Understanding Crane Winch Mechanics: A Comprehensive Guide
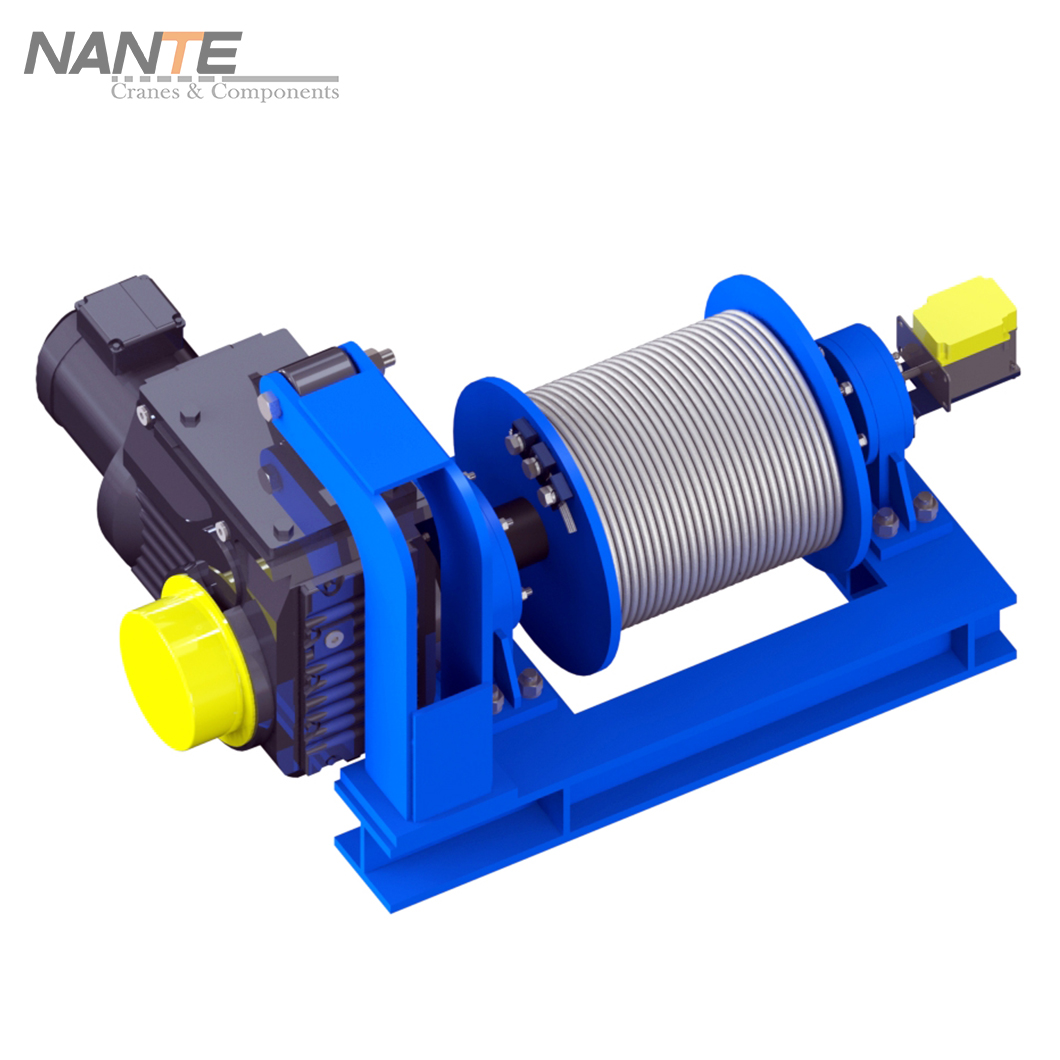
Fundamentals of Crane Winch Systems
Components of a Crane Winch
Drum and Cable
The drum is a part that houses the cable needed for lifting things up and down smoothly and safely in a winch system.
Motor and Brake System
The engine supplies the power needed to run the winch on the crane by transforming hydraulic energy into mechanical strength. The safety is guaranteed by the brake system which keeps the load stable as needed and can handle stops without risking stability.
Gearbox and Transmission
The gearbox adjusts the speed and strength of the motor to meet lifting needs while transmission systems guarantee effective power transfer from the motor to the drum emphasizing the importance of top-notch gears, for seamless functioning and durability.
