Stability Essentials: Optimizing Performance of Industrial Rotary Tools
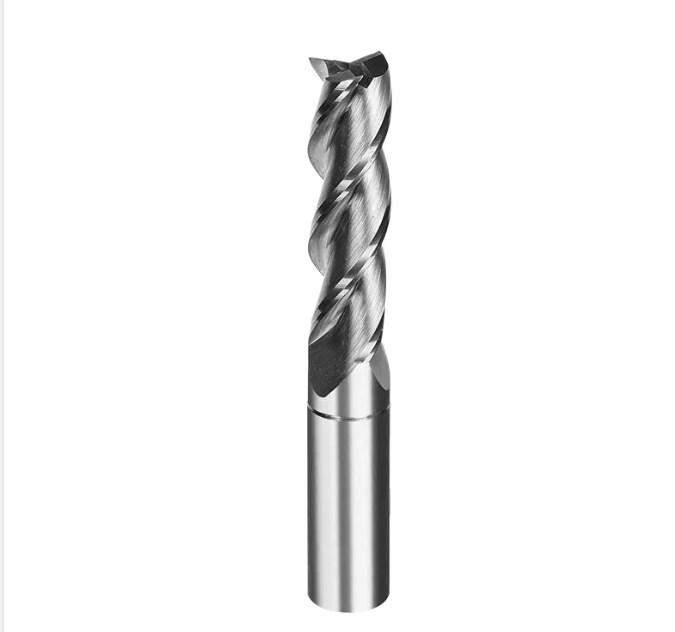
In the world of precision engineering and intricate detailing, the Industrial Rotary Tool stands out as a versatile and indispensable piece of equipment. Its ability to handle a variety of tasks, from cutting and grinding to polishing and engraving, has made it a staple in workshops across industries. However, the effectiveness of an Industrial Rotary Tool is heavily contingent upon its stability. This article explores the factors that contribute to the stability of Industrial Rotary Tools and the measures that can be taken to ensure optimal performance.
The stability of an Industrial Rotary Tool is paramount to its ability to provide clean, precise cuts and consistent results. A tool that vibrates excessively or shifts during operation can lead to uneven surfaces, broken bits, or even safety hazards. To understand how stability is maintained in Industrial Rotary Tools, we must first consider the design and construction of these tools.
The core of an Industrial Rotary Tool is its motor, which is typically designed to deliver high torque and precision. The motor's stability is crucial, as any wobble or misalignment can translate to the tool's output. High-quality Industrial Rotary Tools are often equipped with ball bearings that reduce friction and ensure smooth operation, contributing to the tool's overall stability. Additionally, the tool's housing must be robust enough to withstand the forces generated during use without flexing or deforming, which could compromise stability.
The choice of attachments for an Industrial Rotary Tool also plays a significant role in its stability. Bits and accessories that are not securely fastened can cause the tool to wobble, reducing the accuracy of the work. It is essential to use attachments that are specifically designed for the Industrial Rotary Tool to ensure a snug fit and minimize vibrations. Furthermore, the balance of the attachment is another factor that affects stability; unbalanced bits can cause the tool to vibrate, leading to an unstable cutting or engraving process.
Another aspect that cannot be overlooked when discussing the stability of Industrial Rotary Tools is the user's technique. An operator who applies uneven pressure or moves the tool erratically can introduce instability. Training and practice are essential for users to develop a steady hand and a consistent approach to using the Industrial Rotary Tool. This not only improves the stability of the tool in operation but also enhances the quality of the work produced.
The environment in which the Industrial Rotary Tool is used also impacts its stability. Vibration from nearby machinery, an unstable work surface, or poor lighting can all affect the operator's ability to maintain a steady hand. It is crucial to ensure that the work area is free from distractions and that the surface on which the tool is used is flat and stable.
Lastly, regular maintenance is key to preserving the stability of Industrial Rotary Tools. Over time, dust, debris, and wear can accumulate, affecting the tool's performance. Cleaning your tool regularly and ensuring all parts are in good condition can prevent small problems from becoming big ones that can affect the tool's reliability.
In conclusion, the stability of Industrial Rotary Tools is a multifaceted issue that involves the tool's design, the attachments used, the operator's skill, the working environment, and regular maintenance. By addressing each of these areas, users can ensure that their Industrial Rotary Tools remain stable and reliable, delivering the precision and quality that they are known for.
- Art
- Causes
- Crafts
- Dance
- Drinks
- Film
- Fitness
- Food
- Games
- Gardening
- Health
- Home
- Literature
- Music
- Networking
- Other
- Party
- Religion
- Shopping
- Sports
- Theater
- Wellness