Optimizing Solvent Extraction Machine Parameters for Maximum Base Oil Recovery
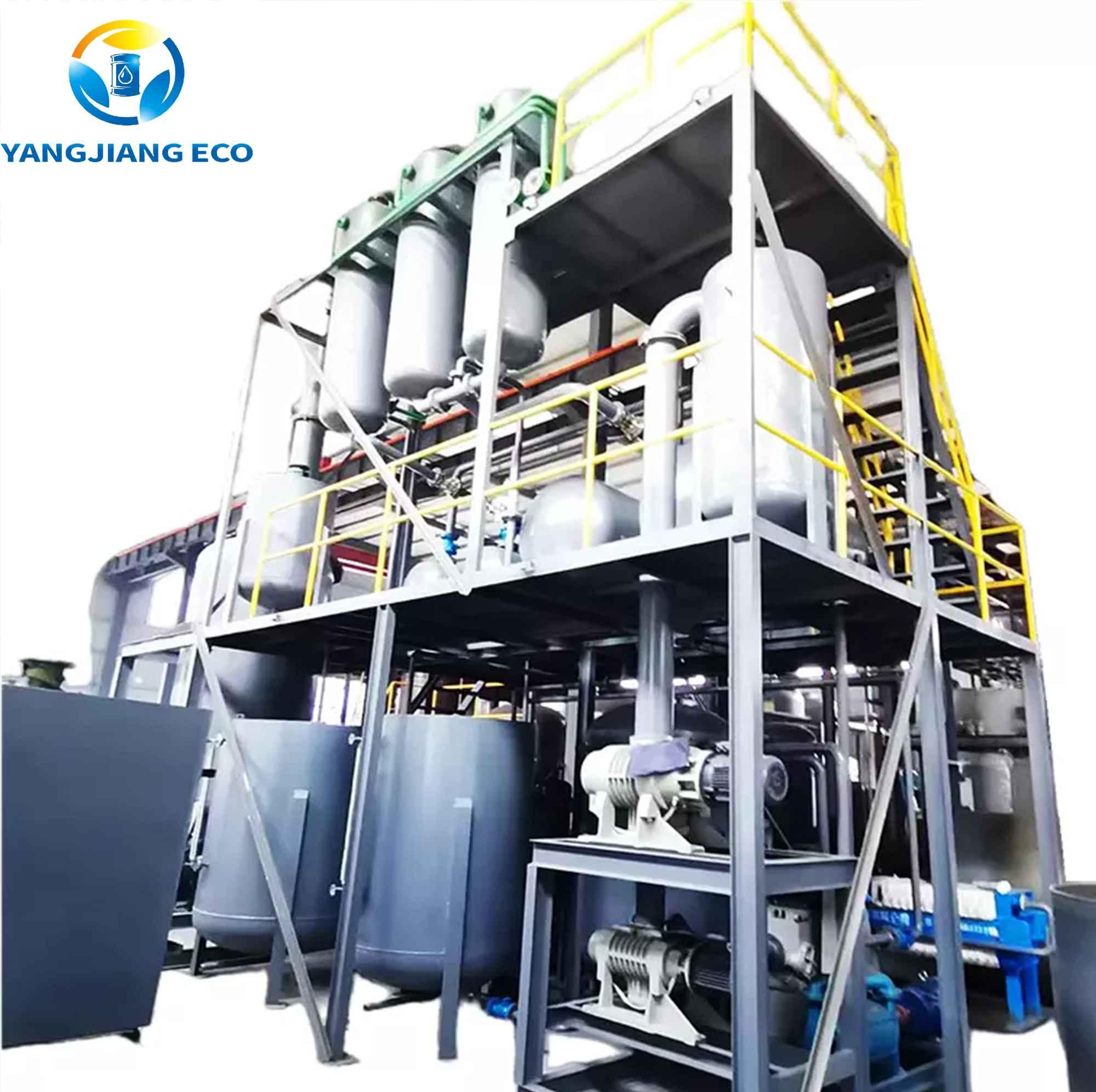
Solvent extraction is a critical process in the recycling and refining of used lubricating oils, allowing for the efficient recovery of high-quality base oils. By optimizing key machine parameters, industries can enhance oil yield, improve quality, and reduce operational costs. This blog explores the essential parameters that influence solvent extraction efficiency and how to fine-tune them for maximum base oil recovery.
1. Solvent-to-Oil Ratio
The solvent-to-oil ratio is one of the most crucial parameters in the extraction process. A higher ratio ensures better separation of impurities and contaminants from the base oil. However, excessive solvent use can lead to increased processing costs and the need for extensive solvent recovery. Finding the optimal balance—typically between 2:1 and 5:1—ensures effective impurity removal while maintaining economic feasibility.
2. Temperature Control
Temperature plays a significant role in solvent extraction by affecting the solubility of contaminants and the viscosity of the oil. An optimal temperature range, usually between 50°C and 80°C, enhances the separation process by reducing oil viscosity and improving the dissolution of undesired compounds. Operating outside this range may result in incomplete extraction or excessive energy consumption.
3. Mixing Intensity and Contact Time
Effective mixing ensures thorough interaction between the solvent and the oil, promoting efficient separation. High mixing intensity can improve extraction efficiency, but excessive agitation may cause unwanted emulsification, making phase separation difficult. Similarly, an optimal contact time—typically between 20 to 60 minutes—ensures maximum impurity dissolution without unnecessary processing delays.
4. Solvent Selection
Choosing the right solvent is essential for efficient base oil recovery. Commonly used solvents include furfural, N-methyl-2-pyrrolidone (NMP), and phenol. The ideal solvent should have high selectivity for contaminants, good solubility for impurities, and be easily recoverable for reuse. Evaluating the economic and environmental impact of the solvent is also necessary to ensure sustainable operations.
5. Phase Separation and Solvent Recovery
After extraction, efficient phase separation between the refined base oil and solvent is critical. Proper settling time, optimized decantation techniques, and the use of centrifugation can enhance separation efficiency. Additionally, a well-designed solvent recovery system, such as distillation or membrane separation, reduces solvent losses and operational costs.
Conclusion
Optimizing solvent extraction machine parameters is essential for maximizing base oil recovery while maintaining cost-effectiveness and environmental sustainability. By fine-tuning the solvent-to-oil ratio, temperature, mixing intensity, solvent selection, and phase separation techniques, industries can achieve higher yields and superior oil quality. Regular monitoring and process adjustments ensure continued efficiency, helping businesses optimize their refining operations for long-term success.
- Art
- Causes
- Crafts
- Dance
- Drinks
- Film
- Fitness
- Food
- Games
- Gardening
- Health
- Home
- Literature
- Music
- Networking
- Other
- Party
- Religion
- Shopping
- Sports
- Theater
- Wellness