The Customer's Guide to Cold Forming Machines
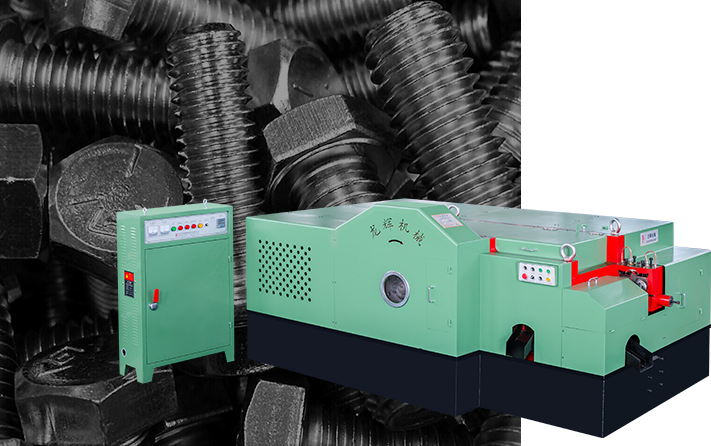
Cold forming machines have become an integral part of various industries, revolutionizing the way metal components are produced. From automotive to aerospace, these machines play a crucial role in shaping metal materials with precision and speed. In this customer-centric exploration, we delve into the world of cold forming machines, shedding light on their functionalities, advantages, and the impact they have on the manufacturing landscape.
Understanding the Basics: What Is a Cold Forming Machine
Before delving into the customer's perspective, it's essential to comprehend the fundamental nature of cold-forming machines. Essentially, these machines are designed to shape metal parts at room temperature or slightly above, as opposed to traditional hot forming methods. The process involves using force to deform and reshape metal materials, creating a wide array of components used in diverse industries.
Customer-Focused Benefits of Cold Forming Machines:
Now, let's explore the benefits that customers can expect when incorporating cold forming machines into their manufacturing processes.
Enhanced Material Utilization:
Optimized Raw Material Consumption
Customers appreciate cold forming machines for their ability to optimize raw material usage. The process generates less waste compared to traditional machining methods, contributing to cost savings and sustainable practices.
Improved Precision and Consistency:
Tight Tolerances and High Precision
Cold forming machines are renowned for their capability to achieve tight tolerances and high precision in the produced components. This ensures that customers receive consistently accurate parts, meeting their specifications with reliability.
Increased Production Speed:
Rapid Manufacturing Output
Time efficiency is a critical factor for customers in various industries. Cold forming machines excel in high-speed production, enabling manufacturers to meet demanding timelines without compromising on quality.
Cost-Effective Manufacturing:
Reduced Secondary Operations
Cold forming often requires minimal secondary operations, such as machining or finishing, resulting in cost-effective manufacturing. This appeals to customers looking for efficient and economical production processes.
Versatility in Component Design:
Complex Geometries and Shapes
Cold forming machines offer unparalleled versatility in shaping complex geometries and intricate part designs. This flexibility allows customers to explore innovative and intricate components for their applications.
Enhanced Material Strength:
Improved Material Characteristics
The cold forming process can enhance the mechanical properties of materials, resulting in components with improved strength and durability. This is particularly advantageous for industries requiring robust and reliable parts.
Reduced Energy Consumption:
Energy-Efficient Production
Customers focused on sustainable manufacturing practices appreciate the energy efficiency of cold forming machines. The process generally consumes less energy compared to traditional hot forming methods, aligning with environmental considerations.
Streamlined Production Workflow:
Integrated Production Processes
Cold forming machines contribute to a streamlined production workflow. Manufacturers can often integrate these machines into automated production lines, enhancing overall efficiency and reducing manual labor requirements.
Customer Testimonials: Real-World Perspectives on Cold Forming Machines
To provide a more tangible understanding of the customer's perspective, let's explore a few testimonials from industries that have embraced cold forming technology.
Johnathan Turner, Automotive Component Manufacturer:
"We've seen a significant shift in our production efficiency since incorporating cold forming machines. The speed at which we can produce intricate automotive components without compromising on quality has truly transformed our operations. The reduced material waste has also positively impacted our bottom line."
Linda Chen, Aerospace Industry Engineer:
"In aerospace, precision and strength are non-negotiable. Cold forming machines have become the backbone of our manufacturing processes. The ability to create complex and high-strength components has not only elevated our product quality but has also opened up new design possibilities."
Michael Rodriguez, Sustainable Manufacturing Advocate:
"As someone passionate about sustainable practices, the reduced material waste and energy-efficient nature of cold forming align perfectly with our goals. It's refreshing to see technology that not only enhances productivity but also contributes to a more eco-friendly manufacturing landscape."
Conclusion: Elevating Manufacturing Standards with Cold Forming Machines
In conclusion, the customer's journey into the realm of cold forming machines is marked by efficiency, precision, and a commitment to sustainable manufacturing practices. As industries continue to evolve, the demand for components that marry high-quality production with cost-effective and eco-conscious methodologies is on the rise. Cold forming machines stand as a testament to technological advancements that not only meet but exceed customer expectations. From automotive innovations to aerospace marvels, the influence of cold forming machines reverberates through diverse sectors, shaping the future of manufacturing with each precisely formed component. As customers seek solutions that enhance their production capabilities, cold forming machines emerge as indispensable tools, ushering in a new era of manufacturing excellence.
- Art
- Causes
- Crafts
- Dance
- Drinks
- Film
- Fitness
- Food
- Games
- Gardening
- Health
- Home
- Literature
- Music
- Networking
- Other
- Party
- Religion
- Shopping
- Sports
- Theater
- Wellness