Steel Forging Manufacturing Plant Project Report 2025: Key Steps, Challenges and Solutions
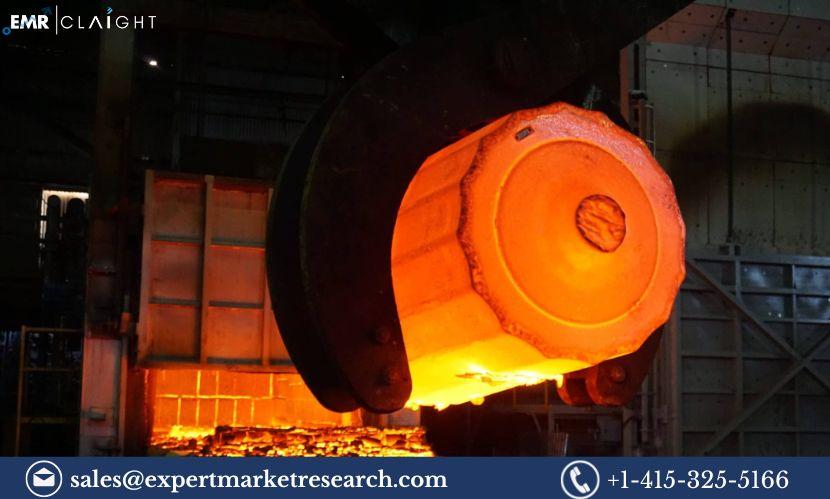
Introduction
Steel forging is a crucial process in the manufacturing of durable, high-performance components that are used in a variety of industries such as automotive, aerospace, construction, and machinery. The forging process improves the strength and durability of steel by shaping it under high pressure and temperature, making it an essential technique for producing parts that can withstand extreme conditions. A Steel Forging Manufacturing Plant Project Report is designed to guide potential investors and entrepreneurs in establishing a steel forging facility. This report covers all key aspects such as market analysis, raw materials, manufacturing processes, machinery, plant design, and financial planning. Whether you're entering the industry for the first time or expanding your existing operations, this comprehensive guide will help you navigate the complexities of setting up a successful steel forging manufacturing plant.
Market Overview and Demand Analysis
Steel forging plays a pivotal role in industries that require high-strength, reliable components. As global industrialization continues to rise, the demand for forged steel products is growing, especially in sectors like automotive, oil and gas, defense, and heavy machinery. Steel forged components are known for their superior mechanical properties, including enhanced tensile strength, ductility, and impact resistance.
Key factors driving the demand for steel forging include:
-
Growth in Automotive and Aerospace Sectors: Steel forged parts are widely used in automotive and aerospace manufacturing due to their ability to withstand high pressures and extreme temperatures. These sectors require high-performance materials for engine parts, transmission components, and structural elements.
-
Rising Infrastructure Development: The global rise in infrastructure projects, such as bridges, buildings, and heavy machinery, has led to increased demand for forged steel components used in structural supports, tools, and equipment.
-
Technological Advancements: Advancements in forging technology have led to the production of more complex and precise steel forged components. This has expanded the range of applications for forged steel products, increasing demand in industries such as electronics and medical devices.
-
Energy Sector Demand: The energy industry, including the oil and gas sector, relies heavily on forged steel components for drilling equipment, turbines, and pipelines. As global energy demand increases, the need for steel forging products continues to rise.
-
Wear and Tear Resistance: Forged steel parts are known for their ability to withstand wear and tear, making them ideal for high-stress applications like mining, heavy machinery, and manufacturing.
Given these driving factors, the steel forging industry is positioned for substantial growth, making it an attractive market for new businesses and investments. A thorough analysis of regional demand, competition, and pricing strategies is essential to developing a successful business plan.
Get a Free Sample Report with Table of Contents@
Regulatory Considerations
Establishing a steel forging manufacturing plant requires compliance with various regulatory standards to ensure product quality, worker safety, and environmental sustainability. Compliance with these regulations is essential for maintaining a reputable and legally compliant business.
Key regulatory considerations include:
-
Quality and Safety Standards: Steel forgings must meet stringent quality and safety standards, such as the ISO 9001 certification, which ensures that the manufacturing process and products meet international quality standards. Additionally, the ASTM (American Society for Testing and Materials) standards set requirements for the mechanical properties and testing of forged steel components.
-
Environmental Regulations: Steel forging is energy-intensive and produces emissions, making it subject to local and international environmental regulations. These regulations may govern air and water quality, waste management, and recycling of scrap metal. The plant must implement systems to reduce emissions, recycle materials, and manage waste responsibly.
-
Health and Safety: The steel forging process involves high temperatures and heavy machinery, which pose risks to worker safety. Regulatory bodies such as the Occupational Safety and Health Administration (OSHA) in the United States set safety standards for manufacturing facilities. These standards include proper machine guarding, ventilation, and personal protective equipment (PPE) for workers.
-
Labor Standards: In addition to worker safety, labor standards must be followed to ensure fair wages, working hours, and employee benefits. Depending on the region, labor laws may include worker compensation and collective bargaining agreements.
-
Certification for Export Markets: If the plant plans to export forged components internationally, it will need to comply with certification requirements specific to target markets. For example, components sold in the European Union may need CE marking, and those sold in the United States may need to meet National Aerospace and Defense Contractors Accreditation Program (NADCAP) standards.
Raw Materials for Steel Forging
The raw materials used in steel forging are essential to the final quality of the forged components. The primary raw materials include various types of steel alloys, which are selected based on the desired mechanical properties of the finished product.
