Achieving Accuracy in Measurements: The Calibration of Electronic Weighing Indicators
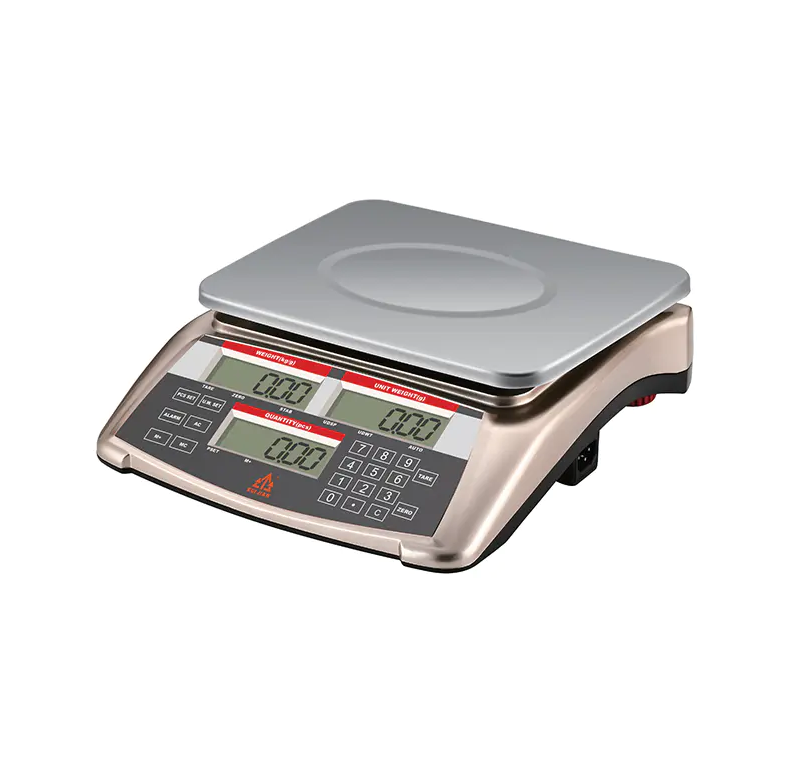
In the realm of precision measurement, the Electronic Weighing Indicator plays a critical role in various industries, from manufacturing to research and food service. Ensuring the accuracy of these devices is not only essential for quality control but also for compliance with regulatory standards. This article delves into the nuances of calibrating Electronic Weighing Indicators to guarantee their reliability and precision in weight measurement.
Calibration is the process of adjusting and verifying the performance of an Electronic Weighing Indicator to ensure that it provides accurate and consistent measurements. This is crucial because even minor inaccuracies can lead to significant errors in the final product, affecting quality and potentially leading to financial losses or safety issues.
To begin the calibration process, it is imperative to understand the specifications and requirements of the Electronic Weighing Indicator. Each model may have different settings and calibration procedures, so consulting the manufacturer's guidelines is the first step. These guidelines will provide detailed instructions on how to perform the calibration, including any necessary tools or weights required.
Before proceeding with the calibration, the Electronic Weighing Indicator should be powered off and any weights removed from the scale. This ensures that the device is in a neutral state and ready for the calibration process. It is also important to ensure that the environment in which the calibration is taking place is stable and free from vibrations, drafts, or other factors that could affect the accuracy of the device.
Once the device is ready, the calibration process can begin. This typically involves introducing known weights into the system and adjusting the settings on the Electronic Weighing Indicator until the displayed weight matches the known weight. This process may need to be repeated with multiple weights to ensure that the accuracy is consistent across the entire range of the scale.
During the calibration, it is essential to monitor the response time of the Electronic Weighing Indicator. The device should display the weight accurately and promptly without any significant delay. Any noticeable lag in the display could indicate a problem with the device that may need further investigation.
After the initial calibration, it is recommended to perform regular checks to ensure that the Electronic Weighing Indicator remains accurate over time. This can be done by using a single known weight to check the device's performance periodically. If any discrepancies are found, a full calibration may be necessary.
In addition to regular calibration, it is also important to maintain the Electronic Weighing Indicator properly. This includes keeping the device clean and free from dust or debris, which can interfere with the sensors and affect the accuracy of the measurements. Regular software updates and hardware checks can also help to ensure that the device continues to operate at peak performance.
In conclusion, the calibration of Electronic Weighing Indicators is a vital process that ensures the accuracy and reliability of weight measurements. By following the manufacturer's guidelines, performing regular checks, and maintaining the device properly, businesses can ensure that their Electronic Weighing Indicators provide the precision needed for accurate and compliant measurements. This not only helps to maintain product quality but also protects against potential legal and financial ramifications associated with inaccurate weighing.
Preventing dust and insects more effectively with an external aluminum alloy bracket
Reinforced casing for anti-drop and impact resistance.
High stability and antifreeze waterproof chip motherboard
Zemic customized load cell verification interval can be 0.1g.
- Art
- Causes
- Crafts
- Dance
- Drinks
- Film
- Fitness
- Food
- Games
- Gardening
- Health
- Home
- Literature
- Music
- Networking
- Other
- Party
- Religion
- Shopping
- Sports
- Theater
- Wellness