Lost Foam Casting: A Comprehensive Guide for Industry Experts
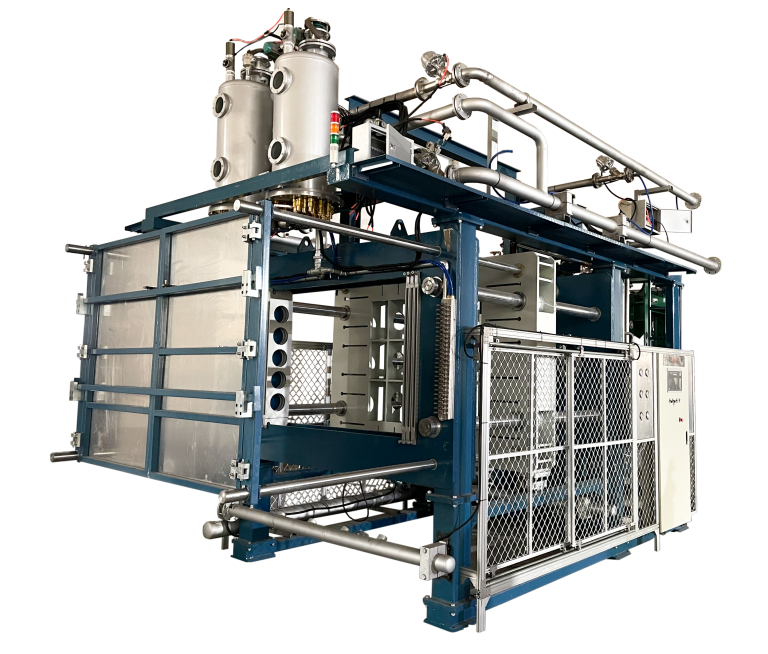
Understanding Lost Foam Casting
The Basics of Lost Foam Casting
Definition and Process Overview
Lost foam casting is a method, for creating metal components with details by utilizing a foam pattern coated in refractory material and encased in sand during the casting process. It involves pouring metal into the mold where the foam pattern evaporates to form a cavity that defines the shape of the final product. This approach enables the production of metal parts without extensive machining processes.
Historical Development and Evolution
Lost foam casting has been around since the middle of the century and was created as a clever way to make detailed castings with greater efficiency back then. Throughout the years that followed its inception; improvements in materials and methods have enhanced the process considerably; thus making it a top pick, for industries that seek precision and intricate designs in their cast products.
Key Components of the Lost Foam Casting Process
Pattern Creation and Material Selection
The initial stage of lost foam casting starts with the production of a pattern made from polystyrene or similar foams that can vaporize entirely without any leftover residues emphasizing the importance of material selection for this process accuracy and attention, to detail usually the use of computer design software (CAD).
Coating and Drying Techniques
After the foam design is ready for use, in casting workpieces it gets covered in a refractory mixture to form a tough shell capable of enduring the intense heat of molten metal. It's crucial to apply the coating to guarantee evenness in the finished cast product. Following the coating process the design is subjected to a drying phase to eliminate any moisture content that might lead to flaws during casting.
Advantages and Disadvantages of Lost Foam Casting
Benefits in Industrial Applications
Lost foam casting provides benefits such as lower machining needs because it can create components that are almost finished in shape. It also enables the production of shapes that would be difficult or not feasible using conventional techniques. Moreover, this method minimizes waste and energy use making it economical, for manufacturing runs.
Potential Limitations and Challenges
Although lost foam casting has advantages it also has drawbacks such as lead times resulting from the creation and drying of patterns and the need for meticulous control over factors like temperature and pressure to avoid issues such as porosity or incomplete filling Additionally setting up initially can be costly due, to tooling needs.
Materials Used in Lost Foam Casting
Types of Materials Suitable for Patterns
Polystyrene and Other Foams
Polystyrene is often utilized for making patterns because of its weight and malleability with other types of foams being selected based on factors, like thermal characteristics or environmental concerns as needed affecting the outcome and effectiveness of the production process.
Metal Alloys Commonly Used in Castings
Aluminum, Iron, and Steel Options
Lost foam casting can be used with a variety of metal alloys such as aluminum which is valued for its nature and which which offers strength and longevity Steel is known for its adaptability, in applications requiring high tensile strength Each type of alloy has its own set of challenges when it comes to melting points and flow behavior during the casting process.
Technical Aspects of Lost Foam Casting
Mold Design Considerations
Designing for Complexity and Precision
Design of molds is essential for outcomes in lost foam casting projects. A key consideration for designers includes factors such as shrinkage allowance and the setup of gating systems and vent paths to achieve replication of intricate shapes. Advanced simulation software is useful in anticipating challenges prior, to the start of production.
Process Parameters and Control
Temperature, Pressure, and Timing Factors
Managing process variables like temperature is crucial for melting the alloys without compromising their properties and controlling pressure helps regulate the flow of metal into complex mold sections reducing issues such as porosity and cold shuts. Timing is also vital as it involves coordinating pouring sequences to achieve thorough vaporization patterns ensuring a smooth transformation, from a molten state to a solidified form.
Applications of Lost Foam Casting the n the Industry
Automotive Industry Utilization
Engine Components and Structural Parts
Lost foam casting is widely used in the sector because it can create intricate and lightweight parts with great accuracy. This method is particularly beneficial for making engine parts like cylinder heads and intake manifolds as well as structural components such as suspension parts and brackets. The detailed designs produced through this process not only enhance engine performance but also help in reducing the overall weight of the components to improve fuel efficiency. Moreover; lost foam casting is favored for its ability to provide lightweight parts that are integral, to modern automotive engineering principles.
Aerospace Applications
Lightweight Components for Efficiency
In the aerospace industry, there is a demand for components that are both lightweight and strong. Lost foam casting addresses this requirement by allowing the creation of shapes that traditional techniques may not be able to achieve. Precision is key in crafting items like turbine blades, housing, and casings to guarantee notch aerodynamic performance and fuel efficiency. The technique's capability to make walled structures without sacrificing durability makes it perfect, for aerospace uses that prioritize weight reduction.
Innovations and Future Trends in Lost Foam Casting
Technological Advancements
Automation and Robotics Integration
The incorporation of automation and robotics into lost foam casting techniques marks a technological progressionUtomatedted mechanisms bolster accuracy and uniformity reducing mistakes and enhancing the general efficiency of production. Robotic systems can be utilized in generating patterns, application of coatings, and handling molds simplifying processes while maintaining quality checks. This shift towards automation not only boosts productivity but also provides more adaptability, in production timetables.
Sustainability Initiatives
Recycling Efforts and Environmental Impact Reduction
Efforts to promote sustainability in lost foam casting involve reducing harm by recycling materials and optimizing resources. Using materials in creating patterns helps cut down waste. Advancements in coating materials target emissions reduction, during the vaporization process. There are efforts to recycle sand from molds to further minimize environmental impact. These initiatives support industry goals of cutting carbon emissions and encouraging manufacturing practices.
Lost foam casting is constantly improving with advancements that make it suitable for a wide range of industries thanks, to its capability to create intricate parts while generating little waste making it a sought-after method in today's manufacturing sector that prioritizes effectiveness and eco-friendliness.
- Art
- Causes
- Crafts
- Dance
- Drinks
- Film
- Fitness
- Food
- Games
- Gardening
- Health
- Home
- Literature
- Music
- Networking
- Other
- Party
- Religion
- Shopping
- Sports
- Theater
- Wellness