Key raw materials include:
-
Steel Alloys: The most commonly used raw material in forging is steel, which can be alloyed with elements such as carbon, manganese, chromium, nickel, and molybdenum to enhance properties like strength, corrosion resistance, and heat resistance. The specific alloy composition is chosen based on the intended use of the forged components.
-
Scrap Metal: Recycled scrap metal is often used in the steel forging process. This reduces the demand for virgin raw materials and contributes to environmental sustainability. The scrap metal is melted down and purified before being formed into the desired shape.
-
Other Metal Additives: Depending on the type of steel and the desired characteristics of the final product, additional metals or additives such as boron, titanium, and vanadium may be used to improve strength, durability, or heat resistance.
Sourcing high-quality raw materials is essential for producing high-performance forged components. Establishing reliable relationships with suppliers and maintaining quality control throughout the sourcing process can help ensure consistency and minimize defects.
Manufacturing Process
The steel forging process involves several stages, each requiring precise control over temperature, pressure, and material flow to produce high-quality components. The general process includes:
-
Material Preparation: The raw steel or metal alloy is cut into billets or ingots, which are then heated to the appropriate temperature. The heating process is critical for ensuring the steel is malleable enough for forging.
-
Forging: The heated billets or ingots are placed in a forging press or hammer, where they are shaped into the desired form. The process can be done using different methods, such as:
- Open-die forging: The material is placed between two dies that do not completely enclose the piece. This method is typically used for larger parts.
- Closed-die forging: The material is placed in a die that completely encloses it. This method is used for more complex and precise shapes.
- Upset forging: This involves compressing the material in a way that increases its diameter, typically used for making bolts and nuts.
-
Heat Treatment: After the forging process, the components undergo heat treatment to refine their mechanical properties. Heat treatment processes such as annealing, quenching, and tempering help improve hardness, toughness, and fatigue resistance.
-
Machining: In many cases, forged components require additional machining to achieve the final dimensions and tolerances. This process includes turning, milling, grinding, and drilling.
-
Surface Finishing: After machining, the components undergo surface finishing processes such as polishing, coating, or painting to enhance corrosion resistance, improve appearance, and meet customer specifications.
-
Inspection and Quality Control: Each forged part is subjected to rigorous quality control measures, including dimensional checks, tensile tests, and non-destructive testing methods such as ultrasonic testing or X-ray inspection.
-
Packaging and Shipping: Once the components pass quality control, they are packaged and prepared for delivery to customers. Packaging must ensure that the parts are protected during transportation and handling.
Plant Layout and Design
The design of a steel forging plant should prioritize efficient workflows, safety, and environmental considerations. Key areas of the plant include:
-
Raw Material Storage: This area is dedicated to storing steel alloys, scrap metal, and other raw materials. The storage area should be organized and protected from contamination.
-
Forging Area: This is where the billets and ingots are heated and shaped under pressure. The forging area should have sufficient space for large presses or hammers, as well as proper ventilation systems to handle the heat and emissions.
-
Heat Treatment and Machining Areas: These areas are dedicated to post-forging processes, where components are heat-treated and machined to meet final specifications. Proper equipment and temperature controls are essential for achieving the desired properties.
-
Inspection and Testing Area: A quality control area equipped with the necessary tools and instruments to perform rigorous testing on the forged components. This area should be separate from the production line to avoid contamination.
-
Waste Management Area: A designated area for collecting and recycling waste materials such as metal shavings, scrap, and hazardous chemicals.
-
Packaging Area: A clean and secure space for packaging and preparing forged components for shipment.
-
Administrative and Support Areas: Offices, meeting rooms, and employee amenities to support the operational side of the business.
Machinery and Equipment
A steel forging plant requires specialized machinery to handle the intense pressures and temperatures associated with the forging process. Key machinery includes:
-
Forging Presses and Hammers: Used to shape the heated steel under pressure. These can be mechanical, hydraulic, or pneumatic.
-
Induction Furnaces: Used for heating steel billets to the required forging temperature.
-
Heat Treatment Furnaces: For conducting processes like annealing, quenching, and tempering.
-
CNC Machines: Used for precision machining of forged parts to meet tight tolerances.
-
Inspection Tools: Instruments such as hardness testers, tensile testers, and ultrasonic inspection equipment to ensure quality control.
-
Material Handling Equipment: Cranes, forklifts, and conveyors to move raw materials and finished parts around the plant.
Financial Projections and Investment Requirements
Starting a steel forging manufacturing plant requires a significant investment. Financial projections should include:
-
Capital Investment: Costs for land, plant construction, machinery, and raw material procurement.
-
Operating Costs: Ongoing expenses for labor, utilities, raw materials, and maintenance.
-
Revenue Projections: Expected revenue based on production volume, market demand, and pricing strategies.
-
Profitability Analysis: Break-even analysis and ROI calculations to assess the financial viability of the plant.
-
Funding Requirements: Potential financing options such as loans, equity investors, or grants.
Related Reports
https://www.expertmarketresearch.com/blogs/top-india-pos-device-companies
https://www.expertmarketresearch.com/blogs/top-high-performance-computing-companies
https://www.expertmarketresearch.com/blogs/top-gaming-console-companies
Media Contact
Company Name: Claight Corporation
Contact Person: Peter Fernandas, Corporate Sales Specialist
Email: sales@expertmarketresearch.com
Toll Free Number: +1–415–325–5166 | +44–702–402–5790
Address: 30 North Gould Street, Sheridan, WY 82801, USA
Website: www.expertmarketresearch.com
- Art
- Causes
- Crafts
- Dance
- Drinks
- Film
- Fitness
- Food
- Games
- Gardening
- Health
- Home
- Literature
- Music
- Networking
- Other
- Party
- Religion
- Shopping
- Sports
- Theater
- Wellness