Exploring the Role of Hydraulic Vane Pump in Modern Machinery
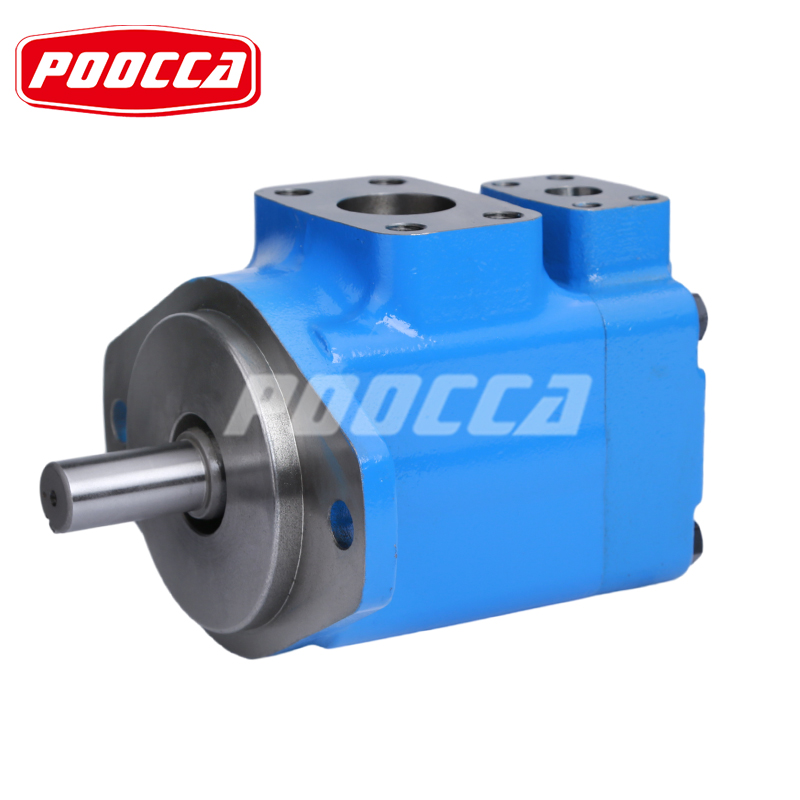
Understanding Hydraulic Vane Pumps
Basic Principles of Hydraulic Vane Pumps
Hydraulic vane pumps function based on the concept of displacement using vanes attached to a rotating rotor within a cavity. When the rotor turns the vanes move back and forth forming chambers of changing sizes. The fluid enters these chambers through an inlet. Is carried to an outlet as the chamber size shrinks leading to pressurized fluid. This process enables fluid movement and pressure creation to play a crucial role, in different machine setups.
Types of Hydraulic Vane Pumps
Different kinds of vane pumps are available to meet specific operational requirements efficiently and effectively; Fixed displacement vane pumps guarantee a steady flow rate that is ideal for applications needing a constant fluid supply while variable displacement vane pumps provide the flexibility of adjusting flow rates to ensure precise control, in dynamic systems; Moreover balanced vane pumps are designed to reduce side loads placed upon bearings which boosts their durability and overall performance; These diverse options allow for customization according to the specific needs of machinery.
Applications in Modern Machinery
Industrial Applications
Hydraulic vane pumps play a role in industrial environments that demand accurate fluid management and optimal performance levels. They are commonly employed in manufacturing operations like injection molding. Die casting relies heavily on maintaining consistent pressure levels. Their versatility in handling viscosities makes them well-suited for lubrication systems and cooling setups. Additionally, the compact design of these pumps allows for integration, into intricate machinery configurations while preserving space and operational efficiency.
Automotive Applications
In the world of cars hydraulic vane pumps are components in power steering setups and automatic transmissions They help maintain steady pressure for smooth steering and effective gear changes These pumps are popular in modern vehicles due to their compact size and dependable performance which is crucial for vehicles, with limited space They greatly enhance safety and ease of driving by offering reliable hydraulic power.
Advantages of Using Hydraulic Vane Pumps
Efficiency and Performance Benefits
Hydraulic vane pumps are well known for their volumetric efficiency thanks to minimal internal leakage. This effectiveness leads to energy usage and operational expenses. The design promotes a flow of fluid with minimal pulsation, which improves system stability and performance. Moreover, their ability to manage a range of pressures makes them adaptable, for different uses.
Durability and Reliability
The design of vane pumps focuses on durability by creating parts that can endure tough working conditions effectively top-notch materials minimize damage. Prolong the lifespan of the pumps even during constant usage. Their sturdy build guarantees performance with minimal upkeep needs leading to lower downtime, in crucial operations.
Technological Advancements in Hydraulic Vane Pumps
Innovations in Design and Materials
Lately, there have been improvements in refining the construction of hydraulic vane pumps to boost efficiency while also making them more compact and lighter in weight. A notable advancement is the adoption of cutting edge materials that provide better strength, to weight ratios when compared to conventional metals. These innovations lead to lighter pumps yet sturdier enabling them to achieve increased performance levels.
Integration with Smart Technologies
The use of technologies has transformed the way hydraulic vane pumps function by allowing for live monitoring and diagnostics. The sensors inside the pump offer insights into performance indicators like temperature pressure, and flow rate. These details are valuable, for implementing maintenance plans that help prevent sudden breakdowns and prolong the lifespan of the pump.
Challenges and Considerations in Implementation
Potential Limitations and Drawbacks
While hydraulic vane pumps offer benefits they also come with drawbacks like being prone to contamination issues that may cause wear or breakdown if not handled carefully. They also demand machining, during production which can raise the initial expenses when compared to alternative pump varieties.
Best Practices for Optimal Use
To get the most out of vane pumps and ensure they work efficiently over time it's crucial to follow recommended maintenance routines which involve inspecting for any impurities and making sure they are adequately lubricated. Choosing the type based on the particular requirements of the application is key to getting top-notch performance and reducing the risk of problems stemming from improper use or environmental impacts, on pump functionality.
- Art
- Causes
- Crafts
- Dance
- Drinks
- Film
- Fitness
- Food
- Games
- Gardening
- Health
- Home
- Literature
- Music
- Networking
- Other
- Party
- Religion
- Shopping
- Sports
- Theater
- Wellness