Comparative Analysis of Railroad Spikes and Screw Fasteners
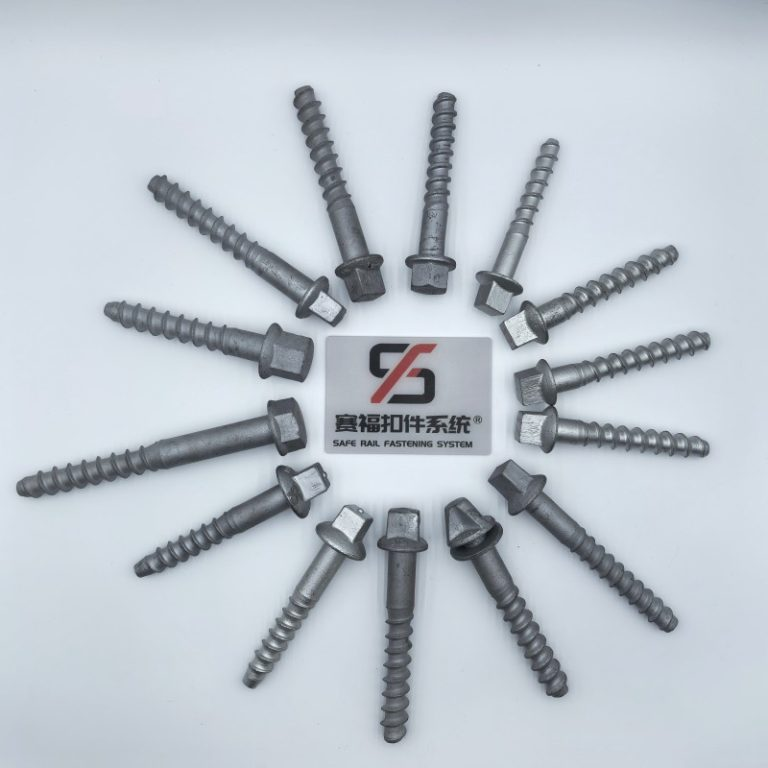
When it comes to the construction and maintenance of heavy-duty rail tracks, selecting the appropriate fasteners is crucial. The two primary options are railroad spikes and screw fasteners, each with its own set of advantages and disadvantages. Understanding these differences is key for railway professionals seeking to optimize track performance.
Overview of Railroad Spikes
Railroad spikes have been a staple in rail track construction for over a century. Their primary function is to secure the rail to the underlying tie, providing stability and alignment. Typically made from high-grade steel, railroad spikes are known for their robust design and ease of installation.
Examination of Screw Fasteners
Screw fasteners, on the other hand, represent a more modern approach to rail fastening. Unlike traditional spikes, screw fasteners are threaded, allowing for a more secure attachment to the rail tie. This design offers increased holding power and can be particularly beneficial in areas with high traffic or load demands.
Performance Metrics for Heavy-Duty Rail Applications
When evaluating fasteners for heavy-duty applications, several performance metrics must be considered to ensure optimal track functionality.
Load-Bearing Capacity
· Railroad Spikes: Generally provide adequate load-bearing capacity for standard applications but may struggle under extreme loads or high-speed conditions.
· Screw Fasteners: Offer superior load-bearing capabilities due to their threaded design, making them suitable for high-stress environments.
Durability and Longevity
· Railroad Spikes: While durable, they may require more frequent maintenance in heavy-duty scenarios due to wear and tear.
· Screw Fasteners: Known for their longevity; they maintain integrity longer under stress, reducing maintenance needs over time.
Installation Processes and Efficiency
The installation process is a critical factor when selecting between railroad spikes and screw fasteners, impacting both labor costs and time efficiency.
