Exploring PMSM Efficiency: A Deep Dive into Performance Metrics
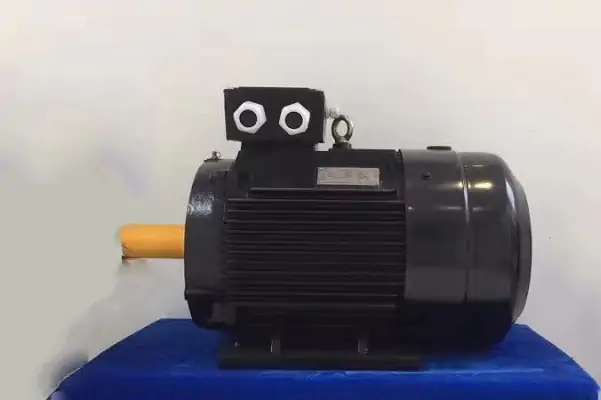
Understanding Permanent Magnet Synchronous Motors (PMSM)
Fundamentals of PMSM
Permanent Magnet Synchronous Motors (referred to as PMSMs) are a type of motors that utilize the magnetic field created by permanent magnets to generate torque efficiently and effectively. These motors operate synchronously with the supply frequency where the rotor's rotation is in sync with the current frequency. The key features that distinguish PMSMs include their capability to uphold speed even when dealing with different load conditions and their high power density which enables them to be used in various applications, across different industries.
Characteristics of PMSM
PMSMs exhibit several defining characteristics that contribute to their widespread use in industry. They offer high efficiency and power factor, which are critical for energy conservation and cost reduction. Additionally, PMSMs have a compact design due to the absence of brushes and slip rings, resulting in reduced maintenance requirements and increased reliability. The presence of permanent magnets eliminates the need for field winding, which further enhances their efficiency and performance.
Components and Design Aspects
The core components of a PMSM include the stator, rotor, and permanent magnets. The stator is typically made up of laminated silicon steel sheets with copper windings arranged in slots. The rotor contains permanent magnets that create a constant magnetic field. The design aspects focus on optimizing these components to achieve desired performance metrics such as torque density and thermal management. Advanced design techniques also involve selecting appropriate materials for minimizing losses and enhancing thermal conductivity.
Applications of PMSM in Various Industries
PMSMs find application across various industries due to their superior performance characteristics.
Automotive Sector
In the industry, PMSMs are becoming more common in electric cars because they are highly efficient and can provide significant torque at low speeds. This feature is beneficial, for enhancing vehicle acceleration and range while lowering energy consumption. Their small size also makes them easy to incorporate into vehicle designs without sacrificing space or weight limitations.
Industrial Machinery
PMSMs are commonly used in machinery for tasks that need precise control and efficiency like robotics and CNC machines as well as conveyor systems due to their capability to function at various speeds without compromising performance quality. Perfect for jobs that require speed adjustments! Additionally, PMSMs are known for their reliability and durability which help minimize downtimes in environments essential, for keeping productivity levels up!
Advantages of Using PMSM
Energy Efficiency Benefits
One of the primary advantages of using PMSMs is their energy efficiency. The absence of mechanical commutators reduces frictional losses, while the synchronous operation minimizes electrical losses associated with slip. This leads to lower energy consumption compared to other motor types like induction motors.
Reliability and Longevity
PMSMs offer enhanced reliability due to fewer moving parts susceptible to wear and tear. The use of permanent magnets eliminates brush-related issues found in traditional motors, resulting in longer operational life spans with minimal maintenance requirements.
Analyzing PMSM Performance Metrics
Key Performance Indicators for PMSM
Torque and Speed Characteristics
Producing torque plays a role in assessing the performance of PMSMs influencing their versatility for different uses directly High torque density enables efficient functioning even when handling diverse loads Speed attributes also hold significance ensuring steady speed under varying load conditions, for the best motor operati.on
Power Factor Considerations
Power factor is another essential metric influencing PMSM efficiency. A high power factor indicates effective utilization of electrical power, reducing reactive power losses within the system. Achieving an optimal power factor requires careful consideration during motor design and selection processes.
Efficiency Measurement Techniques
Testing Methods and Standards
Measuring efficiency includes using tests to assess how well a motor performs under certain conditions evaluating factors such as input power usage compared to the mechanical power output from the motor shaft, at various operating levels.
Role of Permanent Magnets
The decision to select among the magnetic materials currently available in the market impacts both the cost-performance ratios achievable, for end users and manufacturers. Both parties aim to optimize their investments to maximize profitability and achieve growth through careful and dedicated efforts.
Stator and Rotor Material Choices
Choosing the materials to build stators and rotors is crucial, for meeting the desired results set in advance. The planning process should be carried out carefully and thoroughly to ensure all aspects are covered comprehensively.
Influence of Design Parameters on Performance
The design parameters influence how well motors function for their intended purposes as outlined in contracts and agreements made by the parties involved. It is essential to conduct transactions ethically morally and in accordance, with legal requirements.
