cutting extends across multiple industries. From large-scale manufacturing to small businesses and custom fabrication, its applications are diverse.
-
Automotive Industry: Used for creating precise car body components, exhaust systems, and intricate parts.
-
Aerospace Industry: Essential for producing lightweight, high-strength aircraft components with minimal material distortion.
-
Medical Equipment: Used to manufacture surgical tools, implants, and other precision instruments.
-
Jewelry Making: Helps craft delicate and detailed metal designs with accuracy.
-
Architectural Projects: Assists in creating decorative metal panels, signage, and intricate designs.
Choosing the Right Laser Machine for Metal Cutting
Selecting the right laser machine metal cutting system depends on multiple factors, including material type, thickness, and production volume. The two main types of lasers used for metal cutting are CO₂ lasers and fiber lasers.
-
CO₂ Lasers: Suitable for cutting a variety of materials, including non-metals, but less effective on highly reflective metals.
-
Fiber Lasers: Specifically designed for metal cutting, fiber lasers offer faster processing speeds, high energy efficiency, and superior cutting quality.
Manufacturers often consider factors like laser power, cutting speed, operational cost, and maintenance requirements before investing in a machine. With advancements in laser technology, businesses can now integrate automated systems to enhance productivity and reduce downtime.
Safety Considerations in Laser Machine Metal Cutting
While laser machine metal cutting is a highly efficient process, it requires strict safety protocols. Operators must follow safety measures, including wearing protective eyewear, maintaining proper ventilation, and using enclosed workstations to prevent exposure to laser beams.
Additionally, since laser cutting generates heat and sparks, fire hazards must be minimized by keeping flammable materials away from the cutting area. Regular maintenance of laser components ensures consistent performance and prolongs the machine's lifespan.
Future of Laser Machine Metal Cutting
With continuous advancements in technology, the future of laser machine metal cutting looks promising. The introduction of AI-driven CNC systems, improved laser sources, and real-time monitoring systems are set to enhance efficiency and precision. As industries shift towards sustainable manufacturing, laser cutting plays a crucial role in reducing material waste and optimizing energy consumption.
Moreover, the demand for lightweight and high-strength metal components continues to rise, driving innovation in laser technology. The integration of automation and robotics in laser cutting further streamlines production processes, making it an essential tool for modern manufacturing.
Final Thoughts
The evolution of laser machine metal cutting has redefined the metal fabrication industry, offering unmatched precision, efficiency, and versatility. Its ability to cut intricate designs without physical contact has made it a preferred choice across multiple sectors. As technology continues to advance, laser cutting will remain at the forefront of innovation, helping industries achieve high-quality results with minimal effort. Whether for large-scale production or custom metalwork, investing in a reliable laser cutting machine ensures precision, speed, and long-term efficiency.
- Art
- Causes
- Crafts
- Dance
- Drinks
- Film
- Fitness
- Food
- Games
- Gardening
- Health
- Home
- Literature
- Music
- Networking
- Other
- Party
- Religion
- Shopping
- Sports
- Theater
- Wellness