Basic Principles of Operation
Load Lifting Mechanism
This method entails transforming movement into a straight movement to raise objects vertically. The effectiveness of this procedure is influenced by elements such as gear ratios, motor strength,th and cable durabili ty. Adequate coordination, among the parts guarantees functionality.
Control Systems and Safety Features
Operators can use control systems to handle speed and direction while managing loads effectively. To ensure safety during operations and prevent accidents key features like overload protection and safe brakes are essential. Emergency stop buttons are also crucial, for intervention when needed.
Types of Crane Winches and Their Applications
Electric Crane Winches
Advantages in Industrial Use
Electric crane winches are popular due to their nature and seamless integration into automated systems They provide reliable performance with low maintenance needs which makes them suitable for ongoing tasks, in industrial environments.
Common Application Scenarios
These types of winches are frequently employed in factories,\ warehouses,\. Building sites where accurate management of lifting loads is crucial.
Hydraulic Crane Winches
Benefits for Heavy-Duty Operations
Hydraulic crane winches offer power performance which makes them ideal, for demanding tasks requiring heavy lifting capacity and strong torque capabilities to handle larger loads effortlessly.
Typical Usage Environments
These winches are commonly used in settings, like drilling rigs and mining sites as well as in large construction projects that require strong performance capabilities.
Manual Crane Winches
Suitability for Specific Tasks
Manual crane winches are ideal for applications that need lifting solutions without depending on external power supplies providing versatility in remote areas or environments with restricted access, to electricity or hydraulics.
Limitations and Considerations
Manual winches may offer savings in costs. Have restrictions regarding the amount of weight they can handle and their speed capabilities as well. They demand an amount of physical exertions from operators which could be seen as a disadvantage especially, for tasks involving frequent or heavy lifting requirements.
Design Considerations in Crane Winch Manufacturing
Material Selection for Durability
Metals and Alloys Used
Strong metals, like steel alloys, are often chosen for making crane winch parts because they can withstand stress well impacting how well the crane works and how long it lasts.
Corrosion Resistance Factors
Ensuring durability over time is essential, in challenging conditions where corrosion can be a problem. Applying coatings or treatments can help improve resistance to rust and wear.
Engineering Specifications
Load Capacity Calculations
To make sure winches can safely lift the intended loads without any chance of failure is vital to have calculations in place Factors such, as the size of the drum cable strength and motor power are taken into account when doing these calculations.s
Safety Standards Compliance
Ensuring safety during the design phase is essential, by following industry safety regulations rigorously which helps reduce potential risks related to mechanical malfunctions or mistakes made by operators.
Maintenance Practices for Optimal Performance
Regular Inspection Protocols
Identifying Wear and Tear
Regulacheckupsps are crucial in spotting signs of wear like frayed cables orworn-outt gears to avoid more extensive damage, in the future.
Scheduled Lubrication Routines
Applying lubrication helps lessen the resistance between components in motion and prolongs their durability over time. Regular lubrication schedules are crucial, for keeping machinery operating smoothly and efficiently by preventing overheating and minimizing wear and tear.
Troubleshooting Common Issues
Addressing Motor Failures
Issues with motors can stem from problems with the system or internal mechanical issues, within the motor itself, and fixing these requires specialized knowledge to efficiently get things running smoothly again.
Resolving Gearbox Problems
Issues, with the gearbox,x frequently arise from either gear being misaligned or damaged leading to noise or decreased efficiency when in use. Regularly checking for maintenance can catch problems before they become more serious.
Innovations and Future Trends in Crane Winch Technology
Advancements in Automation
Integration with Smart Systems
Advancements in automation allow for connections, to smart systems providing better oversight of operations through remote monitoring tools or programmable logic controllers (PLCs).
Impact on Efficiency and Safety
Automated systems boost productivity by minimizing mistakes made by people and enhancing safety, with withstate-of-the-artt monitoring features that offer real-time data analysis throughout operations.
Sustainable Practices in Production
Eco-Friendly Materials
Manufacturers are more and more prioritizing the use of friendly materials to reduce their impact on the environment while still meeting the high standards, for quality and performance demanded by today's industries.
Energy-Efficient Designs
In today's landscape,e there is a significant focus on sustainability across various industries making it crucial to adopt energy-efficient designs that not only ensure high performance but also lower overall power consumption, during operation.
- Art
- Causes
- Crafts
- Dance
- Drinks
- Film
- Fitness
- Food
- Games
- Gardening
- Health
- Home
- Literature
- Music
- Networking
- Other
- Party
- Religion
- Shopping
- Sports
- Theater
- Wellness