Installation Techniques for Railroad Spikes
· Tools Required: Hammer or spike driver
· Time Efficiency: Quick installation but may require more frequent checks
· Skill Level: Basic skill required; less precision needed compared to screws
Installation Techniques for Screw Fasteners
· Tools Required: Impact wrench or specialized equipment
· Time Efficiency: Longer initial installation time but offsets with reduced maintenance
· Skill Level: Higher precision needed; skilled labor recommended
Safety Considerations in Fastener Selection
Safety is paramount in railway operations. The choice between railroad spikes and screw fasteners can have significant implications on track safety protocols.
Risk Assessment for Railroad Spikes
· Potential Risks: Loosening over time can lead to misalignment
· Mitigation Strategies: Regular inspections and timely replacements are essential
Safety Protocols for Screw Fasteners
· Potential Risks: Over-tightening can damage ties or rails
· Mitigation Strategies: Use torque-controlled tools and adhere to manufacturer specifications
Selecting the right type of fastener is a complex decision that requires careful consideration of various factors including performance metrics, installation processes, and safety implications. Both railroad spikes and screw fasteners offer unique benefits suited to different operational needs in heavy-duty rail applications.
Economic Implications of Choosing Fasteners
The economic impact of selecting the appropriate fasteners for heavy-duty rail applications cannot be overstated. The choice between railroad spikes and screw fasteners involves an intricate analysis of cost, maintenance, and long-term financial implications.
Cost Analysis of Railroad Spikes
· Initial Purchase Cost: Generally lower than screw fasteners, making them a more budget-friendly option initially.
· Maintenance Costs: Tend to increase over time due to the need for regular inspections and replacements in high-stress environments.
· Overall Lifecycle Cost: While initial costs are low, frequent maintenance can lead to higher cumulative expenses over the lifespan of the rail track.
Financial Evaluation of Screw Fasteners
· Initial Purchase Cost: Higher upfront cost compared to railroad spikes, reflecting their advanced design and material quality.
· Maintenance Costs: Reduced frequency of maintenance due to enhanced durability and secure fastening reduces long-term expenses.
· Overall Lifecycle Cost: Although more expensive initially, the reduced need for repairs and replacements can result in lower overall costs over time.
Introduction to SAFE as a Reliable Supplier
When considering fastener options, partnering with a reputable supplier is crucial. SAFE has established itself as a leader in providing high-quality railroad spikes and screw fasteners tailored for heavy-duty applications.
Reputation in the Industry
· Industry Experience: Decades of experience in supplying rail fastening solutions across various sectors.
· Quality Assurance: Adherence to stringent quality standards ensures reliability and safety in all products offered.
· Customer Support: Comprehensive support services including technical advice and after-sales assistance enhance customer satisfaction.
Conclusion: Making an Informed Decision on Fastener Selection
Selecting between railroad spikes and screw fasteners requires careful consideration of various factors such as performance metrics, installation efficiency, safety implications, and economic impact. Each option presents unique advantages suited to specific operational needs. By evaluating these elements alongside trusted suppliers like SAFE, railway professionals can make informed decisions that optimize track performance and longevity.
FAQs on Railroad Spike and Screw Fasteners
What are the key differences between railroad spikes and screw fasteners?
Railroad spikes are traditional fasteners known for their ease of installation but may require more frequent maintenance. Screw fasteners offer superior holding power due to their threaded design, making them ideal for high-stress environments.
How do environmental conditions affect the performance of these fasteners?
Environmental factors such as temperature fluctuations, moisture levels, and soil composition can impact the performance of both types. Railroad spikes may loosen over time under adverse conditions, while screw fasteners provide better resistance but require precise installation to avoid damage.
Are there specific scenarios where one type is preferred over the other?
Railroad spikes are often preferred in standard applications where cost-efficiency is a priority. Screw fasteners are favored in scenarios demanding higher load-bearing capacity and reduced maintenance frequency, such as high-speed railways or areas with extreme environmental conditions.
- Art
- Causes
- Crafts
- Dance
- Drinks
- Film
- Fitness
- Food
- Games
- Gardening
- Health
- Home
- Literature
- Music
- Networking
- Other
- Party
- Religion
- Shopping
- Sports
- Theater
- Wellness