Cap compression machines improve manufacturing efficiency
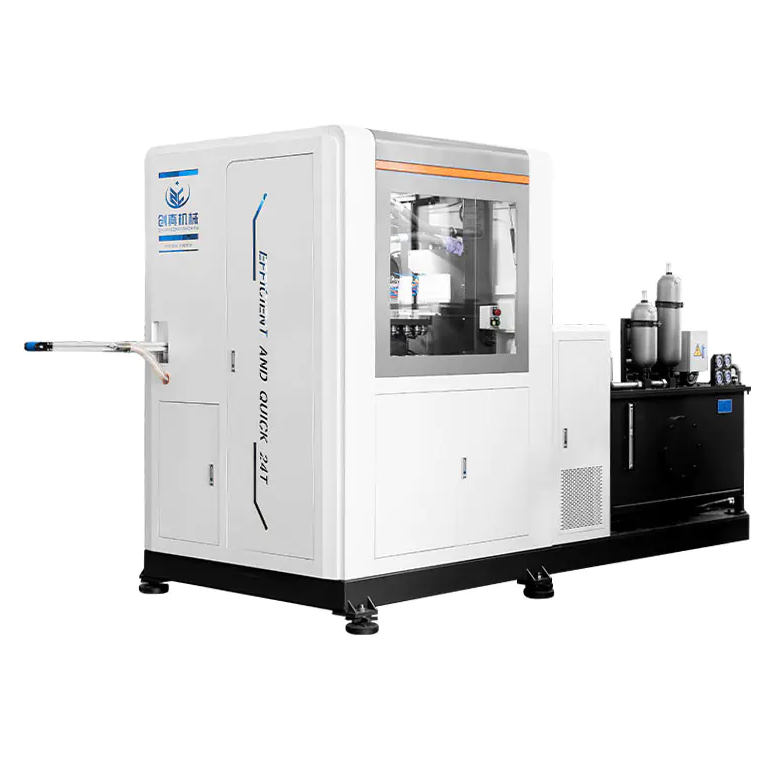
Manufacturing efficiency is a critical factor in determining the competitiveness and profitability of businesses. In the context of product packaging, cap compression machines have proven to be a valuable tool for improving production processes, increasing output, and reducing operational costs. These machines enhance the overall efficiency of packaging lines by offering reliable and precise capping solutions that meet the demands of modern manufacturing.
One of the primary ways in which cap compression machines improve manufacturing efficiency is through automation. Traditionally, capping processes were done manually or with less advanced machinery, which could lead to inconsistencies, slowdowns, and even product defects. By automating the capping process, cap compression machines ensure that each cap is applied consistently with the correct amount of pressure, reducing the risk of human error and ensuring a more efficient production flow.
In addition to automation, cap compression machines often incorporate features such as quick changeovers and adjustable settings, which can significantly reduce downtime. When switching between different cap sizes or types, traditional machines often require extensive adjustments and recalibration. Cap compression machines, on the other hand, are designed to facilitate easy modifications, allowing manufacturers to quickly adapt to different packaging requirements without significant delays. This flexibility can increase the overall throughput of the production line and ensure that a wide range of products can be processed using the same machine.
Another key aspect of efficiency is the reduction in material waste. Improperly sealed caps can lead to product spoilage or contamination, requiring the disposal of affected units and contributing to material waste. By providing a consistent seal every time, cap compression machines reduce the likelihood of product rejection due to faulty caps. This not only helps reduce waste but also ensures that materials are used more effectively, ultimately lowering production costs.
The enhanced reliability and precision of cap compression machines also contribute to improved product quality. A secure seal is essential to maintaining the freshness and integrity of products, particularly in industries where contamination or spoilage can result in significant financial losses. Cap compression machines help ensure that each product is properly sealed, which contributes to a higher-quality end product and a more reliable supply chain.
In conclusion, cap compression machines have a significant impact on manufacturing efficiency. By automating the capping process, reducing downtime, minimizing material waste, and ensuring consistent product quality, these machines help manufacturers streamline their operations and increase overall productivity. With the continued demand for faster and more reliable production lines, cap compression machines are likely to remain an essential part of modern manufacturing.
- Art
- Causes
- Crafts
- Dance
- Drinks
- Film
- Fitness
- Food
- Games
- Gardening
- Health
- Home
- Literature
- Music
- Networking
- Other
- Party
- Religion
- Shopping
- Sports
- Theater
- Wellness