Exploring Lost Foam Casting Maturation Silo for Quality Improvement
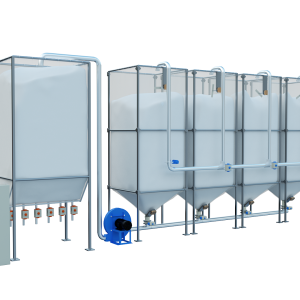
Understanding Lost Foam Casting Maturation Silo
Definition and Purpose
Specialized structures known as maturation silos for lost foam casting play a role in improving the quality of castings by creating a controlled setting for curing and solidifying foam patterns. These silos are essential in the casting process as they guarantee that the patterns attain their mechanical characteristics prior, to being utilized in metal casting operations.
Key Components of the Maturation Silo
The key components of a maturation silo include temperature control systems, humidity regulation mechanisms, and structural supports designed to maintain the integrity of foam patterns. These elements work in harmony to create a stable environment that promotes uniform maturation.
Role in the Casting Process
During the casting procedure maturation silos are crucial as they help stabilize foam patterns and achieve the desired strength and dimensional accuracy required for producing notch final products with minimal flaws.
Historical Development
Evolution Over Time
Over the years the idea of maturation silos has been. Improved thanks to advancements in materials and design resulting in systems that are now more efficient and effective.. Originally these silos were enclosures but they have since transformed into complex units, with cutting-edge control capabilities.
Major Milestones
Significant advances in the evolution of maturation silos involve the implementation of automated control systems alongside upgraded insulation materials and the incorporation, of monitoring technologies. These advancements have led to efficiency and dependability.
Mechanisms of Quality Improvement in Lost Foam Casting
Factors Affecting Quality in Casting
Material Selection and Preparation
The effectiveness of lost foam casting greatly depends on the choice and readiness of materials used in the process ashigh-qualityy materials are essential for ensuring that foam patterns have the required characteristics for casting outcomes while proper preparation methods also play a significant role, in enhancing these qualities.
Process Control Measures
It is crucial to put in place measures for process control to ensure consistency and reduce differences in casting outcomes effectively such as closely monitoring environmental conditions, in maturation silos, and following standardized procedures diligently.
Impact of Maturation Silo on Quality
Reduction of Defects
Maturation containers play a role in lowering defects by creating a space that helps prevent common problems, like shrinking and warping while improving surface quality.
Enhancement of Surface Finish
Using maturation silos enhances the quality of surface finish by promoting the hardening of foam patterns which in turn results in a smoother surface, for cast products that improve their appearance and functionality alike.
Technological Advances in Maturation Silos
Innovations in Design and Materials
Improved Insulation Techniques
Innovations of late have been directed towards enhancing insulation methods, in maturation silos utilizing ccutting-edgematerials with thermal resistance to uphold stable internal environments.
Advanced Monitoring Systems
Utilizing monitoring systems enables the continuous collection of real-time data concerning temperature and humidity as well as other essential factors crucial to the process, at hand.
Integration with Modern Manufacturing Processes
Automation and Digitalization
Automation has become a key aspect of modern maturation silos, reducing human intervention and increasing efficiency. Digitalization facilitates seamless integration with other manufacturing processes, streamlining operations.
Compatibility with Industry 4.0
The advancement of silos is aligning more with Industry 4. Initiatives, by using devices to improve connectivity and data sharing. This alignment helps in promoting manufacturing methods and better decision-making processes.
Challenges and Solutions in Implementing Maturation Silos
Common Obstacles Faced by Manufacturers
Cost Implications
Manufacturers often encounter a hurdle when it comes to the expenses involved in setting up sophisticated maturation silos. The upfront costs can be substantial; however, the advantages, in the run usually outweigh these expenditures.
Space and Infrastructure Requirements
When integrating maturation silos, into existing facilities dealing with limited space presents difficulties that need to be addressed to ensure that the existing operations are not disrupted by the addition of new structures.
Strategies for Overcoming Challenges
Efficient Resource Allocation
To address cost-related obstacles effectively in manufacturing settings requires strategic resource allocation prioritizing areas to maximize returns, within budget limits.
Training and Skill Development
Ensuring that employees receive training programs helps them acquire the necessary skills to effectively manage advanced maturation silos while continuous skill enhancement encourages flexibility in adapting to changing technologies.
Future Trends in Lost Foam Casting Maturation Silo
Emerging Technologies and Their Potential Impact
AI and Machine Learning Applications
AI and machine learning have the potential to improve maintenance, in industrial settings by allowing for better forecasting of maintenance requirements through detailed analysis of historical data.
Sustainable Practices
The significance of sustainability is on the rise in manufacturing practices that utilize lost foam casting techniques with upcoming developments centered on environmentally friendly materials, for constructing silos and implementing energy-saving operational approaches.
Predictions for Industry Growth and Development
Market Dynamics
There is an increasing need for notch cast products in industries like automotive, aerospace, and medical devices. This trend fuels innovation in lost foam casting methods with a focus, on enhancing efficiency, effectiveness, and the overall profitability of production cycles. Improved methodologies are being applied across the value chain ecosystem to elevate maturity stages and boost margins.
Regulatory Changes
The evolving regulatory landscape plays a role in influencing the adoption rates and compliance standards for new technologies with a focus on safety and environmental concerns. Manufacturers must keep abreast, of these changes to align with practices and reduce risks related to noncompliance which could lead to penalties, fines, a nd reputational harm if they fail to adhere to the established guidelines set by industry governing bodies.
- Art
- Causes
- Crafts
- Dance
- Drinks
- Film
- Fitness
- Food
- Games
- Gardening
- Health
- Home
- Literature
- Music
- Networking
- Other
- Party
- Religion
- Shopping
- Sports
- Theater
- Wellness