How to Optimize Your Designs for Aluminum CNC Machining
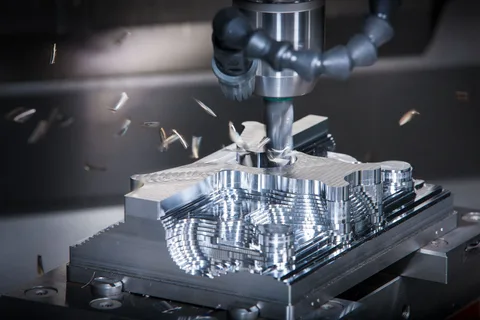
Aluminum is one of the most widely used materials in CNC machining due to its lightweight nature, excellent machinability, and high strength-to-weight ratio. Unlike other metals, aluminum offers superior corrosion resistance and thermal conductivity, making it ideal for aerospace, automotive, and industrial applications. Its relatively low melting point and ease of forming further enhance its suitability for precision CNC machining processes.
However, optimizing designs for Aluminum CNC Machining requires an understanding of its mechanical properties. Aluminum is softer than steel, which means it is more susceptible to deformation under excessive force. To prevent machining errors, designers should take into account factors such as tool selection, cutting speed, and feed rates. Properly understanding these properties ensures efficient and precise machining outcomes.
Selecting the Right Aluminum Alloy for Machining
Not all aluminum alloys are created equal when it comes to CNC machining. Commonly used aluminum grades include 6061, 7075, and 2024, each offering different strengths and applications. 6061 aluminum is the most versatile, balancing strength, corrosion resistance, and cost-effectiveness, making it ideal for general machining. On the other hand, 7075 aluminum is preferred for high-stress applications due to its superior strength but is more challenging to machine.
When selecting an aluminum alloy for CNC machining, factors such as hardness, machinability, and intended application must be considered. Softer alloys like 1100 or 3003 are easier to machine but may lack the strength required for load-bearing components. Choosing the appropriate alloy ensures that the final part meets performance expectations while minimizing machining challenges.
Optimizing Design Geometry for CNC Machining
One of the critical aspects of optimizing designs for Aluminum CNC Machining is simplifying the part geometry. Overly complex designs can lead to increased machining time, higher costs, and greater chances of errors. To enhance machinability, designers should incorporate fillets instead of sharp internal corners, which reduce stress concentration and allow smoother tool paths.
Additionally, minimizing deep cavities and ensuring uniform wall thickness can prevent tool deflection and vibration during machining. Maintaining a balance between design complexity and manufacturability ensures that CNC machines can efficiently produce high-quality aluminum components without excessive rework or tool wear.
Choosing the Right Tooling and Machining Parameters
Tool selection plays a significant role in achieving precision and efficiency in Aluminum CNC Machining. High-speed steel (HSS) and carbide tools are commonly used, with carbide tools being the preferred choice for high-speed applications due to their durability and heat resistance. Coatings such as titanium nitride (TiN) can further enhance tool life and performance when machining aluminum.
Machining parameters such as spindle speed, feed rate, and depth of cut should be optimized based on the selected aluminum alloy. Higher spindle speeds combined with moderate feed rates typically yield better surface finishes and reduce tool wear. Using appropriate coolants and lubricants also helps in heat dissipation, preventing material deformation and ensuring precise cuts.
Implementing Effective Workholding and Chip Management Strategies
Proper workholding is essential for maintaining stability during CNC machining. Aluminum parts can be prone to vibration and movement, which may affect dimensional accuracy. Using precision vises, clamps, or vacuum fixtures ensures that the workpiece remains securely positioned throughout the machining process.
Additionally, effective chip evacuation is crucial to prevent tool clogging and overheating. Aluminum produces long, stringy chips that can interfere with machining operations if not managed correctly. Implementing high-pressure coolant systems or chip-breaking techniques, such as using specialized tool geometries, can improve efficiency and maintain optimal machining conditions.
By following these optimization strategies, manufacturers can enhance productivity, reduce material waste, and achieve high-quality aluminum CNC machined components. Proper design considerations, material selection, and machining parameters work together to streamline production and ensure superior end-product performance.
- Art
- Causes
- Crafts
- Dance
- Drinks
- Film
- Fitness
- Food
- Games
- Gardening
- Health
- Home
- Literature
- Music
- Networking
- Other
- Party
- Religion
- Shopping
- Sports
- Theater
- Wellness