How to Accurately and Professionally Measure Your Screw and Barrel?
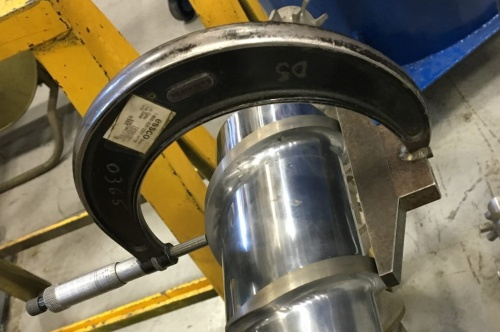
The screw and barrel are core components of extruders and injection molding machines, and their dimensional precision is critical to equipment performance. In practical applications, measuring screws and barrels involves not only basic geometric dimensions but also surface quality, fitting clearance, and material property assessments. This article provides a detailed overview of the tools, methods, steps, and key technologies for measuring screws and barrels, offering systematic guidance for production and quality control.
Measuring screws and barrels is a meticulous task requiring various tools and advanced techniques. The screw's thread geometry is complex, particularly in barrier sections or mixing zones, while the inner bore of the barrel is challenging to measure directly, necessitating specialized tools or non-contact technologies.
Methods for Measuring Screws
Measuring Key Dimensions:
Outer Diameter (D):
Use a vernier caliper or micrometer to measure multiple points along the screw's length, recording the maximum, minimum, and cylindricity deviations.
Pitch (P):
Ensure the thread pitch meets design specifications by using a gear pitch meter or optical measuring instrument.
Thread Depth (h):
Measure the distance from the bottom of the screw channel to the outer diameter using a depth gauge at designated points along the screw.
Compression Ratio:
Verify design parameters by calculating the ratio of channel depths in the feed, compression, and metering sections.
Surface Quality Inspection:
Roughness Measurement:
Use a portable surface roughness tester to scan the screw surface, ensuring the surface finish meets standard requirements (e.g., Ra < 0.8 μm).
Coating Thickness Measurement:
For screws treated with chrome plating or nitriding, measure the coating thickness using eddy current thickness gauges or X-ray fluorescence analyzers.
Geometric Tolerance Detection:
Concentricity:
Mount the screw on a specialized fixture or lathe and use a dial gauge to detect concentricity deviations in the threaded section.
Straightness:
Check the overall straightness of the screw on a flat guide rail using a laser straightness gauge.
Methods for Measuring Barrels
Measuring Inner Bore Dimensions:
Inner Diameter:
For small-diameter barrels, use an inside micrometer.
For large-diameter barrels, use a three-point bore gauge to ensure the inner diameter tolerance meets design requirements.
Inner Chamber Length:
Use a depth gauge or a specialized measuring rod to measure from the barrel's end face to the bottom of the inner chamber at multiple points.
Inspecting Inner Surface Quality:
Roughness Measurement:
Measure the inner wall's roughness using a flexible surface roughness tester to ensure optimal material flow performance.
Wear Assessment:
Compare inner diameter measurements to the original design specifications to calculate wear and determine the need for repair or replacement.
Roundness and Taper Measurements:
Roundness Detection:
Use a laser scanner or inside micrometer with circumferential measurements to check roundness.
Taper Measurement:
Measure the taper using a taper gauge or a Coordinate Measuring Machine (CMM).
Thermal Control Channel Inspection:
Internal Channel Blockage and Corrosion:
Inspect the internal cooling or heating channels using an endoscope to detect blockages or corrosion issues.
Pressure Testing:
Verify channel sealing and flow performance using pressure testing equipment.
Advanced Measurement Technologies
Coordinate Measuring Machines (CMM):
Perform three-dimensional geometric measurements of screws and barrels, particularly useful for complex surfaces and threaded cavities.
Advantages: High precision, digitized results, and automatic error analysis reporting.
Laser Scanners:
Quickly create 3D models of screw profiles, ideal for evaluating large screws' overall geometry.
Applications: Efficiently measure parameters like cylindricity and thread depth.
Ultrasonic Thickness Gauges:
Measure the barrel wall thickness, especially for assessing residual thickness after wear.
Advantages: Non-contact measurement, non-destructive, and suitable for various barrel materials.
Optical Measurement Instruments:
Use optical imaging systems for high-precision measurement of thread pitches and groove shapes.
Advantages: Non-contact methods eliminate mechanical interference, suitable for precision screws.
Analysis and Application of Measurement Data
Data Recording and Trend Analysis:
Maintain long-term records of measurement data to analyze screw and barrel wear trends.
Use this data to determine replacement cycles, optimize maintenance schedules, and reduce downtime costs.
Feedback to Manufacturing Processes:
Compare measurement results with design dimensions to guide production adjustments, enhancing manufacturing accuracy and consistency.
Quality Control and Acceptance:
Measurement data serves as a critical criterion for quality acceptance, ensuring compliance with standards.
Provide customized inspection reports for client-specific dimensions or tolerances.
- Art
- Causes
- Crafts
- Dance
- Drinks
- Film
- Fitness
- Food
- Games
- Gardening
- Health
- Home
- Literature
- Music
- Networking
- Other
- Party
- Religion
- Shopping
- Sports
- Theater
- Wellness