Winding Configurations
In scenarios, different winding structures are used based on specific needs that are influenced by the circumstances present, in each unique situation often arising unexpectedly and unpredictably.
Cooling Mechanisms
Maintaining operating temperatures is crucial for efficient cooling systems to prevent overheating and protect components ultimately extending the durability, strength,h, and resilience of the system.
Enhancing PMSM Efficiency Through Technological Innovations
Advances in Motor Control Technologies
The development of motor control technologies has played a role in improving the effectiveness of Permanent Magnet Synchronous Motors (also known as PMSMs). These progressions are essential, for maximizing motor efficiency cutting down energy usage, and andprolongingg the life of PMSMs.
Role of Inverters and Controllers
Inverters and controllers play a crucial role in the efficient operation of PMSMs. Modern inverters are designed to convert the direct current (DC) into alternating current (AC) with minimal losses, thereby ensuring that the motor operates at its optimal efficiency. Advanced controllers, on the other hand, manage the motor's speed and torque by precisely regulating voltage and current inputs. The integration of sophisticated control algorithms within these devices allows for real-time adjustments based on load conditions, enhancing overall system efficiency.
Software Algorithms for Optimization
Software algorithms play a role in enhancing the performance of PMSM by analyzing different factors like changes in loads and temperatures as well as fluctuations in power supply to adjust motor functions in real time effectively. These algorithms aid in anticipating maintenance needs and detecting faults to prevent failures and minimize operational interruptions. This no only boosts efficiency but also guarantees durability and trustworthiness, in PMSM use cases.
Emerging Trends in PMSM Design
Advancements in design are always expanding the limits of what PMSMs can accomplish by emphasizing improvements in performance and compatibility, with today's environments.
Lightweight Materials
The use of materials in the design of PMSM motors is becoming more popular as a way to increase efficiency.T he utilization of materials like carbon fiber composites and high-tech alloys serves to lessen the weight of motor parts while maintaining their strength. This decrease in weight results, in inertia which improves acceleration and decreases energy usage when in use.
Integration with IoT and Smart Systems
The integration of PMSMs with Internet of Things (IoT) technologies and smart systems represents a significant leap forward in motor efficiency. By connecting motors to IoT platforms, real-time data on performance metrics can be collected and analyzed remotely. This connectivity allows for proactive maintenance scheduling, energy usage optimization, and seamless integration with other smart devices within industrial ecosystems.
Challenges in Achieving Optimal PMSM Efficiency
Despite the progress, in technology we've made far; there are still numerous hurdles to overcome to fully optimize the efficiency of PMSMs.
Overcoming Thermal Management Issues
Thermal management is a critical aspect that influences the performance and durability of PMSMs. Excessive heat generation can lead to inefficiencies and potential damage to motor components.
Heat Dissipation Techniques
Effective heat dissipation techniques are essential for maintaining optimal operating temperatures within PMSMs. Innovations such as advanced cooling systems using liquid or air-based methods have been developed to enhance thermal conductivity. Additionally, incorporating phase change materials that absorb excess heat during peak operations helps maintain stability and prevents overheating.
Addressing Cost-Effectiveness Concerns
Achieving a balance between keeping costs in check and meeting the demanding performance standards continues to pose an obstacle, for both manufacturers and end users.
Balancing Performance with Budget Constraints
Striking a harmony between boosting performance and staying within budget calls for choices when it comes to picking materials, design intricacy, and manufacturing techniques. Using materials without sacrificing quality or effectiveness is key, to keeping prices competitive while ensuring top-notch product performance.
Future Prospects for PMSM Development
The future development of PMSMs holds promising prospects across various sectors due to ongoing research efforts aimed at further enhancing their capabilities.
Potential for Increased Adoption Across Sectors
With industries emphasizing energy efficiency and sustainability nowadays the use of PMSMs is set to rise in various sectors, like automotive, aerospace, renewable energy systems, and industrial automation. Their exceptional efficiency features make themwell-suitedd for tasks that require control and minimal environmental effects.
Research Directions for Enhanced Efficiency
I can rewrite the text can you please provide the input text? Research projects aimed at improving the efficiency of PMSM are exploring pathways such as advancements in materials science and enhanced manufacturing techniques like 3D printing. They are also looking into cooling solutions that leverage nanotechnology to reduce losses related to factors, like electrical resistance and magnetic hysteresis. The goal is to achieve overall efficiencies consistently across different operating conditions worldwide. These efforts arewidespready. Valued in industry, academia, and regulatory bodies for promoting collaboration and achieving mutually beneficial outcomes through sustainable and ethical practices.
- Art
- Causes
- Crafts
- Dance
- Drinks
- Film
- Fitness
- Food
- Games
- Gardening
- Health
- Home
- Literature
- Music
- Networking
- Other
- Party
- Religion
- Shopping
- Sports
- Theater
- Wellness